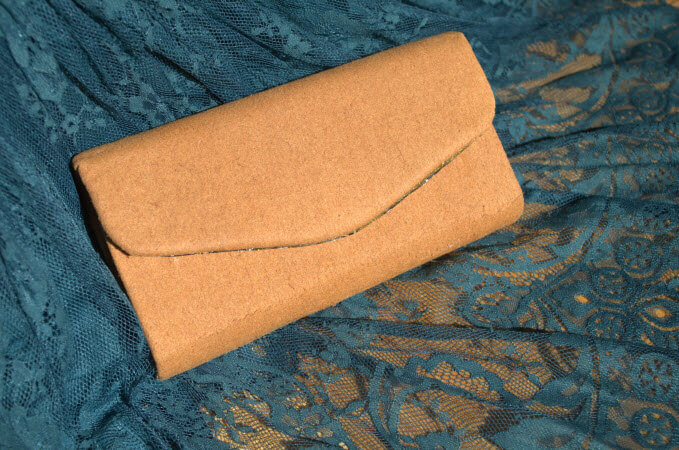
The textile industry is currently under a lot of pressure to become less wasteful and more sustainable. Many manufacturers still use toxic dyes in their practices leading to the pollution of waterways, while fast fashion results in tonnes of garments going to landfill, and even washing clothes at home releases microfibres into the oceans where they have been ingested by marine life.
Yet becoming more sustainable is not simple – new ideas and manufacturing techniques are needed, and this requires a lot of time, money and effort. And even if products are successfully developed, there is the challenge of scalability and affordability.
One company that is currently in the process of creating an eco-friendly material that has the potential to be mass-producible and affordable is Gelatex.
How it all began
While working as a garment technologist, Mari-Ann Meigo Fonseca, co-founder and CEO of Gelatex, became aware of the amount of waste in the fashion industry and decided to start researching innovative materials.
“When I was working in this field, I felt like there was so much waste in the fashion industry, but there were some designers who were using really cool and innovative materials such as using paper and other crazy things,” says Fonseca.
“I then started to look at whether there was anyone in Estonia who was developing new materials and I came across some material scientists at the university, where I was studying for my entrepreneurship and technology management MBA degree.
“The scientists were developing gelatine-based textiles, and Märt-Erik Martens, my co-founder, was one of them.”
At the time, the scientists’ focus was on the medical industry and they were testing the gelatine-based material for growing skin cells for skin replacement, Fonseca explains. She says that the team were already thinking that the technology had more potential such as an alternative to leather, and that’s how Fonseca and Martens started doing more research.
Vegetable tanning is probably the most popular eco-friendly way of making leather, but it is a really slow process and it is not yet mass-producible.
“In the beginning I was thinking, ‘Why? This doesn’t make sense’, because everyone is looking for non-animal alternatives to leather and yet gelatine is made from animal waste,” says Fonseca. “But when we started to learn more about it, we realised that if we improved our existing technology of making gelatine-based textiles, it could be mass-producible and more efficient.”
Sourcing gelatine
Twenty five per cent of the meat industry’s waste is unused as there is a small amount of commercial value to it.
“Gelatine already has many different uses but there is so much more potential to it, and as long as people eat meat, we should maximise the value of the leftovers as much as possible,” says Fonseca.
Right now, Gelatex is supplied as gelatine as a powder from a gelatine factory based in Germany called Gelita. Factories such as this one take the meat waste, such as bones and skins, and make gelatine from it.
“At a later date, when we have improved our production capacity and have thoroughly tested our technology, then we will likely start to make gelatine ourselves,” adds Fonseca.
“At the moment, gelatine is made into a liquid form and then it is dried up in order to store it better and then it is shipped to the buyer. But for us, we don’t need the solid/dry gelatine, it’s fine for us in a liquid state, so one day we would like to start producing gelatine ourselves, so we can cut out some of that production to save even more energy.”
Leather production
The process of making leather at Gelatex is faster than producing normal leather. Although the company is still testing the technology, its production process is so far quicker and more energy and water efficient.
“For our process, water is needed to make gelatine from the waste, but that water is reused and recyclable,” says Fonseca. “Once we get the gelatine and make the textile, it really doesn’t require that much water.”
The leather from Gelatex is also much more affordable: “Our leather costs around €20-25 per sq m, which is maybe half the average price of leather. Of course, there are some leathers that are similarly priced to ours, but on average leather costs €40-50 per sq m.”
And when it comes to the final product, the leather produced from Gelatex is very similar to the real deal.
“Our target is for it to feel and look like leather,” says Fonseca. “Our first few samples did really look like it, they almost looked like skin when you get sunburnt. Then we changed the method a bit and it became tougher. We are still working on the touch, but we can make it very similar to leather.”
Challenges
Developing anything new always throws up challenges, and with Gelatex, challenges include improving the properties of the material and sourcing non-toxic chemicals.
Fonseca says: “We are now happy with the tear resistance and water resistance, but we need to improve the abrasion resistance because when you scrub the material it isn’t quite durable yet.
“The core thing for us is not to add any toxic chemicals either. For example, some companies who make nice eco-friendly materials then may add petroleum-based chemicals on top, which is something we do not want to do.
“So that is why the development can take a while because we are trying to find eco-friendly alternatives that provide the same result.”
Gelatex is currently working on colouring the leather. The company says it only wants to use unharmful and natural dyes and so far, it has been experimenting with beetroot colours to provide a pink shade.
From leather to product
Currently, the company is still very much in the research and development stage, although Fonseca hopes that the leather will be available for production within a year.
She says: “The hope now is that by the end of next year (2019), we will be ready with the product to start to produce other products with this. I hope that maybe we will start to see our products in some shops by 2020.”
Saying that, Gelatex has made a few products from the leather so far. The company has worked with a few designers in Estonia and in Finland where Gelatex has made a few items and received feedback from the brands.
“We have made some small items such as clutch bags, wallets and bow ties,” says Fonseca.
So far, Gelatex has been really well received, despite the lack of marketing that Fonseca mentions. There is the odd group, such as those who are vegan who are not keen on the product, but there is still a lot of interest for eco-friendly materials.
“The interest is really big for smaller fashion designers who are looking for innovative materials, and also for the furniture and automotive sector; these companies are very interested, and it helps that our material comes in rolls – it is much more efficient for them to use,” says Fonseca.
The ultimate goal for Gelatex is to grow the company big, as that is what Fonseca dreamt of – creating an eco-friendly product that can be scaled up.
She says: “Once we have thoroughly tested the technology then we would like to license it so that other companies can start to produce the material, too.”
For more information about Gelatex, visit: https://www.gela-tex.com/
Have your say. Tweet and follow us @WTiNcomment