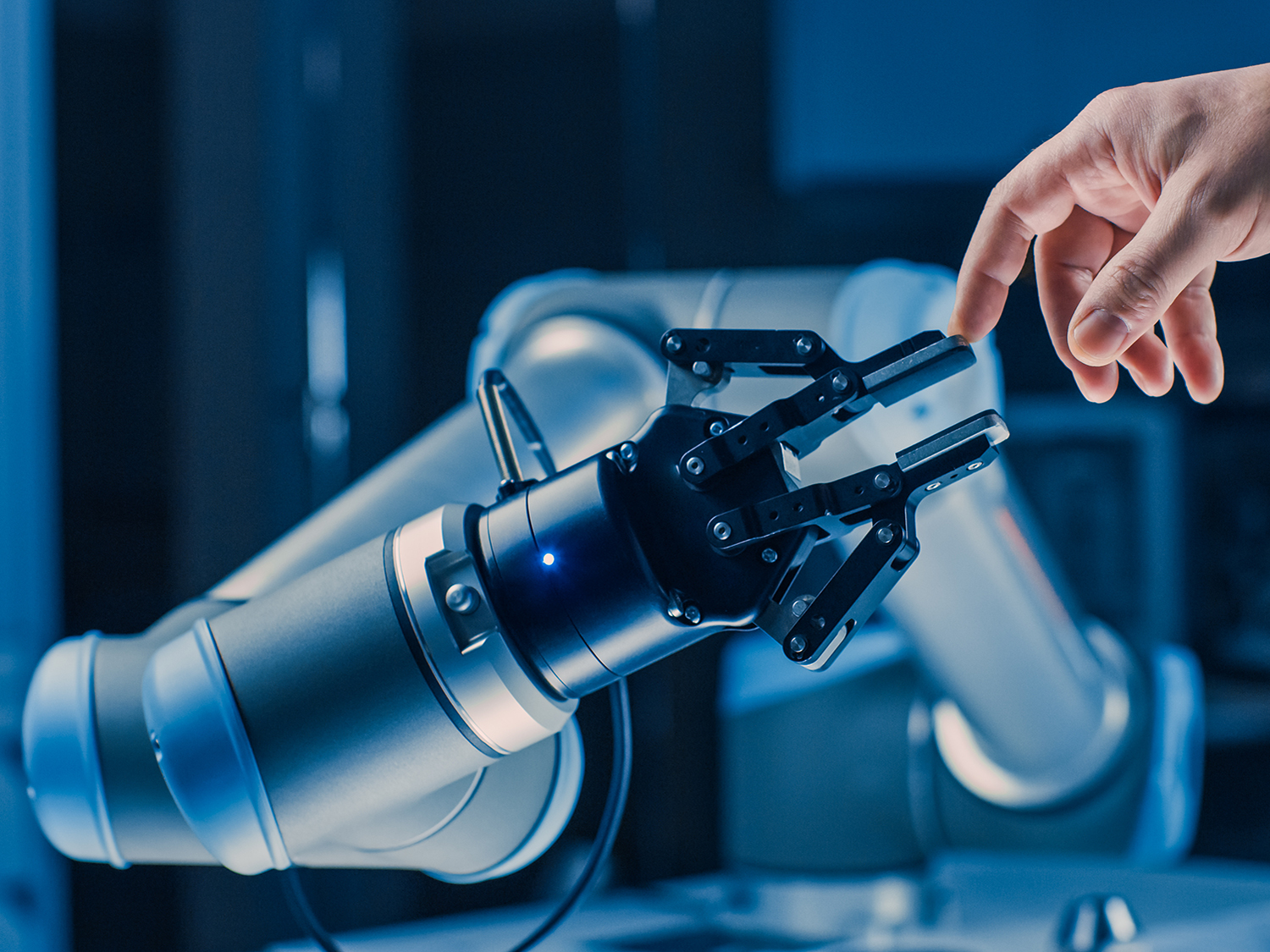
WTiN investigates the state of textile gripping systems for automated manufacturing methods.
Summary
- It is widely accepted that the main barrier to automation adoption in the textile & apparel industry is a lack of proficient automated fabric gripping technology for the handling of fabric after cutting.
