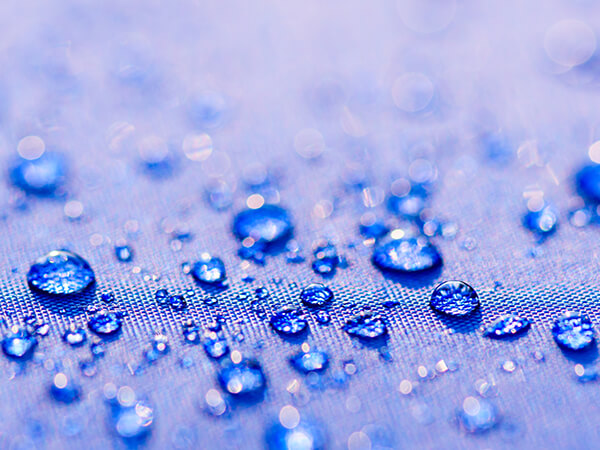
Innovative and ecological methods to manufacture waterproof and breathable membranes
By Laura Solomon
For outdoor enthusiasts, having the right clothing is essential to maintain thermal comfort outdoors, especially in a wet, windy and cold environment. Water resistance is a fundamental function of any outdoor or sportswear garment to ensure the body stays dry.
For a person to feel comfortable in outdoor environments, it is vital that the energy produced and exchanged with the environment is evenly balanced. The human body must maintain its core body temperature of 37°C, to ensure the body feels comfortable and maintains well-being. The body maintains a comfortable temperature during different levels of exertion and environmental conditions, through changes in blood flow and evaporation of perspiration from the skin’s surface as it naturally tries to cool itself down [1]. However, as the body has a limited ability to cope with the outdoor climate, functional materials are selected and engineered for use in outdoor apparel to provide comfort and protection from otherwise uncomfortable environments.
Clothing designed to keep a wearer dry is typically made from either permeable (breathable) or impermeable (non-breathable) textile materials. Impermeable water-resistant materials are notorious for being excellent at blocking water molecules from entering through the membrane. However, it is this same mechanism that often makes these materials uncomfortable to the wearer. This is because excellent resistance to water molecules from the outside environment means that water vapour molecules produced from the body’s perspiration cannot escape from inside the microclimate between the skin and the clothing. Therefore, because perspiration can’t escape, wearing impermeable waterproof textiles commonly causes the wearer to become stuffy and wet with sweat, and subsequently can cause the wearer to experience cold chills.
Permeable textiles, also referred to as waterproof-breathable membranes, prevent liquid water permeating the material. However, they allow water vapour and sometimes air to pass through, maximising comfort and dryness during outdoor activities [2].
Breathability in outdoor garments is extremely important to prevent the wearer overheating, as well as for keeping both the wearer comfortable and the textile fresh by avoiding the build-up of lingering odour. Therefore, a breathable protective garment will aid to enhance sports performance by enabling the athlete to pursue outdoor physical activity of any intensity, while remaining comfortable and protected [2].
Moreover, achieving water resistance in textiles has often resulted in the use of perfluorinated chemicals (PFCs) due to their superior water, oil and soil repellent abilities. PFASs – polyfluoroalkyl substances – are also used as this group of chemicals is closely related to PFCs, with both containing fluorine and carbon atoms. However, despite their great repellent properties, both PFCs and PFASs are part of the DWR discussion that refers to concerning compounds, and they have been the subjects of severe criticism in recent years. Specifically, longer chain PFC materials, depending on their functional groups, can be very hazardous due to their harmful by-products; although it is generally understood that not all PFCs/PFASs are hazardous [3].
PFCs and PFASs can be both environmentally and physiologically hazardous. They are highly persistent molecules in nature, meaning that some of them will degrade extremely slowly or not at all, and many are also bioaccumulating. However, ironically, those who treasure the environment often wear garments that are damaging it. The majority of breathable outdoor outerwear is created with PFASs because they are extremely good at providing water and oil repellence. And although there are still no obvious alternatives to PFAS membranes for deterring oil, developments are being made for fending off water.
