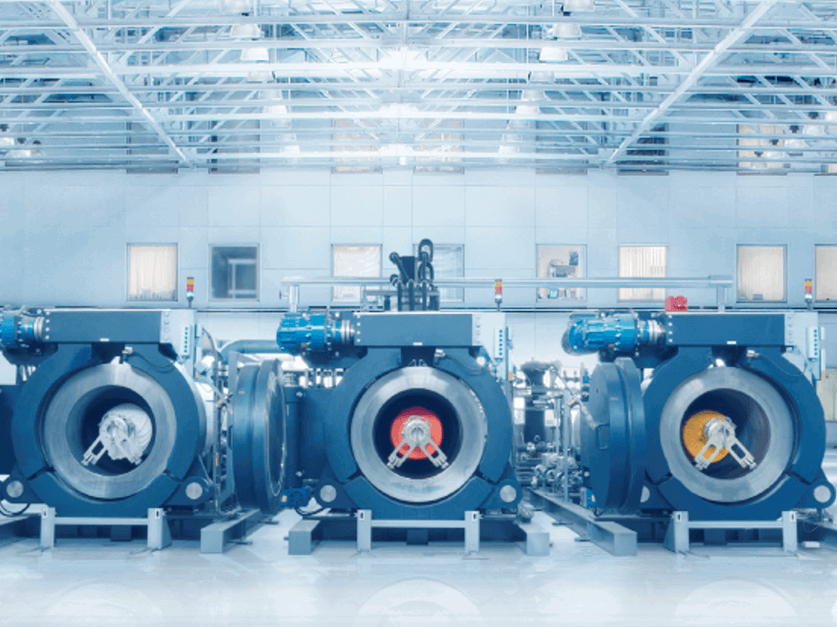
As an industry, textiles has one of the largest water footprints in the world. The dyeing process poses one of the biggest problems within the textile sector, not just in terms of using a huge amount of wastewater, but in terms of polluting with wastewater and textile effluent as well.
It is estimated that traditional dyeing processes use 5.8 trillion litres water annually, equal to around 3.7 billion Olympic swimming pools, according to the University of Leeds. What’s more, 10-20% of the dye used in the dyeing process remains after dyeing, as well as other chemicals leading to the potential for wastewater pollution. The World Bank states that one fifth of the world's industrial water pollution comes from the textile dyeing industry.
As a result, the industry needs to adopt more sustainable technologies for processes like dyeing, particularly for manmade fibres such as polyester which is the most used fibre-type in the textile industry. New innovative processes must reduce or eliminate the use of water and chemicals, reduce energy usage, while also sustaining the look and hand-feel of traditional water-dyed fabrics.
One company offering a solution that meets these needs is Netherlands-based Dyecoo. The company’s solution is completely water-free and therefore wastewater-free and uses no chemicals, replacing water and chemical resources with supercritical CO2: a fluid state of carbon dioxide where it is held at or above its critical temperature and critical pressure.
Dyecoo is, at the moment, the only company in the world that offers a “true industrial, commercial CO2 solution, meaning that we are now the only one so far in the world that has a complete, 100% water-free and chemical free dyeing solution for the textile industry,” says Kasper Nossent, managing director for Dyecoo Asia.
The technology has been developed over the last 20 years and has evolved from a lab environment to a commercial, industrial solution.
“We always try to be a front runner in the industry, looking at doing things differently and add something to a big need that this industry has [and this is] that it has to change in terms of environmental impact,” he continues. “We have to reduce water usage, we have to reduce chemical usage and it’s preferable if we don’t use them at all to get complete, water-free, maybe even chemical-free solutions to make fabrics. Of course, it also fits into the bigger picture of the circular economy where everything needs to find a way back into the value chain.”
By the end of 2018, Dyecoo had a total of 12 machines in operation at six different customers in Vietnam, Thailand and Taiwan. For 2019, the company expects to expand further into India and Europe while growing its existing Asian markets.
The company’s growth plans are going well so far, with Indian textile manufacturer Arvind Ltd in talks to introduce CO2-dyeing with the Dutch technology provider.
How it works
According to Nossent, the technology itself is actually quite simple. “Instead of using water, we use supercritical CO2,” he says. “The advantage of using supercritical CO2 is that we can actually dissolve the dyes into the CO2. We only use CO2 and pure powdered dyes. We don’t need to add any chemicals to keep dyes in dispersion. We don’t need to add any anti-foaming agents. We don’t need to add any levelling agents, any salt or any pH modifiers. None of that is needed: pure CO2 and pure dyes are all that we need.” Other than electricity and steam, supercritical CO2 is the only ingredient Dyecoo requires.
“We take CO2 and make it supercritical by increasing the pressure to 250 bar, while also increasing the temperature to 120°C (standard dyeing temperature for polyester dyeing),” says Nossent. “During the dye-cycle, we pump the CO2 around so that we pick up the dye. We dissolve the dyes and then transport that to the fabric which is not much different than what happens in a water system except for the fact that we don’t have a water-like carrier. After dyeing we recycle the CO2, and then we store it again and use it for the next dye-batch.”
The company uses liquified supercritical CO2 which must be stored at between 50-60 bar. It is a standard process gas used in industry as a cooling agent, cleaning agent or solvent. “It’s also a sustainable gas because you can actually reclaim it from powerplants, or beer breweries, both of which produce a lot of CO2,” says Nossent. “You can capture those gases, liquify them, purify them and then they are sold as industrial gases.”