- Limitations in this area of fabric handling mean manufacturers are dependent on human labour to sew together garments and have left robotics and other automation somewhat inaccessible.
- However, slowly but surely, automation solutions – industrial robots, gripping and automated vehicles – are enhancing the capabilities of factories, generating smart environments where materials can be transported, moved or handled in automated ways.
- The current automation push in the textile sector reflects progress made in the 1980s and 1990s, which was slowed by the decisive shift to outsourcing to Asia in the late 1990s and early 2000s. It was not until recently that rising labour costs in Asia have revived textile companies’ interest in textile grippers.
- In June 2022, Texprocess welcomed a handful of developments to fabric gripping technologies, listed in this report.
Introduction
The Saxon Textile Research Institute (STFI – Sächsische Textilforschungsinstitut), based in Germany, is developing textile grippers as tools to replace the human hand – driven by industry’s adoption of automation [1].
STFI analysis – shared with WTiN – stressed the need for a wide variety of grippers given the large variety of fabric workpieces in textile & apparel manufacture. Despite widespread use in other industries, including upstream textile manufacture, automation has made less progress in clothing manufacturing due to textile materials being dimensionally unstable, limp and permeable.
In addition, the STFI says such materials take up a large surface area when unrolled, with masses ranging from light to medium weights – all variables that challenge effective automation and robotics. And while typical fields of application for robots in textile production include separating, stacking, positioning and aligning, the automation of processing easily deformable materials still poses enormous challenges for computers and image processing programmes – making tough demands on computing resources.
Michael Fraede, founder and CEO of Germany-based tech firm Robotextile, adds that the manual separation of fabric layers (which is needed to bring the fabric from the cutting table to the automated sewing machine) still accounts for a substantial share of a textile company’s labour costs. Consequently, the automation of this task could add important efficiencies to manufacturing processes. But Alexander Bley, co-founder and chief executive officer (CEO) of Germany-based manufacturing tech developer Sewts, reiterates that simple tasks for humans (such as gripping a towel or a piece of clothing) are inadequately performed by current robots and gripping systems.
Industry developments
At Texprocess, an international trade fair for processing textile and flexible materials that took place in Frankfurt, Germany in June 2022, Robotextile presented textile grippers that pick up the separated fabric layer and set it down again safely and smoothly at the desired position. Attached to a KR Scara robot produced by Germany’s Kuka [2], a manufacturer of industrial robots and systems for factory automation, the united gripper and robot has a working diameter of 1,600mm and a payload of 5 kg. Robotextile has four different textile grippers that fit several types of textiles depending on their thickness, bending stiffness, hairiness, air permeability, weight, static charge and rolling edges.
One gripper separates the layers by directing an air flow, which makes the top layer flutter so that it can be picked up by the gripper [3]. Another system uses an adhesive tape for the separation of layers, while another one uses a rubber roller that rolls between the layers and creates a U-shape loop in the top layer, so that it can be picked up easily. The fourth system uses silicone forceps that – due to its automated sensor-based “finger haptics” – can pick up the top layer very gently. Haptic technology creates an experience of touch by applying forces, motions or vibrations to the user [4]. All four Robotextile grippers operate without artificial intelligence (AI). Before settling for one of Robotextile’s four gripping methods, the company evaluates the textiles for thickness, bending stiffness, hairiness, air permeability, weight, static charge and rolling edges. Optional camera systems detect the position of the fabric stacks and guide the robot to the correct position. Optionally, the robots can be guided and programmed manually for teach-in. This can be done by the production personnel.
Fraede explains: “The manual separation of fabric layers that is needed to bring the fabric from the cutting table to the automated sewing machine makes up for 40% of a textile company’s labour cost. And, the process is difficult to automatise because the loose filament at the edges of the fabric tends to stick together.”
He tells WTiN: “We achieved this by looking at old patents, speaking to the researchers behind them and by using standard off-the-shelf sensors, such as for fabrics’ light penetration and proximity.”
According to Fraede, the current automation push in the textile sector reflects progress made in the 1980s and 1990s, which was slowed by the decisive shift to outsourcing to Asia in the late 1990s and early 2000s. It was not until recently that rising labour costs in Asia have revived textile companies’ interest in textile grippers.
