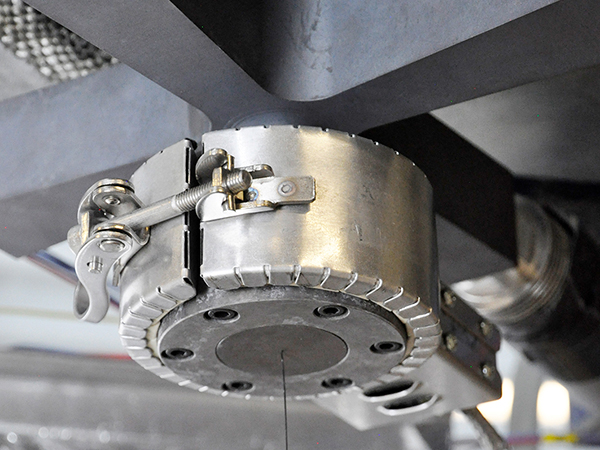
Researchers at the Institut für Textiltechnik (ITA) of RWTH Aachen University are exploring biobased alternatives to petroleum-derived polymers for textile applications. Jessica Owen reports.
We are all well aware that the world is currently facing a plastic crisis. Not only do traditional plastics such as polyester take hundreds of years to degrade and contribute to microplastic and microfibre pollution, but they are created from petroleum – a non-renewable resource that when processed emits carbon dioxide into the atmosphere which contributes to climate change.
The increased awareness for plastic pollution among the textile and wider industries has led many organisations to develop biopolymers. This term can mean a couple of different things: either biopolymers can be biodegradable or non-biodegradable and made from natural, living organisms; or biopolymers can be biodegradable but made from non-renewable resources such as petroleum.
Currently, these new materials account for around 1% of the 335 million tons of plastic produced annually, but global biopolymer production capacity is expected to continue increasing. For example, European Bioplastics and the nova-Institute in Germany reckon capacity will increase from around 2.11 million tons in 2018 to 2.62 million tons by 2023.
One biopolymer family that is now gaining interest is PHA (polyhydroxyalkanoates). PHAs are produced naturally by microorganisms, including through bacterial fermentation of sugars or lipids. There are different versions of PHA, all with different structures, and they are thought to biodegrade in both soil and marine environments.
PHA is currently of significant interest to researchers at the Institut für Textiltechnik at RWTH Aachen University. In the project called PHAtex, funded by the Federal Ministry of Education and Research of Germany (BMBF), the team is working out if this biopolymer can be meltspun into fibre for the textile & apparel industry.
“We are working together with the chair of Bioprocess Engineering at the Technische Universität Berlin (TU Berlin) where PHA is produced and then we turn it into a textile fibre,” says Melina Sachtleben, research assistant, Institut für Textiltechnik of RWTH Aachen University.
“TU Berlin produces the polymer with bacteria which utilises a wide range of carbon sources, including biogenic waste streams. This is good because no crops are required that could otherwise be used to feed animals or humans. The bacteria accumulate the PHA inside the cells as carbon and energy storage. After cultivation, the bacteria are harvested and the PHA is extracted from the biomass. We then receive the pure polymer and figure out how to get a fibre out of this.”
Sachtleben and the team have many different machines at their disposal to produce the fibre. They begin at laboratory scale with a few hundred grams and then move onto a bigger machine that simulates the industrial process. Afterwards, the team works with industrial partners who can actually produce at scale. In this project though, development is in the early stages, so the team works in the kg scale.
“There are other biopolymers in development throughout the research and industry landscape. Some are available to buy in thousands of tonnes for production, and others like this PHA are only available in small quantities for now,” she explains.
Aside from scaling the production of PHA, the next challenge is making it compatible with the meltspinning process – the manufacturing process used to produce synthetic fibres.
