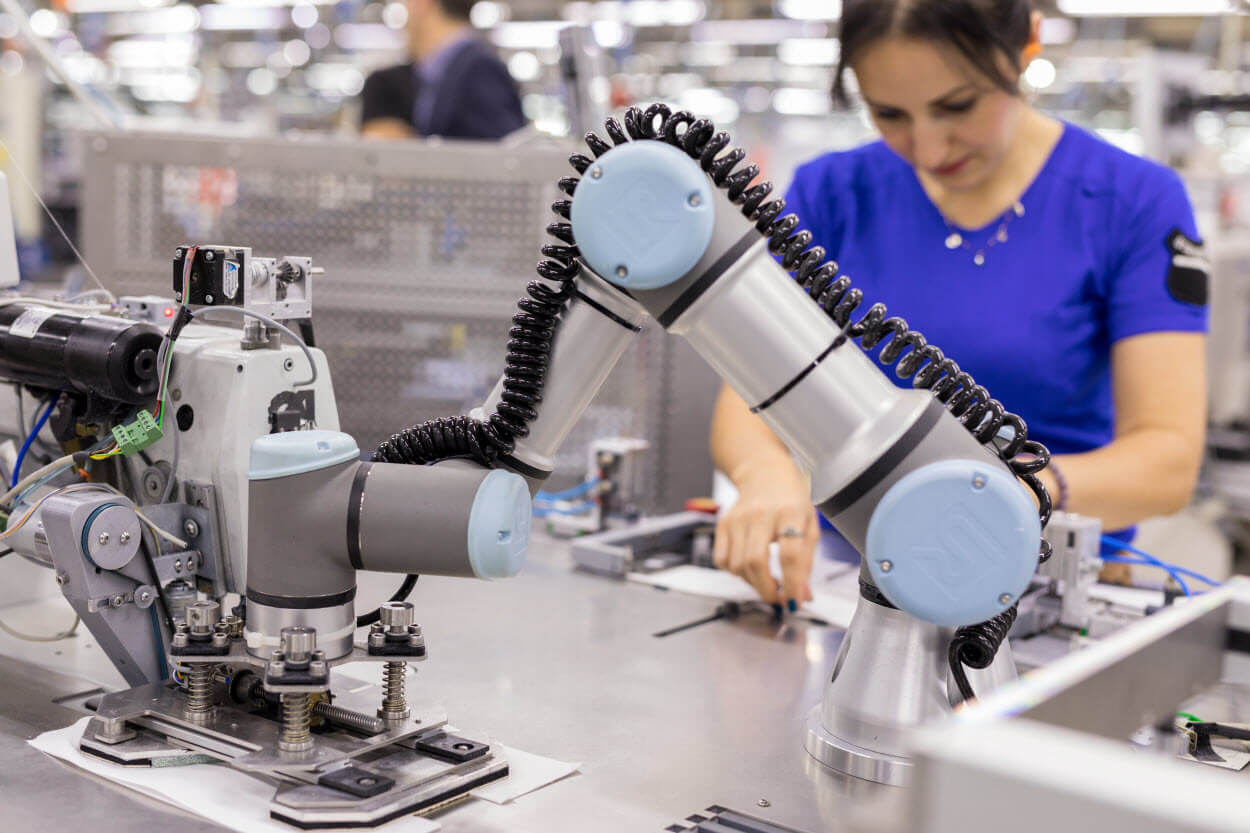
Hugo Boss Textile Industries explores workflow digital monitoring system
By Otis Robinson and Mutlu Chaouch Orozco
Otis Robinson and Mutlu Chaouch Orozco explore the ins and outs of the Hugo Boss Textile Industries facility in Izmir, Turkey, accompanied by senior project manager Yasemin Kan.
Leading apparel designer HUGO BOSS has a firm grip on more than just the fashion market. HUGO BOSS Group, the umbrella company behind the brand, has its roots deeply planted in future apparel production concepts and is determined to innovate the manufacturing space with Industry 4.0 concepts such as automation, digitalisation and more.