He adds: “Nevertheless, it usually takes real effort and time to implement such modern technologies in existing garment factories, given their outdated infrastructure.
“It is much easier in the technical textile sector,” given their existing higher levels of automation, “which is partly explained by its closeness to the auto supply chain,” he adds.
Robotic systems
Progress has also been made under a European Union (EU)-funded research project – the SoftManBot project for Advanced Robotic Technology for Handling Soft Materials in Manufacturing Sectors. It has drawn financing from the EU’s €80bn (US$77.6bn) research and innovation Horizon 2020 programme, some of whose projects are ongoing [5].
SoftManBot is an industrial-end-user driven project aiming to provide a robotic system for the handling of flexible and deformable materials within labour-intensive production processes. This robotic system utilises a generic robotic perception system (augmented by skilled human operators); a multi-sensor control and planning platform (integrating advanced control algorithms for shape and contact controls; AI-based task generalisation, enabling systems to adapt to unexpected processing events; smart dexterous grippers (using a smart mechanical design with grasping/manipulation skills; and the integration of sensors – mainly tactile – for identifying precisely the contact state between the product and the gripper. Altogether, this system can handle soft components with high-levels of robustness and flexibility.
Among the specific scientific and technical objectives of SoftManBot is the design and development of intelligent, dexterous and low-cost grippers for deformable object handling integrating embedded sensors (notably those offering tactile, force, proximity and vision sensing), says a project note. Another is a smart mechanical structure (embodying grasping/manipulation skills), executing challenging tasks with prominent levels of precision, fault tolerance robustness and flexibility within harsh and changing environments.
Another Germany-based company, the Zimmer Group, a specialist in the field of innovative handling technology, has participated in the SoftManBot project. It aims to help France-based sporting goods retailer Decathlon automatically sew foam pads into cycle shorts (Decathlon creates, designs and manufactures most products sold in its stores). The gripping of the pad is undertaken with a needle gripper and the fabric is draped wrinkle-free with two bendable rubber fingers mounted on a new developed long-stroke gripper. The wrinkles are located by an AI-based sensor whose controller generates commands for the robot and the gripping system. The needle’s extension is driven by a pneumatically driven cylinder. The penetration depth can be adjusted in advance.
The system – which was developed in cooperation with the Italy-based Italian Institute of Technology (IIT - Istituto Italiano di Tecnologia) and Italy-based Stam [6], [7] – works with a robot made by Denmark-based Universal Robots [8]. The system remains a prototype, but the consortium stands ready for further development to produce commercially available systems.
Erik Bauhaus, a research and development engineer at the Zimmer Group, says: “The textile industry is a huge, under-automated market, so we as a company that comes from the realm of classical mechanical engineering found it promising to participate in SoftManBot.”
Speaking to WTiN, he adds: “Industrial implementation will still require looking into error rates, speeds and so on, but once calibration is done on the real application through learning by doing, you will have a fully automated fabric handling system that runs 24/7.”
According to the STFI, needle grippers can be used for unrolled textiles – woven or knitted fabrics. Needle grippers vary by needle number, needle stroke frequency and needle size. Needle grippers are also useful for lifting porous materials other than fabrics such as foams. However, needle grippers can also leave permanent puncture marks in material structures. “Here it depends on whether these defects in the structure are acceptable for the further production process,” STFI wrote.
Suction approaches
US-based Sewbo takes a different approach by temporarily stiffening fabrics, allowing off-the-shelf industrial robots that are equipped with suction cups to easily separate and pick up single fabric layers, as if they were working with sheet metal [9].
Sewbo claims that the fabric panels can be easily moulded and welded before being permanently sewn together. The water-soluble stiffener is removed at the end of the manufacturing process with a simple rinse in hot water without needing detergents, leaving a soft, fully assembled piece of clothing. The stiffener can then be recovered for reuse. The treatment uses polyvinyl alcohol, a non-toxic polymer used elsewhere in the textile production process, as a "sizing" that temporarily strengthens yarn during weaving.
Sewbo has been working closely with an advanced manufacturing team within the Berkeley, California, US-based Siemens Technology, the R&D arm for Siemens in the US. Sewbo is supported also by the US military which is mandated by law to source all its uniforms from US manufacturers.
