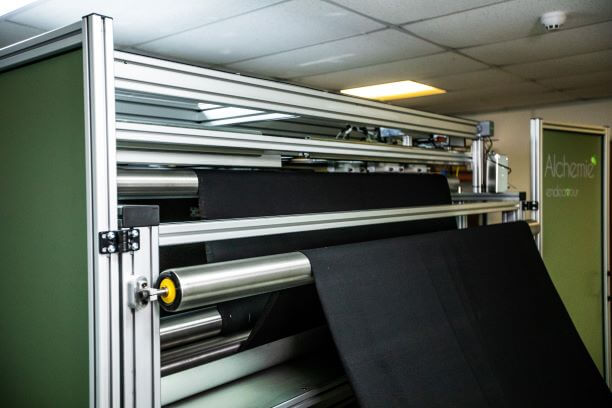
Alan Hudd, director and founder of Alchemie Technology, talks to Madelaine Cornforth about the company’s new waterless, smart dyeing technology.
Water is a critical aspect of many manufacturing processes, particularly in the textile industry, which is dependent on water in most steps of the manufacturing supply chain. The area where water is most highly used in textiles is in dyeing and finishing where traditionally dyes and chemicals are applied to fabrics in baths of water.
This method has been developed over hundreds of years. But, with the population and the demand for fast-fashion increasing, this method is not sustainable in terms of water usage (the amount of water used each year for fabric dyeing is 1.3 trillion gallons, according to World Resources Institute) and is also the cause of a huge proportion of the world’s pollution, through wastewater and textile effluent. According to the United Nations World Water Development Report, up to 80% of the global wastewater is dumped into the environment untreated. But what if we didn’t need to use water in textile dyeing and finishing?
UK-based Alchemie Technology has created a breakthrough waterless smart dyeing system that has the potential to change the dyeing landscape across the globe, reducing the textile industry’s water consumption and pollution.
The waterless, smart technology named Endeavour was unveiled at China Interdye on April 10 in Shanghai, China after over two years of development. Endeavour delivers a step change in sustainability at a radically lower cost, according to the company. Alan Hudd, director and founder of Alchemie Technology, says that the technology addresses all the problems that that previous industrial revolutions created, such as pollution, waste and long lead times.
He explains: “[Endeavour is] a completely waterless smart dyeing process for the on-demand digital dyeing of textiles. It is a unique digital technology: it has all the advantages and propositions of digital and yet it’s able to produce very high-quality dyeing with less than 1% variation across the web of colour consistency. Concurrent methods of dyeing find it very hard to match that level of colour quality. So not only does it have all these digital advantages, but it also creates a high-quality process.”
The technology
The Endeavour technology includes a fully automated colour lab sampling system to perfectly match a customised colour in a very short time making the system a truly ‘end-to-end’ high-performance sustainable dyeing solution with ultimate performance, says the company.
According to Hudd, Endeavour is unique in the sense that it is a digital process but is “unlike other digital technologies that exist.” So, although it shares a lot of similarities and the same benefits as inkjet, it is not the same technology. “Endeavour shares some similarities with inkjet with the type of configuration and setup,” he says. “It’s just that the process of jetting is very different. What we’re able to do is jet fluid or dye deep into the fibres of the fabric. Once we’ve jetted the dye into the fabric we’re creating an atomisation process where the dye finds its way onto the surface of the fibres very quickly and when it’s fixed they go deep into the fibre.”
The smart system has nozzles just like an inkjet system and each one of these nozzles can be addressed individually a different amount of liquid dye can be delivered to each nozzle. “We can optimise the shade colour that the user wants to end up with,” says Hudd. “We can put a small amount of dye per jetting process or a large amount of dye per jetting process depending on what shade a user wants.”
The Alchemie Endeavour waterless smart dyeing process is capable of throughputs of over 2,000 sqm/hr (the average throughput for the bath dyeing process is usually 2,000 sqm in somewhere between 4 and 6 hours) and will reduce waste water and energy by more than 80%, delivering more than a 50% reduction in production costs. For example, Hudd claims that the Endeavour system will operate on the basis of less than 1 kW/hr. “That equates to about 80% less than the traditional bath process of dyeing polyester in China.”
He continues: “We’re all about dramatically reducing manufacturing costs and increasing profitability for manufacturers. We know western brands are keen to push sustainability but a lot of the time, the manufacturer in [mass production countries like] China is really just looking at profitability. Endeavour hopefully does both: creates a step-change in sustainability, but it also enables the dyeing manufacturers to increase profitability. Overall we’re claiming that we can eliminate water emission and reduce carbon footprint by about 80%.” He adds that the digital benefits are on-demand, reducing run lengths and enabling rapid changeover between colours and fabrics.
At the heart of the system is a unique new dyeing process that distributes dye molecules deep into the fabric enabling very high absorption, homogeneous distribution and excellent fixing efficiencies. This results in minimal wash out, even at very high saturation levels of dye.
According to the company, the technology delivers exceptional results with high colour consistency and colour fastness. There are no restrictions on available colours except from restrictions that the traditional dyeing process faces in colour availability. And, with the fully automated colour lab sampling system, customised colours can be matched. Based on Alchemie’s proprietary digital manufacturing technology, the system can deliver any colour shade required and enables on-demand digital colour changeovers in any run length from a few metres to several kilometres, says the company.