In earlier interviews with WTiN, Hugo Boss Textile Industries, Izmir – the company’s ‘biggest producer’ of the HUGO BOSS brand, based in Turkey – revealed its increasing adoption of smart factory concepts such as digital twin technologies, while plans to move away from traditional, analogue manufacturing processes were shown to be at the forefront of managing director Joachim Hensch’s priorities.
Later, Döndü Ünal Haktar, intrapreneur at Hugo Boss Solutions (a company offering Industry 4.0 consultancy based on its own transformational experiences in the Izmir facility), offered insights into how best to integrate this technology into a human workforce.
In the third and final interview with a HUGO BOSS Group company, Yasemin Kan, senior project manager at Hugo Boss Textile Industries, leads a guided walkthrough of the Izmir facility, allowing a first-hand look into the leading designer’s future factory concepts while exploring its plans for the future.
DOJO
First and foremost, Kan makes her way into a room emblazoned with VIRTUAL DOJO along its side in illuminated lettering. Traditionally, dojo might refer to a room in which a range of martial arts can be practiced, but at Hugo Boss Textile Industries it’s the place where people can take charge of their learning and progress within the company.
“Our aim here is to accelerate the learning curve of a new employee (or operator) to adapt in a short time,” Kan says. “We designed the dojo around two years ago. We want to make people’s learning easier and make it more effective. Traditionally, our learning process lasted for 10 weeks on average – but it’s dropped to five weeks with the dojo.”
Upon first entry, the employee will be shown an introduction video that explores their new role and function within the team. By exploring terminology, definitions and individual departments utilised within the smart facility, Kan says a new employee can experience ‘cultural adaption’. By further following the dojo through to a second room, an area akin to a stylish staff room is revealed, and here further operational methods are taught to the employee. “The operator can handle this [area] as they want. They can repeat the training as much as they need,” Kan says, before leading the way into the penultimate room of the dojo.
With ‘defected products’ on display beside faultless ones for comparison, the employee is taught how to recognise when a garment has undergone faulty operation, for example with stitches, for future reference when working on the factory floor. While this training appears rigorous, Kan says that the company understands the difficulty in absorbing so much information and “for this reason, in the production [area], we have tablets for operator usage. They can see information about materials and learn what they need”.
In the final room of the dojo, the employee is shown their new craft: “The operator will learn the technical details of whichever machine they are going to use. They learn this operation step-by-step with the help of our How to Make videos.” But Kan reiterates that staff will not be expected to use only one machine for their entire employment at the company and will be given the opportunity to adapt to changing styles and diverse trends. Training is often followed by tests, and operators can follow their progress online and on tablets on the production floor – Kan titles this as ‘performance monitoring’.
By installing this safe space for employees to revisit and learn at their own pace (and tablets that encourage further learning on the job), Kan says Hugo Boss Textile Industries ensures time is used more effectively in production, while the use of digital technologies is made habitual by the staff.
Next, Kan leads the way to the facility production floor.
Plant One
Product designs arrive from HUGO BOSS’ German headquarters, but technical preparations are made here in Izmir, Kan says, while walking into Plant One, where men’s jackets and trousers are produced. Before a product enters production, its operations, methods, process flow and unit times are studied so that staff can reduce obstacles and ensure the ‘best quality’; there lies a ‘technical preparation centre’ that, through usage of smart tablets, transforms designers’ designs into production conditions.
“The purpose of this department is to transform the parameters defined by the creative team into the simplest and most comprehensible way for the operators,” Kan elaborates. But this is only one way the facility uses digital technologies to ensure smooth sailing where garments are made.
There are five visible lines operating within Plant One, each working on separate garments with a supervisor at the helm of the wheel. Each supervisor acts as the backbone for the performance, efficiency and quality of the work done here, but they are supported by digital management tools installed into touch-screen panels. Data visualised on the screens, which hang nonchalantly and tidily from the ceiling, is derived from operators.
“Each operator has a tablet. We have a data collection system in this factory and other factories, based on smart, touch-screen tablets,” Kan says, about the 1,700 tablets in production. Hanging on the edge of each machine, tablets issue operational instructions to an employee at the start of each day, upon their login. Data such as the time taken for an employee to complete a task is recorded for the supervisor, while the operator can input notes such as machine aggravations or staff meetings that may have impacted the duration of a task – in the Hugo Boss Textile Industries facility, even management can be digitalised. “Thus”, Kan says, “the operator can monitor their own performance and efficiency from the tablet.”