Jonathan Zornow, Sewbo’s founder and the technology’s inventor, says: “The treatment is applied on the fabric in a lamination process, which is going to be done in parallel with the sewing process.
“Industrial implementation will first come for garments that are washed anyway, such as denim for blue jeans,” he adds, pointing out that the cost of the Sewbo suction cups is as low as a few US dollars each.
A Sewbo note claims that its “technology will allow manufacturers to create higher-quality clothing at lower costs.” It continues that “it will shorten supply chains and lessen the long lead times that hamper the fashion and apparel industries, helping to reduce the complexity of today’s intricate global supply network.”
Another company using the suction-gripper approach is Germany-based Formhand [10]. Its module consists of a frame and a granulate-filled gripping pad, the latter adapting to different objects’ geometry and surface by the freely moving granules, which are controlled by air flows. This creates a sealed system, performing within a vacuum created by an inbuilt vacuum generator. Formhand claims in a note that integrating the system into a client’s manufacturing processes can be quickly done; that energy, storage and maintenance costs are reduced and that the system is modular and scalable. The company also says that the technology cangrip on a large surface with a low-pressure difference in combination with a form-closure enables gentle object handling and that the gripping pads can be used as a mobile gripper, as a stationary mounting element or as a powerful clamping element.
Christian Löchte, Formhand’s CEO, says: “Formhand is basically a tool that combines the flexibility of a sofa cushion with the air flow of a vacuum cleaner. In the textile context, we can use our universal gripping pads for a wide range of processes, such as the picking up of socks, the folding of T-shirts and the packaging of shoes.
He adds: “One of our gripping pads has an A4 paper format size, which is a good size for the handling of T-shirts, for example.”
Löchte continues that when a Formhand gripping pad picks up fabric, it stays wrinkle-free and does not sag, meaning the system could be used to accurately feed fabric into an automated sewing machine to assemble, for instance, a pair of trousers. He says the system has proved its worth in industrial applications, such as in the automotive sector and its flexibility means it could easily be used for textile manufacture.
Intelligent systems
Meanwhile, Germany’s Sewts has been developing innovative machine learning (ML) and computer vision technology to enable highly intelligent gripping operations [11]. The company founders developed this idea during their studies at the Technical University of Munich, focusing on the automated handling of easily deformable materials, such as carbon fibres and textiles.
Their company Sewts, whose name is a combination of “to sew” and “suit”, underlining that the sewing of men’s suits is the most complex challenge in automated sewing of garments, recently completed industrial implementation of its Velum system. It feeds towels and similar laundry made of terrycloth into existing folding machines. This, says the company, closes a significant gap in automation. Indeed, Sewts’ inhouse-developed AI analyses these textiles and translates the findings into robotic commands. Velum is optimised for adaptability and handles all sorts of towels up to sizes of one by two metres – without restrictions regarding colour or texture. Specifically, the robot picks a towel from a stack of such products, locates its seams and positions the towel on a table that allows a second robot to accurately grab those seams to feed the towel into an automated folding machine.
A note from Sewts points out that although industrial laundries wash and dry textiles in highly automated environments to cope with the large quantities of dirty linen, each one of these machines still requires an employee to spread out cleaned laundry to avoid wrinkling.
Human labour involves high costs, with staff serving laundry machines accounting for 30% of personnel costs in laundries, according to Sewts.
Looking ahead, Sewts’ current project is handling garment returns for ecommerce, involving unpacking wide varieties of garments from plastic bags, inspection and packaging.
Alexander Bley, Sewts co-founder and CEO says: “These technologies allow our customers to reduce highly repetitive manual work and better cope with the shortage of qualified personnel. And, our usage of off-the-shelf components makes them economically feasible even if considering that a textile worker in, say, Romania, would cost less than €2k (US$1.9k)/month.
“In five years from now, we will have created a platform that will integrate all our technologies for robot cognition, grip force and so on, so that integrators from different industries can readily use it.”