Felix Krooβ, researcher of Mono Filament Technology, Institut für Textiltechnik of RWTH Aachen University, adds: “First of all, we need a good quality polymer because the material’s quality changes the processing capabilities in the spinning process. The process is significantly influenced by the quality of the polymer as not every polymer can be processed into fibre.
“We start by drying the polymer because the residual moisture in the polymer can affect the whole process. We dry it in a vacuum overnight before the polymer can be used in the meltspinning process. Here, the material is heated up so that it melts. Spinning pumps then transport the molten mass where it is either extruded through a spinneret with one hole to produce monofilaments, or through up to hundreds of holes to produce multifilament fibre. Afterwards, it is stretched, has its tensile strength increased and is wound up on a bobbin.”
Although it sounds like a relatively straightforward system, the polymer needs to be tweaked for it to work. To obtain certain properties, polymers can be blended with other polymers. The melting point of these polymers have to be similar, in order for this process to be successful. For example, the polymer must have a high thermal stability. The team’s spinning lines can easily be heated up to temperatures of 350°C and so materials are usually spun 20-30°C above their melting point. However, some materials or additives already start degrading at those temperatures and the team does not want this to happen, as quality yarn can be obtained.
“We do our trials and study temperature, quality, what it looks like under a microscope etc and then provide TU Berlin with this information,” says Sachtleben. “They can then use this to adapt the molar composition of the polymer.”
Moving forward, another challenge for PHA is improving its hand-feel as Sachtleben says a material made from this would feel quite different to other textiles. That said, there are other biopolymers available that feel just like traditional materials in the finished product, proving again that there are very similar sustainable alternatives around. “There is a prejudice that the environmentally friendly solutions are worse than the originals, but we’re here to prove that wrong,” she explains.
Although this project is in its infancy, the aim is to prove that it’s possible to make fibre from this particular biopolymer and the team has about two to three years to achieve this. By the end, the researchers say that they hope to produce a garment, probably a knitted jumper that a company in eastern Germany will develop.
Besides PHA, ITA also works with other biopolymers. One example is the project called BioBase, which is part of the BioTexFuture forum – a scheme that funds projects focusing on sustainable innovation across the textile value chain. The goal of BioBase is to replace established petroleum-based polymers with biopolymers and to demonstrate that quality and affordability do not have to be compromised.
“We at ITA coordinate this project and we have 12 industry partners working with us, including Adidas, Schmitz Textiles and Huesker,” says Sachtleben. “The plan is to reproduce existing products using biobased materials.
“At the moment, we are deciding what product to produce and then we’ll evaluate all biopolymers currently on the market to see which one has the appropriate qualities that match our product. I’m really looking forward to doing this, it will be very interesting, and we should have a better understanding of the availability of biopolymers at the end of it as well.”
The BioBase project’s goal is much closer to market, but it will be up to the partners at the end to decide whether they want to make a go of moving in the direction of integrating biopolymers into their collections.
“We hope to prove that there are no drawbacks for companies to use biopolymers and that is the message we want to send to companies at the end of the project so that they will consider using them in future,” says Sachtleben.
The team is hopeful that companies will indeed move towards biopolymers soon, especially as countries like Germany and the European Union (EU) are funding a lot more projects these days to explore sustainable alternatives. What’s more, there are new rules regarding circularity in the EU and so this is putting added pressure on companies to meet these sustainability targets.
“It would be ideal if companies just wanted to intrinsically be more sustainable, but I’m happy with whatever works to push this process,” she adds.
Biopolymers is just one area of research that the Institut für Textiltechnik at RWTH Aachen University is exploring. Other areas include smart textiles, nonwovens, antibacterial textiles, digitisation of the spinning process and many more. With that in mind, WTiN will be regularly following up with the institute to bring you information about its latest work.
To find out more about the Institut für Textiltechnik at RWTH Aachen University, visit www.ita.rwth-aachen.de. And to find out more about PHAtex, visit www.bioprocess.tu-berlin.de/menue/research/projects/phatex/
Have your say. Join the conversation and follow us on LinkedIn