Chemicals
The use of chemicals in textile dyeing and finishing can also be costly as well hazardous for both the environment and for consumers and can add more steps to the manufacturing process, increasing lead times and energy usage. However, with Endeavour, a binding chemical is not required to bind the dye to the fabric. Hudd explains binding is not needed in the delivery process of the dye to the fibre. “The fixing process is still very important and it’s the fixing process that takes the dye from the surface of the fibre into the fibre,” he says. “But what we’re all about is delivering the dye molecules to the surface of the fibre. It’s a very efficient process. We are able to optimise the right amount of dye for the particular shade that you want.”
With current dyeing methods dye manufacturers often have to saturate the fabric with a lot of dye and that saturated, dyed fabric then ends up having most of the dye washed out, causing real waste problems. “We’re able to optimise the delivery of the dye to the fibre to exactly the right amount that you want to fix into the fibre and get the right shade,” says Hudd.
He adds that the Endeavour system is not chemical free in the sense that the dye is a chemical but “the other ingredients in the formulation are not hazardous and therefore are not considered to be a problem as far as waste is concerned. The traditional formulation has quite a lot of different chemicals in them to help get the dye to where it should be in a fabric and we don’t have to use any of those chemicals.”
The waterless process can deliver dyed fabric that does not require post-dyeing washing steps to deliver finished product – a remarkable sustainability advantage, according to Alchemie. At the moment, the company is focused on dyeing polyester fabric as “80% of the market is polyester,” says Hudd.
Although the process works on all fabrics, the company is choosing to focus on polyester initially. “It will work just as effectively on cotton but you still need a pretreatment process on cotton to fix the dye to the cotton fibres. In the case of polyester, then the choice to use a pretreatment is really all about the contamination that is in the fabric to begin with,” Hudd says. “The pretreatment for polyester is really a wash with water to clean all the oils and contamination that exists in the fabric. Some manufacturers choose to pretreat polyester by cleaning it and some manufacturers choose not to. Our process is not dependent on either. We can use either and we tend to want to use a pretreatment washing process because you end up with much better quality.”
Any pretreatment process used however would be the same as the traditional polyester pretreatment process. “To get rid of all these oils and contamination in the fabric,” says Hudd. “When fabric is made there is a lot of oil contamination in it.”
When it comes to post-treatment Endeavour requires a steam fixing process. Hudd says: “By the end of this year we’re planning to have an end-to-end process where we dye and we fix inline and put a steamer for steam fixing at the end of our product [Endeavour] so the fabric you get out [of the machine] is dyed, fully fixed and optimised to the right shade.”
Performance
As the process is waterless, the fabric comes out of Endeavour completely dry. “The whole point of this atomisation of the dye within the fabric is that we’re also vaporising any water we’re using in the formulation and therefore the fabric is coming out dyed and then it can be steamed to be fixed. That’s where the big advantage of using less water [lies],” says Hudd. “We’re claiming that we will use 95% less water than the traditional processes. That’s huge because the wastewater in the current process is costing a dye manufacturer a lot of money.”
The hand-feel of the fabric once it is dyed is “much better than padding because again you’re saturating the fabric with dye,” says Hudd. However, he adds that a lot of the hand-feel is a consequence of the fixing process, particularly with polyester. “If you use dry heat for polyester and you overcook it, the hand-feel is awful. If you steam it, you get a much better hand-feel and that’s why we prefer to steam it.”
According to Hudd the colour also has very little wash-out because of the unique atomisation of the dye onto the surface of the fibre. And the “dry-rub colour-fastness and the wash are all seen to be very good indeed,” Hudd continues.
Sustainability
Sustainability is one of the key drivers behind the Endeavour technology, with Government initiatives and pressures from big brands forcing manufacturers to clean up their manufacturing processes. China in particular is under a lot of pressure, with 65% of the world's clothing now made in China.
Hudd says: “The Chinese government is putting a lot of pressure on the dyeing industry. The manufacturers themselves are finding it tough to keep up with other countries in Asia. Fabrics in China are going offshore because of all these pressures.” However, with Endeavour technology, Hudd argues that these pressures are alleviated as Endeavour creates 95% less wastewater, uses 80% less energy, 30% less dye and Hudd estimates the cost of labour will reduce by 50% with Endeavour.
“One of the problems manufacturers in China have is recruiting people to work in their factories,” says Hudd. “The middle class in China is increasing and as a result the Chinese manufacturers are now struggling to get the labour to carry out some of these activities [needed in textile and apparel manufacturing] and we believe that we will offer the dye manufacturer the ability to reduce their labour cost by reducing the number of people involved in their operation.”
He continues: “In a typical medium-sized dye manufacturing facility in China they have about 25 people involved in the process and we can certainly envisage that being reduced to about 10 or so people.”