According to the STFI, another possibility for handling textile materials is freezing grippers. This technology involves the contact surface being wetted with a freezing medium, then frozen with a cooling element. The ice then forms a contact bridge between the surface and the gripper. Loosening takes place by heating the contact surface, which thaws the ice. The STFI referred to the Germany-based Fraunhofer Institute for Production Technology IPT, which has developed a gripper for handling semi-finished products with a low flexural strength that can grip materials such as air-permeable textiles with electrostatically charged films [12]. Attractive forces resulting from the different electrostatic charges of the gripper and the workpiece cause the material to adhere to the gripper.
Also, STFI anticipates the development of bionic grippers, which integrate design influences from the human and animal world, delivering the creation of a humanoid robot hand modelled on the human hand.
Such adaptive grippers could adapt to the contours of the part or material to be gripped and could therefore be used multifunctionally. This would enable safe and non-destructive gripping, even of fragile or irregularly shaped workpieces, says the STFI [13].
Falko Schubert, a scientific officer at STFI, says: “In summary, it can be stated that there is a wide range of grippers with different designs and operating principles on the market.
“Not all grippers are suitable for textiles, but new developments and designs offer opportunities for gripping these fabrics. In any case, it remains exciting to continue to observe this area of technology,” he concludes.
Key takeaways
- Although there remains much to develop in the way of fabric gripping technologies, focus from industry and institutions reveal a variety of future possibilities.
- Some of these technologies, although yet to be fully scaled, offer solutions to fabric gripping issues.
- There exists a range of alternative out-of-the-box solutions too. One such solution for handling textile materials is found in freezing grippers. This technology involves the contact surface being wetted with a freezing medium, then frozen with a cooling element. The ice then forms a contact bridge between the surface and the gripper.
- Alternatively, research is anticipated around the development of bionic grippers, which integrate design influences from the human and animal world, delivering the creation of a humanoid robot hand modelled on the human hand.
- In the future, these technologies – whether out-of-the-box or successfully developed existent ideas – could allow manufacturers to reduce highly repetitive manual work and better cope with the shortage of qualified personnel.
-
References
[1] Editors, “Mobile robots and grippers for textile substrates ,” Textile Network, 2020. https://textile-network.de/de/Technische-Textilien/Technologien/Mobile-Roboter-und-Greifer-fuer-textile-Substrate (accessed Oct. 11, 2022).
[2] KUKA, “KR SCARA Robot,” KUKA AG. https://www.kuka.com/en-de/products/robot-systems/industrial-robots/kr-scara-robot (accessed Oct. 11, 2022).
[3] Robotextile, “Home,” Robotextile. https://robotextile.com/en/ (accessed Oct. 11, 2022).
[4] Robotextile, “Technology ,” Robotextile. https://robotextile.com/en/technology/ (accessed Oct. 11, 2022).
[5] SoftManBot, “SoftManBot – Advanced Robotic Technology for Handling Soft Materials in Manufacturing Sectors,” SoftManBot. https://softmanbot.eu/ (accessed Oct. 11, 2022).
[6] “Istituto Italiano di Tecnologia - IIT,” IIT. https://www.iit.it/ (accessed Oct. 11, 2022).
[7] “Longitudinal and transverse profiling machines and cutting lines,” STAM. https://www.stam.it/it/ (accessed Oct. 11, 2022).
[8] “About Universal Robots,” Universal Robots. https://www.universal-robots.com/about-universal-robots/ (accessed Oct. 11, 2022).
[9] O. Robinson, “Start-up creates system to enable fabric handling,” WTiN , 2021. https://www.wtin.com/article/2021/september/130921/start-up-creates-system-to-enable-fabric-handling/ (accessed Oct. 12, 2022).
[10] “Flexible handling for efficient production and logistics,” Formhand. https://www.formhand.de/ (accessed Oct. 11, 2022).
[11] “Automating complexity,” Sewts. https://www.sewts.com/ (accessed Oct. 11, 2022).
[12] “Fraunhofer Institute for Production Technology ,” Fraunhofer IPT. https://www.ipt.fraunhofer.de/en.html (accessed Oct. 11, 2022).
[13] Sächsisches Textilforschungsinstitut e.V. (STFI), “Sächsisches Textilforschungsinstitut e. V. (STFI),” Sächsisches Textilforschungsinstitut e.V. (STFI). https://www.stfi.de/ (accessed Oct. 11, 2022).