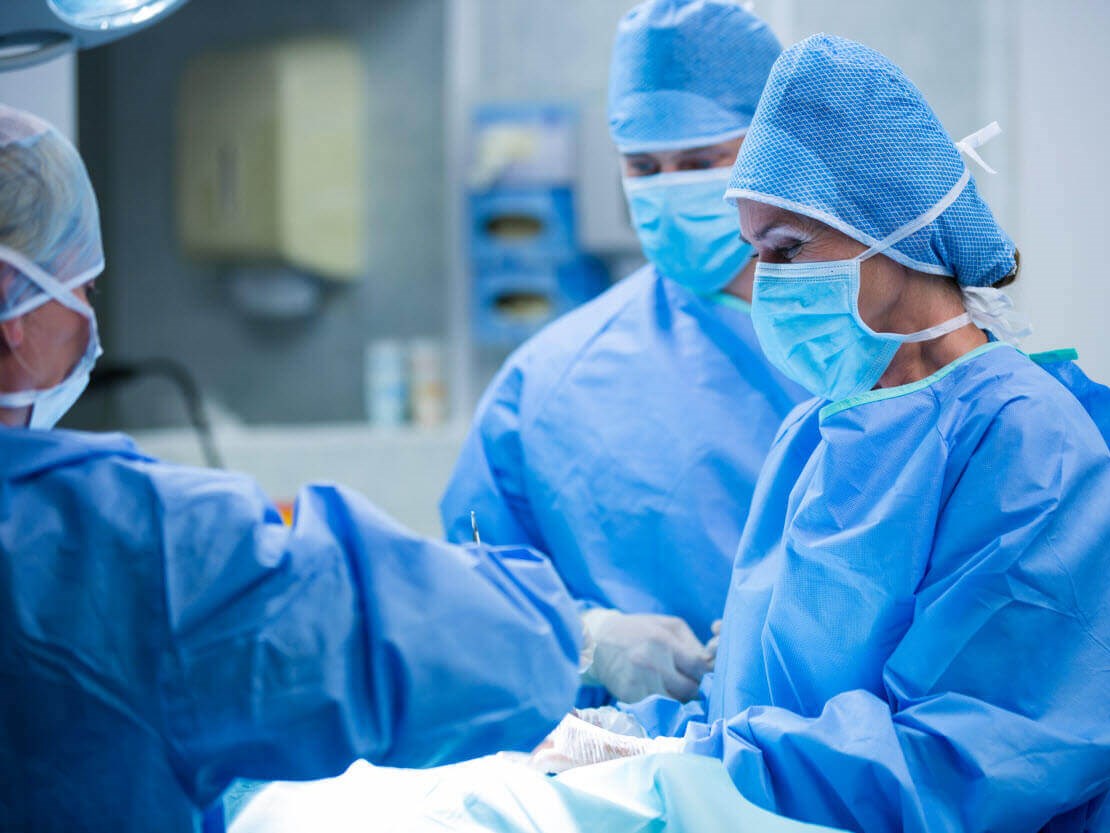
The company’s representatives Jason Zyglis and François Levac explain to Fiona Haran how its SmartView and SmartAdvisor systems identify and make sense of material defects in the production of nonwoven PPE.
At a time when nonwoven production lines are running at full capacity to meet the increased demand for PPE, it is important that quality isn’t compromised. Nonwoven materials provide critical air permeability while protecting against airborne particles, so these properties must be protected to ensure they are safe to use.
AMETEK Surface Vision’s inspection and monitoring solutions provide the required quality and consistency by identifying typical material defects across a range of nonwoven production processes, even at the high-speed production volumes required to support the manufacture of single-use items.
Combining cutting-edge software and proven hardware, Surface Vision’s SmartView and SmartAdvisor systems perform real-time detection and classification needed to identify nonwoven material defects. Uniting web inspection and monitoring capabilities, imperfections are captured by a combination of synchronised high-resolution monochrome or colour camera technologies and LED lighting arrays, capturing high-quality images using multiple inspection angles.
Explaining how the systems work, Jason Zyglis, division vice president, AMETEK Surface Vision, starts with SmartView.