In this innovation profile, WTiN reports on a textile material discovered by researchers from Aalto University School of Chemical Engineering, Finland, who have developed a non-toxic, water-resistant and breathable coating solution with wax obtained from Brazilian palm tree leaves [4].
Additionally, WTiN compares the research outcome from Aalto University with a commercially available PFC and PFAS-free, water-resistant and breathable membrane technology from the company Dimpora. Dr Mario Stucki, CEO and co-founder of Dimpora, talks to Laura Solomon about the technology used within the company’s environmentally-friendly membranes for outdoor clothing.
Purpose
The development of a scalable method to fabricate a water-repellent wax particle coating suitable for cellulose fibres, which is ecologically kind and enables the breathability and natural feel of the uncoated textile to be maintained.
Approach
The researchers first prepared a wax dispersion by adding carnauba wax to water at a high temperature. After melting, the mixture was sonicated and then cooled. The wax dispersion was then filtered through a filter funnel with a nominal maximal pore size of 100–160 μm.
During the processing, the wax is thawed and decomposed in water into wax particles that are anionic (negatively charged) just like cellulose. For the wax particles to adhere well to the cellulose surface, something cationic (positively charged) is needed as a buffer, since the oppositely charged particles attract one another. In previous studies, a natural protein called polylysine was used for this.
Therefore, the prepared carnauba wax dispersion was coated onto the textile material using the layer-by-layer coating method where alternate layers of a polycation (cationic starch) used as the anchoring agent, and a layer of anionic wax-particle dispersion, were coated onto the textile. This was achieved by soaking the textile substrate in water and then 10 g/l of the prepared carnauba wax dispersion was applied to the substrate in layers using the dipping (suitable for small-scale coating), spraying or brushing (for garments, eg jackets and other clothes) methods.
Between application and absorption of each wax layer, the wax-coated textile substrate was thoroughly rinsed with water to remove non-adsorbed wax; only then was the next layer of wax coating applied and adsorbed. In total, two layers of wax were coated onto the textile; the samples were then dried and cured in an oven.
Results
After fabrication of the waterproof wax-coated textile, the curing temperature was optimised, and the researchers explored the effect that different types of textile substrates had on the effectiveness of the waterproof coating. Moreover, the breathability, waterproofness and durability of the wax waterproof coating were investigated.
The researchers found that the curing temperature can affect the water repellency and the durability of the wax-coated waterproof textile, due to some molecules in the wax melting at a lower temperature than others. Increasing the surface coverage and molecular rearrangement within the wax coating was found to enhance the hydrophobicity. A curing temperature of 70°C was found to give the highest water contact angle and good long-term water repellency.
When testing the coating on different textile materials including viscose, Tencel, cotton, hemp and cotton knitwear, the researchers found that the surface roughness of textiles has a direct impact on how well it repels water. The researchers found that rougher surfaces had higher water-repellent properties. This can be explained because, on a rough surface, water droplets contact the textile surface in a smaller area.
The researchers compared the developed wax-coated textiles with two other commercially available waterproofing methods. The fabricated wax-coated material was found to perform better both in terms of water contact angle and breathability.
Although in previous studies polylysine was used as the anchoring agent, it is very expensive, so in this study the researchers substituted polysine with a much cheaper, cationic starch that’s already commercially available. Although the researchers found that cationic starch is not quite as effective as polylysine, two layers of the starch mixed together with two wax particle layers were found to be sufficient to make the textile waterproof.
When comparing the breathability of textiles treated with the carnauba wax dispersion to textiles that had been treated with commercial products, results found that the carnauba wax dispersion had improved waterproof and breathable properties.
Additionally, washing tests found that the textile coated with carnauba wax dispersion did not withstand washing using detergents. For this reason, the researchers suggested that this type of coating is best suited for outdoor jackets that do not require washing often.
