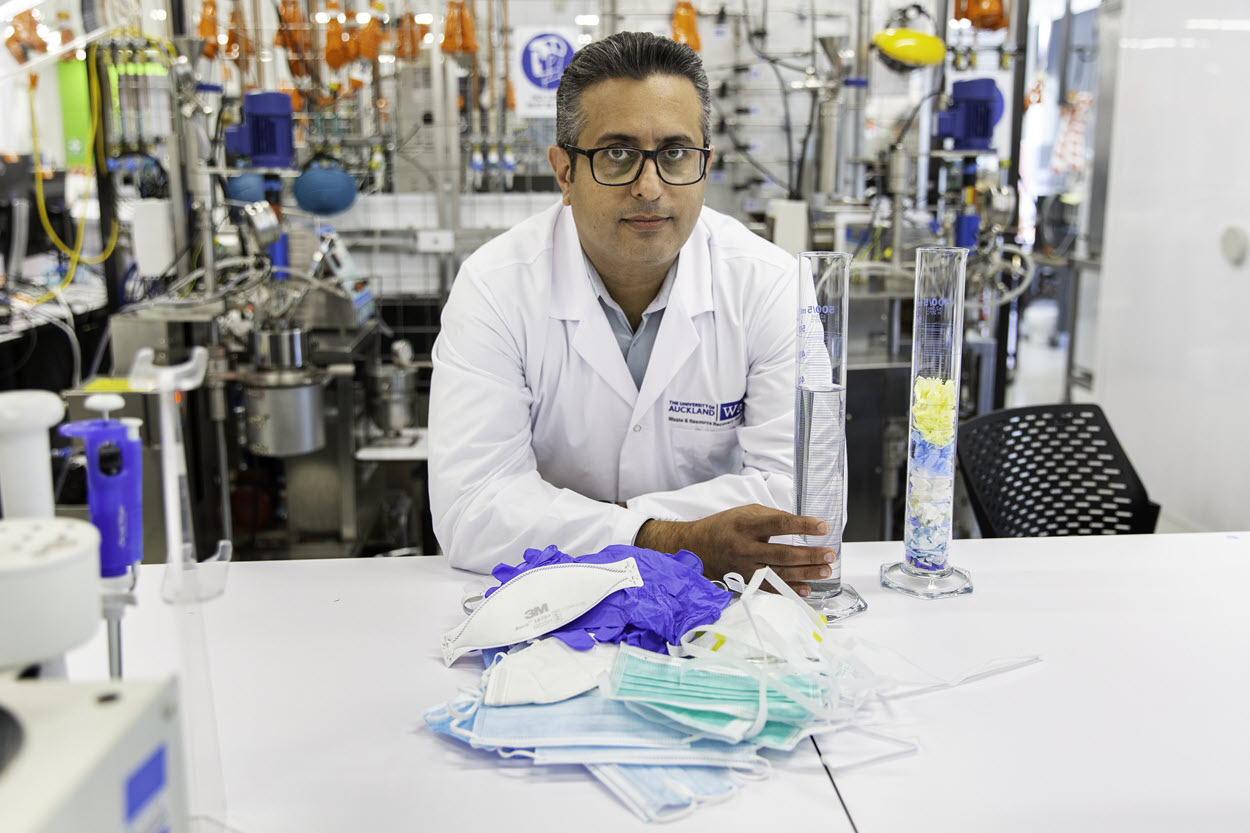
Two complementary methods to reduce the amount of personal protective equipment (PPE) waste have been developed by researchers at the University of Auckland in New Zealand.
The first solution can disinfect PPE for it to be reused and the second solution turns non-recyclable PPE into water and acetic acid, instead of it remaining for hundreds of years in the ocean or landfill.
Dr Saied Baroutian, associate professor, Department of Chemical and Materials Engineering, Faculty of Engineering, University of Auckland, says: “We are closing the loop on single-use PPE.”
He adds: “First, we disinfect and reuse PPE, which allows us to conserve their supply in the event of pandemic surges or supply chain issues. However, not all PPE can be reused due to material damage or contamination from organic matter. That means a considerable amount of waste still needs to be treated and disposed of efficiently and in an environmentally sound manner.”
The disinfection technology project is led by Dr Yvonne Anderson from the Department of Paediatrics at the university. Her team’s process works by applying dry heat to the PPE, which can inactivate bacterial pathogens and SARS-CoV-2.
Baroutian says the process is scalable, clean and has a low footprint. It has the potential to be implemented in healthcare and airport settings and could also be adapted for the treatment of other forms of hazardous waste.
The team has now designed, built and tested a prototype mobile disinfection unit in a shipping container at the port of Taranaki, New Zealand. This has since been demobilised and transferred to the University of Auckland to be integrated with the second solution to dispose of PPE waste.
Anderson says: “It’s fantastic that this work has the potential to reduce the impact of PPE on the environment and ensure an ongoing safe supply of PPE, even in the event of supply shortages.”
As mentioned, the second method safely disposes of non-recyclable PPE. The process begins by putting shredded masks, gowns, gloves and plastic safety glasses into a machine where pressurised water and compressed air are applied.
The process is carried out at a temperature of 300°C. Water at high temperatures such as this has unique properties, says Baroutian – it’s a very strong solvent and highly reactive. The team also uses air to pressurise the hydrothermal system and again at high temperatures, the oxygen molecules initiate a series of oxidation reactions in water.
In this instance, the long-chain polymers are converted into water and acetic acid. The water can be recycled back into the process and the acetic acid can be used as a disinfectant moving forward. Ash-like solid residues are also produced, however the researchers say these are inert and safe to be disposed of in landfills or repurposed.
Baroutian says: “This technology can effectively destroy PPE waste and reduce their volumes up to 98%. We are literally busting waste with water.”
The process takes one hour in a small prototype machine in a laboratory in the faculty and like the disinfecting solution, it is scalable, clean and has a low footprint.
The team has also done an economic analysis which proves that a large-scale system could process PPE waste at a cost comparable to the current practice of autoclaving and landfilling.
Moving forward, the team says it wants to optimise the process at larger scale to ensure the designs work with the flow of PPE waste. Baroutian adds that the team is looking for funding and is in discussion with commercial organisations as partnerships with industry will help it to implement the technology in New Zealand and overseas.
Have your say. Tweet and follow us @WTiNcomment