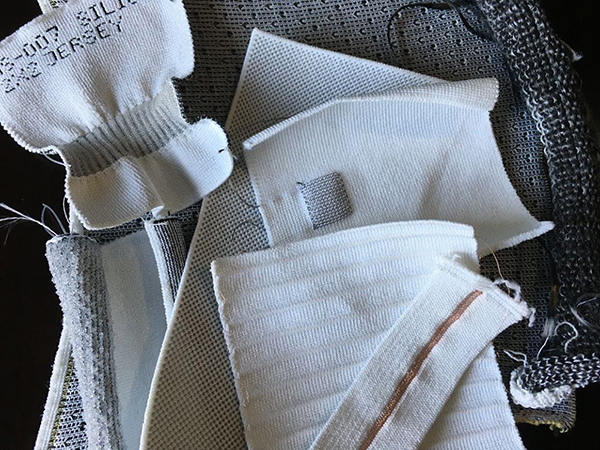
In February 2021, Fabdesigns and Meminger IRO soft-launched an unspooling device that successfully integrates conductive fibres into the knitting process, enabling enhanced scalability of smart garment production. Otis Robinson reports
How can garment manufacturers knit conductive fibres into a fabric, instead of merely placing circuits on top of the textile? This is a commonly asked question in smart textile manufacturing, says Concetta Huffa, president at Fabdesigns and volunteer for IPC, a non-profit, member-driven organisation that specialises in electronics and manufacturing. Over many years, IPC has set industry standards for smart textiles and wearable technologies.
Current smart garment manufacturing capability is complex and disintegrated. Electronic components are created separately to garment manufacture and laminated or stuck to the fabric, which can lead to peeling or positional issues.
Huffa volunteers on the committee for smart textile connectors and notes that a reoccurring query from IPC members asks how industry can knit conductive and functional fibres into a fabric consistently with repeatability. The demand for advanced smart textiles and garments is there, but the knitting technology has struggled to catch up.
“Some want it for sports, for fashion, for medical products, for military products, but mostly they want things that are functional, that is easier to produce and where the [conductive fibre] is actually integrated within the materials themselves,” says Huffa. “The Meminger IRO MTD, an unspooling device, is going to help with this – help an ordinary machine make extraordinary fabrics.”
Unspooling device
The mass manufacturing of smart textiles is an area arguably weakened by its limited scalability. Current smart textiles and wearables utilise sticky components that are placed atop the garment as opposed to weaving functional or conductive fibres directly into the fabric. Though technologies exist that try to perform the latter process, Huffa says it is, too, limited by the number of wires or other materials they can knit into the fabric (“With only one or two wires, I really can’t make a circuit”) and operational inefficiencies related to spooling (“When you’re unspooling wire, it starts winding on itself; the machine stops and starts, and when it starts again, it jerks up and the wire usually breaks or breaks a piece on the machine”).
“It’s very challenging to use wire in a machine if you’re trying to get a circuit into a fabric. [Normally] you have one or two,” Huffa explains. “We wanted to be able to have more than that – we’re actually able to get up to 22 on the machine – which means we can now do lots of different things.”
Fabdesigns, founded in 1988 by wife and husband team Concetta and Bruce Huffa, is a confidential engineering firm that creates and scales proprietary manufacturing prototypes and platforms for garment manufacturers and brands. The pair have a rich experience in garment manufacturing – Bruce’s employment history spans R&D specialist at Smitex, an affiliate of Stoll, and master technician at the latter, while Concetta was once a textile engineer at the same company – which led to the creation of their own firm.
The unspooling device, which was soft launched in February 2021, entered development in around 2011, Huffa says, and over a couple of years was refined. Later, the pair approached Meminger IRO, part of Vandewiele Group and a developer of technology for knitting machines, to collaborate on its global commercial distribution.
“They worked on it for around a year,” Huffa explains. “They’d come [to the US], we’d go to Germany, and we’d throw everything we could at it. We threw fibre optics at it, carbon fibre, different types of Kevlar, braided wire, raw wire, different thicknesses of wire and different gauges just to make sure we could troubleshoot as many problems as possible.”
Unlike traditional flange spools, the Meminger IRO MTD can unspool materials without breakage, added tension or problematic twisting.
“Then you have a management of the rotation of the package, which is completely unique. Nobody’s had this previously,” adds Huffa.
The unspooling device is largely machine agnostic, thus can be fitted to new machinery or retrofitted to most legacy equipment and works alongside existing knitting and design software.
“This is a big deal because a lot of companies have pushed [these technologies] to the back [of their minds],” says Huffa. “You can run this on your older equipment.”
Smart garments
The Meminger IRO MTD enables manufacturers to add circuitry to garments for a range of functionalities: “We can put light and sound and all different types of circuits into a particular panel.
“There’s a lot of opportunities now for people to be able to experiment with smart textiles – from fibre optics, to doing different types of composites and mixing different types of materials.”
Consequently, Fabdesigns believes the new tool will enable ‘a new generation’ of design and engineering of smart garments. According to Huffa, the tool allows knitting machines to construct textiles and garments with purposeful placement of circuits consistently and repeatedly – bringing automation and reliability to the construction of smart garments.
“The machines are acting like robots. You don’t have to worry about if something is in the right spot,” she explains. “And we can make sure that for different sizes the circuits are in different places, or for different sexes, depending on muscle groups.”
The tool has additional functionalities on other machineries like embroidery, circular knitting, webbing, and braiding equipment – “There’s a lot of opportunities now for people to experiment with smart textiles,” says Huffa.
Evidence of its success comes from a variety of industries tapping into smart textiles, including automotive, footwear and fashion. Use cases range from catalytic converters to smart footwear and therapeutic garments.
“And you have a lot of other people who might be able to benefit from these options, such as children with autism. Whether it’s for monitoring or sensing mood, or location, or different biofeedback [capabilities] that might be helpful to their parents, caregivers or teachers, this might be something [positive]. One thing we’ve talked about is being able to knit smart alloys into fabrics – if we run a current through it, it actually feels like a hug.”
According to the president of Fabdesigns, the functional possibilities enabled by smart knitting capabilities are endless.
“We’ve got a whole generation of people that are going to be able to experiment with it in whatever way they want. It’s been holding [companies] back,” says Huffa.
“It’s going to bring the next revolution for a lot of different places, a lot of different companies and a lot of different individuals.”
For more information, visit www.fabdesigns.com.
Have your say. Tweet and follow us @WTiNcomment