“The product is focused on continuous manufacturing processes, ie anything that is unwound or wound up,” he says, adding that besides nonwovens, the system services materials such as paper, metals, glass, plastics etc.
“It’s not a camera like you’d have on your phone, which takes a picture that has an X and Y axis on it,” he continues. “This camera is similar to the scanner you have on your printer, or the dollar bill or euro readers used in vending machines … it’s called line scan technology.
“We use line scan technology so that we can have very high resolution with very controlled optical geometry inspecting the products as they move underneath the cameras. The system creates and records images as the nonwoven fabric moves through it to find defects.”
Zyglis explains that the heart of the system is Surface Vision’s advanced algorithms.
“As the product goes underneath [the cameras], the texture of the nonwoven translates into optical noise when you’re looking at it under a very bright light under a very high resolution camera. So, the first thing the system does is examine the variability of the nonwoven as it is passing underneath.”
This can prove a challenging task as nonwovens of PPE grades are often comprised of proprietary layers, typically spunbond and meltblown.
Outlining the types of defects that the system looks for, Zyglis says: “Typical defects would be discrete defects such as holes, contamination, hard spots, married fibres etc, as well as overall quality defects such as bad formation.”
In the past, camera technologies tended to capture black and white images, but as systems have evolved, colour camera technologies are now more commonplace. Zyglis explains that colour systems provide features that previously weren’t available.
“You can determine if something has a light shade, so things that almost have a burned texture to them, where they go through the hot calendar roll stacks,” he says. “You can find yellows and browns which may not be able to be seen when you’re just looking at a black and white camera.”
“Another thing to add,” he continues, “is that companies especially in the Asian markets are very concerned with bloodborne pathogens, specifically those coming from insects that can get into the manufacturing process.
“This is particularly important as such coloured defects means that a manufacturer is unable to sell a roll or is forced to cut out a section of material and patch it before it is eventually sent to the end user.”
SmartView can also detect light spots. According to Zyglis, gaps or light spots captured on spunbond material for instance, can mean that the density of the material is not optimal for either converting, barrier performance or rigidity.
“The challenge is: how do you find the critical light spot versus one that’s just part of the formation of the process?” Zyglis notes.
Companies must also consider the detection of holes in the inspection and monitoring process. Surface Vision’s systems are said to be capable of detecting down to 100 microns or below.
“Holes are important for a couple of reasons,” says Zyglis. “When we’re not looking at PPE, holes speak to issues with converting and efficiency in throughput, whether it’s going through slitters or something else. Finding holes on a line that’s moving up to 1,200 m/min, (50 miles per hour) 24/7 can be challenging.”
After this so-called cluster of contamination spots, the system can then start looking for other defects such as spinning defects, edge defects or hard spots – the latter describing the occurrence of too much material in one location. “It may not have the right porosity, which could change the properties of the inner face layer,” he adds.
Tailored approach
AMETEK Surface Vision was established by a group of technology pioneers in the late 1990s. According to Zyglis, nonwovens was one of the very first markets it entered into.
“We had a very successful product launch in nonwovens,” he says. “We have hundreds of nonwoven systems installed around the world at major nonwoven producers. It’s a competitive market, but we definitely have our slice of the pie.”
Surface Vision’s extensive applications experience ensures that these manufacturers receive the most effective solution for each application.
“We work with our customers to monitor defects that they’re looking for,” says François Levac, Americas business director, AMETEK Surface Vision. “They’ll come back and provide samples of these defects and we’ll come up with the best optical configuration. As the industry is moving we’re obviously trying to move with it and make sure we’re providing the right solution.”
Each SmartView system is a customised installation for each client – tailored to their production.
“It’s a two-step process,” says Levac. “Obviously, we want to classify the defects by using machine-learning/AI so that it’s not labour intensive. But it’s not just about reporting data, it’s about actually trying to make sense of the data. We want the production staff to be self-sufficient.”
“Every customer machine is a little different,” adds Zyglis. “We have installations on machines that are 50 years old and some machines coming out of Europe that were delivered months ago.