In the last few years the Chinese government and wastewater treatment plants have raised the costs for handling wastewater dramatically. Hudd says: “It’s gone from US$0.45 (3RMB) per 20 tons of wastewater to now costing them $US1.79 (12RMB) per one ton of wastewater.” As well as this, each of the factories have a daily cap of how much wastewater they can produce. “So, they’re now forced into trying to recycle the wastewater which is very expensive,” says Hudd. “The cost of handling wastewater significantly affects a manufacturers profitability and just by removing the cost associated with wastewater, the dye manufacturer could increase their wastewater profitability by about 40%.”
Current dyeing processes such as the traditional bath or padding process take much longer than Alchemie’s Endeavour technology. For example, the bath process takes about four hours and uses a lot of water: 30 times more water than dye. “In our process, we’re literally taking a couple of minutes to dye the fabric and then you need to fix it,” says Hudd. “That fixing process is a steaming process and that literally takes a few minutes as well. We’re reducing the time significantly from the bath process to an on-demand dyeing process.”
As well as sustainability, profitability for the dye manufacturers is also increased with less people, wastewater, energy and water usage. “It’s about sustainability and increasing profits,” comments Hudd.
Due to pollution issues in China and increased government regulations, along with a changing societal landscape, Alchemie has chosen to commercially launch Endeavour in the country. Hudd says: “The Chinese are so hungry for [this technology].”
The company is also seeing a lot of interest from Western brands as sustainability is a priority for them, with pressures from organisations and the more conscious consumer increasing. “Brands want to be responsible and the textile industry is a massive [global] polluter,” continues Hudd. “The combination of the pollution of rivers and all this water and energy consumption are very big environmental problems that the Western brands are very conscious of.” As a result, Hudd says that Western brands are pushing Chinese dye manufacturers into considering Alchemie’s Endeavour technology.
Dyes
Alchemie Ruby liquid dyes have been optimised for high quality performance and are available for use in Endeavour. Other dye suppliers are welcome to contact Alchemie to become an approved liquid dye supplier to the Endeavour system but the machine itself, says Hudd, is an ‘open system’. “We can use dyes that are suitable for polyester dyeing and we have got an open system,” says Hudd. “The formulation is different and for anybody who is interested in supplying dyes for the system, we are going to put the traditional approval process in place to make sure that we retain the quality. We optimise the formulation and we use, in the end, about 30% less dye than traditional formulations for dyeing polyester.”
As a result, one of the big changes in formulation compared to traditional dyeing processes is the concentration of dye: “We just don’t need the amount of dye to get the shade or the colour intensity that you have to use in the bath dyeing process,” says Hudd. “In the bath dyeing process there is an equilibrium between the dye in the water and the dye in the fabric and so you have to use more dye than you need to push the equilibrium towards dye being maintained in the fabric.” But this is not required with Endeavour.
As well as dyes, Endeavour technology can be applied to any type of chemistry – whether it’s a metallic dispersion, a self-cleaning type chemical or more. Through this system, Endeavour could be used not only as a dyeing system but a coating system. If you are interested in putting a dressing pattern in or patterning different chemistries onto textile fabrics then Endeavour will be able to do that as well at some point in the future. Though it is capable to do so now, it’s just not where their ‘efforts are focused’ at the moment.
Challenges
As the technology makes its way into the market, the company is facing a number of challenges in an industry which has been dyeing and finishing its products in the same way for decades and in some instances, for hundreds of years. This is particularly difficult for a smaller sized company and in this regard, Hudd notes that one of the big challenges they face is “visibility and being taken seriously.” Overcoming this barrier, however, is the reason why Alchemie is taking the technology to China and setting up a demonstration lab to invite people to test the dyeing to prove its capabilities. “The claims are quite important and certainly in China seeing is believing,” says Hudd
“The challenge of course is two-fold,” adds Hudd. “One is that it’s a new technology and we are trying to battle through an infrastructure of how it [dyeing] has always been done – and it is an outdated process. As well as this, trying to get people to understand this new technology is a challenge.”
And then are commercial challenges. Although the technology is very cost-effective compared with previous dyeing processes, the capital outlay for the Endeavour technology is greater than the capital outlay of the bath dyeing process. “We are going to be very cost-effective but the capital outlay will be one of the biggest challenges,” comments Hudd. As the dyeing industry works on tight margins, getting potential customers to understand ROI (return on investment) with the technology could be difficult.
Impact
The impact that Endeavour could potentially have on the dyeing and finishing industry is huge. Hudd says: “It will bring the textile industry from the dark ages into modern day, with modern-day responsibilities around sustainability.” It is also set to increase the performance of the textile fabric as well as the quality of dyes. Hudd compares the technology to digital textile printing: “[Take a look at] all the advantages that digital printing has brought – on-demand, rapid change-overs, no set-up costs, all of those things [had] a big impact.
“I can see the same impact and the same effect happening with textile dyeing, if we can get traction,” he continues.
There is the belief that eventually waterless dyeing technology could soon become popularised. According to Hudd, it is just a question of time and effort.
“I remember going to the first inkjet textile conference in San Diego, California, US in 1997,” says Hudd. “It took a long time for digital printing to get through into the textile industry so we shouldn’t underestimate the barriers in the infrastructure to making progress.
“Given time I think that it will become the new norm.”