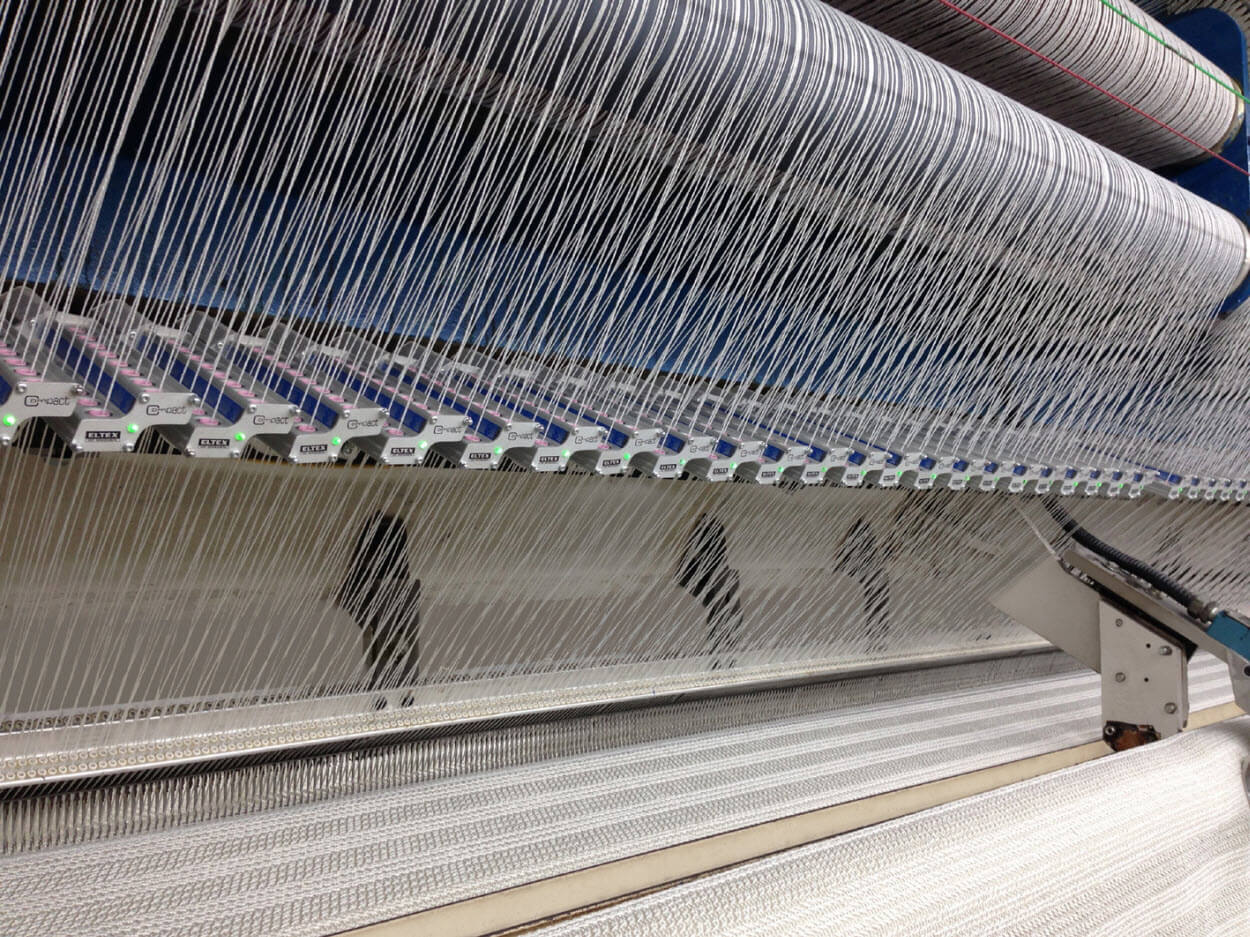
As more nations enter into what has been labelled the coronavirus recession, it has never been more crucial for companies to be cost-efficient.
Analysts have highlighted the benefits of a digitalised supply chain for many years, but due to investment costs a large proportion of textile manufacturers have been reluctant to implement the relevant technologies.
In the carpet sector, Eltex of Sweden has been researching and developing technologies that enable weavers to increase output volumes and minimise errors. This has allowed manufacturers to increase production capacity and reduce waste, the company says.
Eltex’s latest offering is the Eye Compact II, which was unveiled at ITMA Barcelona in Spain, last June (2019). The product was two years in the making and is an evolution of Eltex’s original Compact yarn monitoring system.
Eltex’s chief executive officer (CEO), Brian Hicks, says: “We focused our efforts on successfully miniaturising the componentry of our established Compact yarn monitoring system for carpet tufting machines. We have managed to get the Eye Compact II down to a third of the size of that system, which is in successful operation at carpet weaving operations around the world.”