Moreover, the researchers found that the highest water resistance was achieved when the drying temperature is lower than the melting temperature of the wax.
THE ECO PURE MEMBRANE: A SOON-TO-BE COMMERCIALLY AVAILABLE ENVIRONMENTALLY FRIENDLY WATERPROOF AND BREATHABLE MEMBRANE TECHNOLOGY
Alternatively, WTiN reports on a PFAS, PFC and dimethylformamide (DMF)-free waterproof and breathable membrane technology – close to becoming commercially available on the market – from the company Dimpora, who is based in Zurich, Switzerland. Dimpora has developed an innovative method to form a network of tortuous and hydrophobic micropores within a polyurethane (PU) membrane that is coated onto a textile substrate, transforming the textile substrate into a breathable and waterproof textile material. Dr Mario Stucki, CEO and co-founder of Dimpora, explains to WTiN how this unique pore forming strategy works to provide highly waterproof and breathable microporous membranes, without using any PFAS, PFC and DMF materials in the process.
Dimpora has invented a technology called the ‘template removal method’, with the goal to develop an alternative to the fluorinated membranes that are commercially available on the market at the moment, while still allowing brands to have a high-performance solution.
“If you go out of the fluorinated membranes space, you will have the issue that there is a solid polymer layer that transports water molecules based on solid state diffusion, where it is sucked up and released at the other side. However, this method is very slow so not very breathable. Then there is very breathable, highly porous structures; these are more like wind stoppers and these types of materials do not provide waterproofing,” says Stucki.
The Dimpora technology allows brands to have something that is very porous and therefore breathable, with the necessary waterproofing, without using any nasty chemicals.
To make the polymer membrane porous, Dimpora uses calcium carbonate as a mineral-based template. When the calcium carbonate is blended with the polymer dispersion it acts as a space holder in the membrane, creating pores in the polymer membrane once the template is removed after drying using an acidic washing step. The membranes are then washed again with water to remove the acidity and the newly porous material is then dried once more.
However, the key to Dimpora’s technology is that the calcium carbonate template is functionalised with a hydrophobic substance. Once the template is washed out of the membrane, the hydrophobic additive transfers a hydrophobic coating to the inside of the pores within the polymer membrane. This additional step means the membrane is much more waterproof than it otherwise would be without a hydrophobic coating within the pores.
The porous membrane can then be laminated onto a fabric, laminated in between two fabrics, or laminated directly to a 3D shape such as a foot, hand or torso.
Dimpora is currently working on two types of microporous membranes, named ‘eco pur’ and ‘sane membrane’. “The eco pur membrane is a microporous polyurethane (PU) so it is not as sustainable as the sane membrane which is biodegradable because polylactic acid (PLA) is used in place of the PU. The eco pur is almost commercially available and is being scaled in production. The sane membrane still needs a bit of work before becoming commercially available, to see if PLA is the right material to use for a biodegradable membrane or if there are other polymers that might be better suited,” says Stucki.
At the moment, Dimpora is looking further into PLA in terms of sustainability, price, and how applicable PLA is for this type of application. It is important to investigate if PLA can be laminated and if it has the correct stretch behaviour, as well as if it can be manufactured thin enough before the sane membrane is at the scaling up stage. Additionally, PLA is based on corn starch which competes with food sources, so there is still some questions to be answered regarding PLA, according to Stucki. However, there is no difference in the manufacturing process and microstructure of the two membranes; the only difference is the material that Dimpora uses.
The membrane material chosen for waterproof materials is extremely important. This is because a hydrophilic polymer should not be used, as using hydrophilic polymers would cause the water to get sucked through the pores. It is also important not to use materials that are very rigid, as in this case, the handfeel of the material would be poor and the membrane could break easily when flexed and bent during use in apparel applications.