“Next, that information is passed onto very powerful self-learning – it takes all this noise and information and images we’ve found and makes it meaningful to the operation.”
The final step is data transferral. “We take the data and we either generate reports with it or we send this information in real time to the historians or the quality systems at these facilities, so we integrate it directly into their BI [business intelligence] process,” adds Zyglis.
SmartAdvisor
SmartView is supported by the SmartAdvisor system – a simple and reliable monitoring and inspection solution that maximises machine efficiency and yield rates. Described as a versatile and easy-to-use vision system, SmartAdvisor provides high-speed, multi-dimensional video monitoring and process analysis to a range of industries.
According to Zyglis, the two systems can work in an integrated solution. “Typically, SmartView is at the end of the line if you want to guarantee quality, so we work with these cameras and you can layer them down the machine towards the front of the process,” he says.
“They look for the origination of the defect. You can get multiple videos upstream of that exact same piece of product where the defect should be. The operator can click and go to the exact point to show where the defect started.
“We consider Smart Advisor a complementary product offering within nonwovens – cameras can find defects on their own or work synergistically with an inspection system.”
Supporting the industry
Since the Covid-19 crisis began, we’ve witnessed several companies across the textile & apparel supply chain shift their production to PPE. The nonwovens industry has been at the forefront of these efforts, as Surface Vision can vouch for.
“We’ve seen that manufacturers have taken their capacity and redirected it to masks and PPE,” says Zyglis. “It’s been a conversion of lines that were already producing something else and are now making the PPE, as well as potential for new lines and increased production.”
AMETEK Surface Vision is currently helping nonwoven material manufacturers meet the demand for these products through its inspection and monitoring solutions.
“We have received numerous messages from customers asking for support at a momentary notice,” says Zyglis. “To support them we’ve been staffing and adding resources to our global technical support teams. We have augmented services with some of the other resources we have to make sure that we can respond within hours, if not sooner, to a customer calling us saying they need help.”
The company’s technology has also proven particularly beneficial for the remote working strategies that many businesses have now adopted.
“As well as phone support, we have software that lets us tunnel into a client’s system in a very protected way,” says Zyglis. “We can run it as if we were at the plant. We have to do all this service remotely – in the past, we did this physically. So, we’ve had to rethink our approach.
“If nothing else, Covid has shown us that this remote training and service is probably here to stay, whether it becomes more cost effective or just for personal safety.”
Preventative maintenance support
Levac says that gaining access to the systems of nonwoven manufacturers during this time is particularly challenging as they ‘cannot allow any downtime or take any risks’.
To limit the need for on-site maintenance and repairs, while avoiding said downtime, Surface Vision has launched a new preventative maintenance service to monitor and maintain inspection systems remotely during normal operation.
According to the company, the service helps reduce operating costs and ensure that system performance remains at an optimum level, allowing work to be scheduled in advance, rather than waiting for problems to occur.
“We have seen that customers are shifting from a reactive service to a proactive service, so we had to do that as well,” says Zyglis. “Instead of waiting until someone tells us that something is broken, we are pragmatically going in and analysing their system to anticipate issues.”
After each system check, the company sends a report highlighting maintenance issues, potential problems, and recommended solutions.
“We can anticipate an upgrade path – we call it a lifecycle management programme,” Zyglis continues. “Most of our systems will live in a plant from 10 to 20 years after purchase, so over those years we offer compatible software – whether that be maintaining current operating systems … we have to be compliant with different security matters.
“We can provide a pathway for old systems to the latest software and features we provide. While we’re working with these clients we can also manage and upgrade their computer peripherals. So, we often work with our customers to do what we call a server upgrade or software upgrade.”
Through this service, actions can be taken before serious problems – including equipment failure – arise, highlighting the importance of trusted and assured quality surface inspection systems.
“Customers look to us for best-in-class technology,” says Levac. “And we offer services to maintain that technology and the knowhow to use it. That’s something we are proud of.”
To learn more about AMETEK Surface Vision, visit www.ameteksurfacevision.com
Have your say. Tweet and follow us @WTiNcomment