Additional functions, such as method checks, can be completed by operators, while previous and present errors are visualised on-screen to prevent ‘erroneous work’ from passing through. Kan says the facility digitalised the operational process in order to track the quality and efficiency of production protocol and further support the training and growth of operators – a functioning example of the aforementioned digital twin technology Hensch intended to implement, uprooting traditional supervisory methods.
Kan adds that these digital management and performance monitoring functions allow staff to meet goals in their career journeys, such as rising salaries or promotions, but also improve their communication abilities with outward parties: “For example, when an operator needs a certain material, they can now order it online from the tablet. This order falls to the screen of another operator within the warehouse so the operator knows which line and which operation needs which material.”
Kan continues, exploring the benefits of wielding digitalisation in conjunction with a human workforce: “The main purpose of data collection is also [to allow] supervisors to take immediate action [on production obstacles]. They need to see the results of their line [in real time] so they can manage it suddenly.”
To adequately respond to obstacles in the workflow, supervisors are equipped with access to the production and efficiency data of a line, team or individual staff member. Kan elaborates: “The performance of an operator may be high, but if there is too much loss of time, it will reduce productivity, which will affect the profitability of the company. It is the responsibility of the supervisor or management to manage this lost time well.”
With new and efficient processes on display, Kan leads the way to the pre-ironing checkpoint, where jackets and trousers are sent in the dozens.
Innovative technology, Plant Two and smart robotics
Before continuing the tour, Kan explores the bigger picture. The introduction of such technologies into the management style within the facility is derived from a specific goal: to increase the transparency of processes. Kan says that, overall, their goal is to make people, technologies and processes talk with one another to reduce the complexities of traditionally complicated manufacturing processes. Often, these traditional practices do not offer people the best working experiences.
“The skills of people are key to reaching high standards in our industry and therefore to sustain customer satisfaction. So, if you manage to prepare your human resources to these technologies and use technology in a form that supports people and brings out their skills, this is the best you can do.”
Additional digitalisation appears through predictive maintenance technologies, which are used to analyse the longevity of machines. For example, temperature, current and vibration data is taken from industrial sewing machines to monitor maintenance or replacement machinery needs.
Kan continues while entering Plant Two, the final stop at the Izmir facility, where women’s clothing and men’s shirts are produced. Here, many product types are made – with an annual production of two million men’s shirts and 550,000 miscellaneous items of women’s clothing – which means the order size can be quite small and similar production processes to Plant One are used in order to be able to ‘switch from one product to another’.
To meet the facility’s ‘competence needs’, extra functions such as automation are used to enable the sewing of shirt cuffs and buttonholes. These robots are intelligent, too, Kan says, because they must identify pieces of fabric: made of two varying lengths of material, the robot must correctly layer the longer cuff over the shorter cuff ‘so that the bottom side isn’t seen’.
“The machine is manufactured by Hugo Boss Textile Industries,” Kan adds. Automation robots and machines such as this have been utilised in the automotive industry for years, Kan declares, but until recently, there had been no counterpart for the apparel industry. So, in 2016, the company established a technology laboratory – titled TechnoLab, made from a team of disruptive digital technologies researchers, image processing technology experts, textile engineers, industrial engineers and mechanics for production – who now dedicate themselves to new machineries for testing in the production space.
Coupled with the facility’s ongoing digitalisation (Hensch affirms that you ‘cannot digitise everything in one night’ in WTiN’s first Hugo Boss Textile Industries interview), the company is setting an intriguing example for the fashion and apparel manufacturing space whereby Industry 4.0 technology is not independent, but tied hand-in-hand with staff, their career trajectories and company communications.
The facility’s success in integrating such technologies with its human workforce is often used as an example for Hugo Boss Solutions, too, who frequently use the Izmir site to discuss Industry 4.0 concepts with its clients.
“There is a demand from Hugo Boss Solutions’ customers to see our facility. Although people have an idea about digital transformation, they really need to understand what it truly means,” Kan concludes. “When they come here, they understand everything so much better.”
Have your say. Tweet and follow us @WTiNcomment