The Dimpora membranes are typically made with around 55-65% of pores within the membrane that has a thickness of 50 μm and a weight of 25 g/m2. This percentage provides both high breathability (0.5-0.6 cm3/cm2/s) as well as very high waterproofing values (a water column value of 22 m). However, the process allows Dimpora to reduce the water column value to 5 m if required and therefore increase breathability significantly as well as reduce the weight, making the membrane more suitable for lightweight jackets. However, these properties are highly dependent on the membrane thickness.
Moreover, the percentage of pores in the Dimpora membrane can be increased or decreased very easily, in order to adjust waterproofing and breathability. “To adjust the pore percentage, it is simple,” says Stucki. “By simply using more template in the mixture, the membrane will have an increased number of pores, which makes a more breathable membrane, but it will be less waterproof. Or it is possible to reduce the amount of template for fabrication of a membrane that is less porous – this will increase the waterproofness but reduce the breathability.”
The size of the pores in the Dimpora membranes directly depends on the template that is used, as the template material can be adapted. There is commonly a distribution in pore sizes but the pores in the Dimpora membranes are generally below a micrometre in size.
Stucki explains that the pore size, agglomeration of the template and the starting size of the template are all parameters that must be controlled during the process, for Dimpora to achieve the optimum water resistance and breathability in its membrane technology.
The Dimpora membrane is PFAS, PFC as well as (dimethylformamide (DMF)-free. DMF is usually used during the manufacture of microporous membranes. DMF is commonly used to form the pores and it is mostly extracted from the membrane during the manufacturing process. However, it is not possible to totally remove DMF from the membranes and therefore, it is held within the membrane and in this case can enter the skin of the wearer. It is for this reason that DMF has started to be banned in some countries. As the Dimpora technology is DMF-free, this means these membranes can be used as a suitable replacement for companies who don’t want to use fabrics made from DMF in their garments.
The application for Dimpora membranes has been focused on apparel, due to the pricing structure of the materials as well as the market demand for truly breathable and waterproof, environmentally friendly garments. However, Stucki advises that Dimpora is also beginning to look at shoes as an end-product application. Additionally, if there is a tent producer that is interested in high breathability, this could also be an option. The Dimpora technology can be painted, sprayed, dip-coated or printed onto the textiles. This means that the technology can be applied to a ready-made garment or specifically where you need it, enabling a garment to be designed the way it serves a wearer best.
The Dimpora membranes are in the scaling up stage of product development and so are very nearly commercially available. For more information regarding this technology, see https://dimpora.com/.
Impact
The present membrane market is dominated by fluorinated chemistry. This is due to the trade-off between comfort and waterproof performance, and available alternatives on the market at the moment cannot provide the high waterproof performance with simultaneous breathability that is desired.
Therefore, due to rising concerns about the environmental impact of manufacturing waterproof textiles using fluorinated materials, there is high demand from both brands and consumers for new sustainable material alternatives that are fluorine-free with high waterproofing capabilities. The Dimpora technology and the wax particle coating technology from Aalto University, both have the potential to have a positive impact on the environment while also ensuring brands are sustainable, driving consumer sales.
Both these methods can become an option as a non-toxic and, in some cases, degradable finishing to achieve water repellency of materials.
-
[1] F. Group, “Waterproof 6 Breathable Fabrics,” Apparel, pp. 123–145, 2008.
[2] Y. Liang et al., “Super-hydrophobic self-cleaning bead-like SiO2@PTFE nanofiber membranes for waterproof-breathable applications,” Appl. Surf. Sci., vol. 442, pp. 54–64, 2018.
[3] “Overcoming water-repellency challenges for outdoor apparel.” [Online]. Available: https://www.wtin.com/article/2018/november/191118/overcoming-water-repellency-challenges-for-outdoor-apparel/. [Accessed: 24-Oct-2019].
[4] N. Forsman, L.-S. Johansson, H. Koivula, M. Tuure, P. Kääriäinen, and M. Österberg, “Open coating with natural wax particles enables scalable, non-toxic hydrophobation of cellulose-based textiles,” Carbohydr. Polym., vol. 227, p. 115363, Jan. 2020.