Through this method, the technology is truly sustainable as it doesn’t use any water or chemicals, nor does it produce any wastewater. It does, however, require energy to run the machine. “We use steam for heating and we use electricity for cooling and driving the pumps,” says Nossent. “[…] If you look at the bigger picture of energy consumption for CO2 dyeing then we use significantly less energy. The simple reason [for this] is that in the industry people are now working towards zero-liquid discharge plants where you recycle and keep recycling water. You even use very energy intensive solutions where you evaporate water and condense it again and get rid of any contaminates. That is extremely energy consuming. So, if you look at the whole picture, we make a significant impact because that part is not needed.”
The technology also does not require additional pre-treatment or post-treatment steps. “We replace the dye process. The only thing that we add to the equation [in terms of pre-treatment] is that we have a beam-dye process, which is not standard in a lot of dyehouses. So, you’re required to pre-set the fabric and then wind them to a dye-beam that we use in our machines.”
When it comes to post-treatment, fabric leaves the Dyecoo machine completely dry so there is no need for an added drying process. Also, Nossent says: “You don’t need to do any post-processing to develop the colour. Everything is done with CO2. And if you don’t need to do any wet-post finishing you can immediately transport the fabric to the next processing step, which can be garment making.”
At the moment, the dyeing technology only works on 100% polyester fibres where, according to Nossent, the technology can achieve the same, if not better results, than traditional water dyeing at a cost-competitive level. Polyester-cotton blends can also be dyed but the cotton part of the substrate remains unstained.
The company is working on adding new material types to its pallet of materials that it can dye, to be able to reach a wider segment of the market. “One of the things that we are currently working on is nylon and nylon spandex,” says Nossent.
However, the latest fourth generation machines, the Dye0x4 – launched in 2017 – can dye-knit fabric, woven fabric and yarn, this is a unique all in one machine concept that doesn’t exist in traditional water dyeing.
Dyecoo works together with dye-stuff suppliers to develop new dyestuff ranges for these new fibre types and applications, such as nylon and nylon spandex. “Those are applications we work on together with dyestuff suppliers who are actually developing new dye-types,” he says.
Sustaining traditional quality
This partnership with dye-stuff suppliers such as Colourtex, Dystar and Huntsman, is what allows Dyecoo’s technology to achieve the same, if not better results, than that of traditional dyeing processes. “The dyes that we use are not much different to the dyes that already exist in, for example, polyester dyeing. Our dyestuff partners have developed specific dyes and dye ranges to be very soluble in CO2 because they need to be soluble,” says Nossent. “So basically the colour strength and the dye performance is the same as, or in some cases even better, than traditional dyeing.”
However, Nossent has seen that CO2 dyeing does provide a significant advantage for very specialised niche applications such as specialised fibres. “We do see that, for example with high visibility neon colours, C02 dyeing provides much more brightness and vibrancy to the colours than water dyeing.”
The technology at the moment is very much supported and pushed by big retailers and brands. They have high standards when it comes to colour-fastness and the dyestuff partners that Dyecoo has have developed dye ranges that can meet the strict and high performance KPIs for dyes that are used by international brands.
“The other advantage that we have is that we don’t need to do any reduction-clearing step after dyeing,” says Nossent. “We dye the polyester, the nylon or whatever the material is that we are dyeing and then when the fabric leaves the Dyecoo machine the colour strength is there. The colour-fastness is also there and we don’t need any post reduction clearance steps. That is different than traditional water dyeing.
“Our philosophy is that sustainable technology should not only be sustainable but should be a substitute for the existing technology and also be competitive,” he continues.
Pressure for sustainability
While the sustainability trend began and is strongest in Europe, the majority of textile mills are located in Asia. Consequently, this is where the bigger pressure is coming from to be sustainable as it is where the need is. But it is mainly brands, located in the consumer market, that are pressurising their mills, mostly in Asia, to become more sustainable.
Nossent says: “The brands are pushing change because they are pressurised by society to change, and all sorts of environmental groups are pushing them to be sustainable.” As a result, the brands then target their supply chain, ordering them to become more sustainable. “If a brand’s supply chain becomes sustainable the brand can claim that they are sustainable as well,” he adds.
Many of Dyecoo’s customers are setting up new factories in Vietnam. The Vietnamese government is very much aware of the fact that textile dyeing houses are unsustainable, and as a result they have implemented strict rules for water usage, water intake but also wastewater discharge. For example, some local governments in Vietnam have refused large projects capitalised at nearly US$100m, and sometimes as large as US$200m because of pollution concerns. Locals in the area have applauded this, stating that they will not exchange the environment for textile projects, according to Textile Excellence in 2018.
This therefore drives the market to look for more sustainable solutions that use less water and less chemicals. “If they [dyehouses] can eliminate the use of water, it means that facilities can become smaller because they don’t need to allocate so much land to wastewater treatment,” says Nossent.
Despite pressing sustainability and pollution issues, Nossent thinks traditional water-dyeing will always exist in the textile industry, alongside waterless dyeing. He says: “Water dyeing has been developed during previous centuries for natural fibres and the last decades for synthetic fibres. So there is a huge investment already made into making these technologies and these dyes perform better and better. Water dyeing is still making a lot of improvements.
“CO2 dyeing will not replace it [water dyeing] completely, as CO2 dyeing does not work on all sorts of fibre types at this moment.” Currently, CO2 dyeing is not possible for natural fibres such as cotton, for example.
Nossent adds: “Maybe in the next 10 years somebody will develop a solution that will work commercially and industrially for cotton dyeing, but they will co-exist. CO2 dyeing will coexist with water dyeing from a cost perspective […] and we will never be able to compete with these markets. Digital printing and other types of dyeing all have specific needs in the market.”
Have your say. Join the conversation and follow us on LinkedIn