Investing in the future
Digitalised solutions like this, which are a steppingstone on the long road to Industry 4.0 and the smart factory, are proving priceless for companies who have already embraced innovation. It has been suggested that businesses that embrace digitalisation will enjoy long-term benefits and, in many instances, these claims have already come to fruition.
When high investment costs are involved, companies are understandably reluctant to make the first move. But following a period of positive use cases, demand for digitalised technologies is now growing across the textile industry. This rise in demand was the motivation that Eltex needed to develop the Eye Compact II, Hicks says.
“Customers with the original Compact system experienced such a quick return on investment (ROI) that they pushed us for a solution for the machines they were running that were not suitable for the original Compact,” says Hicks. “Compact II is the solution for complicated graphics-driven tufting machines where space in the yarn path is very limited. The sensors need to be installed after the last puller roller and before the tufting needles, otherwise the roller could still be feeding yarns that will not be successfully taken by the needles. This is only possible with the extremely slim Eye Compact II units.”
Hicks believes the Eye Compact II is a savvy investment. He adds: “Our customers are typically manufacturing very expensive carpets made in a myriad of patterns, and if faults are allowed to occur they can be extremely costly.
“Eye Compact II sensor technology operates at a critical stage in high-end carpet production, where everything comes together in the entire manufacturing process,” Hicks continues. “The yarns and the carpet backing have already been produced and will be wasted if a fault is only identified later during the tufting stage.
“Another benefit is that the sensors can be arranged more closely, with each of them monitoring 16 yarn positions. Their robustness ensures that once fitted, there is little the technicians or operators need to do.”
But this raises a question: should companies be investing more in people or machinery?
Some unions fear that blue collar jobs will be at risk as manufacturers turn to automated solutions as a means of reducing labour costs, but it is also argued that machinery is only as good as the person operating it. The likelihood is that jobs will change rather than be replaced, but this would require businesses to retrain staff.
Additionally, statistics suggest that a business is more likely to succeed if it consists of staff and machinery that complement one another. And Hicks believes the Eye Compact II is a solution that enables just that.
He says: “Eye Compact II has been developed for the very latest machines which can consistently feed up to 1800 yarns from the creels at extremely high speeds. In these instances, it is simply impossible for an operator to fully detect missing yarns.
“There are a number of reasons why yarns go missing. The most common cause is when a bobbin simply runs empty,” Hicks continues. “But yarns can also be broken as they are fed through the creels or pulled out of position, which would also mean they were not picked up by the needles. Our system (Eye Compact II) provides a 100% guarantee that all of the yarns that should be in the tufted construction are being correctly fed into the primary backing. This helps to prevent expensive repairs at a later stage and also allows single operators to simultaneously control multiple machines.”
Expansion plans
Following its launch at ITMA 2019 in Barcelona, Eltex was happy with the industry’s response to the Eye Compact II. But the current recession caused by the Covid-19 pandemic has severely hampered sales. This year, the company was planning to build on its successful showing at ITMA and expand its presence in the Oceania region, and also in west and central Asia.
Sweden’s textile industry is struggling, but despite this the country is still home to a plethora of reputable OEMs, according to Hicks. He says: “Like many western countries, much of Sweden’s traditional textile industry has long since migrated east. However, what remains is a small but strong sector of specialised producers, in addition to major household brands like H&M and Ikea.
“The same can be said for the technology companies who are part of TMAS, Sweden’s textile machinery association,” Hicks adds. “All have developed highly-specialised, and often niche, technologies that meet specific needs in the textile industry. They are market leaders in terms of automated and sustainable solutions.”
From a technology perspective Sweden has a bright future, but companies there are concerned about what the recession will mean for the textile industry long-term. Eltex’s biggest markets include the US, UK, Belgium, the Netherlands, France, Spain and Australia and Hicks is hopeful that manufacturers in these economies will see the value in innovative technologies regardless of the recession.
He says: “By eliminating both production waste and machine downtime, manufacturers can not only boost their profitability, but also improve their sustainable footprint. This can be achieved by creating a quality product that generates less waste and uses resources more effectively.
“The carpet manufacturing sector is already undergoing a transformation,” Hicks continues. “Automated manufacturing has been on the rise for some time and the technology is extending to a wider range of functions. Sensor systems are very much part of this, not only for making individual machines more efficient, but for allowing data to be collected, analysed and acted upon across an entire manufacturing plant – often multiple plants.”
The reaction to Industry 4.0 relevant technologies at leading textile machinery exhibitions is evidence of the direction in which the industry is heading. If economic predictions are correct, it is almost certain that the current recession will impact on technological investment across the market for at least the next 12 months. But in the long-term, the need for digitalised solutions is unlikely to diminish.
Have your say. Join the conversation and follow us on LinkedIn