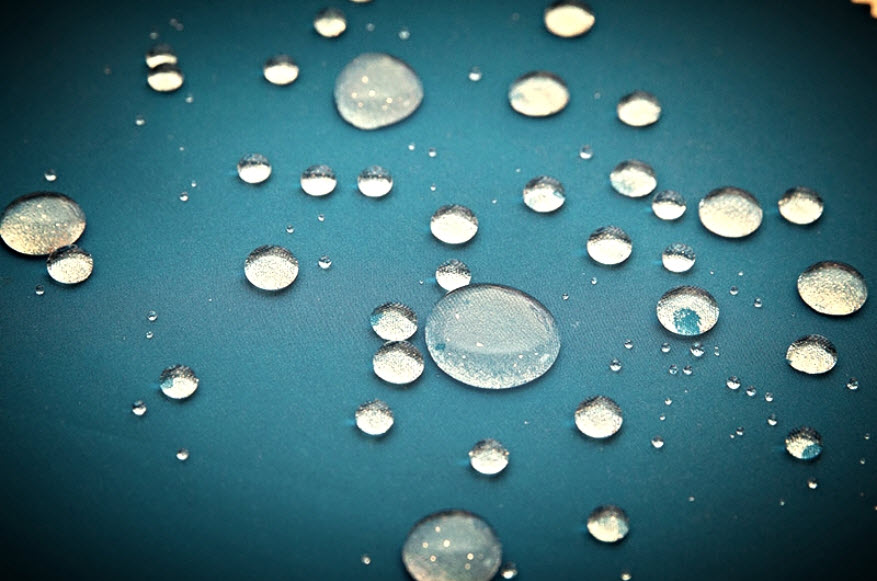
OSM Shield is introducing a number of new textile treatments this year, including V-Shield – antimicrobial technology based on hydrogen peroxide, and Zero – a new fluorinated chemistry with non-PFAS classification. By Fiona Haran.
OSM Shield creates high-performance fabric finishes that are ‘safe for both people and the environment’. Its philosophy is built around ‘Zero Tolerance’ – not only to odour, stains, moisture and oils, but also to PFOA and PFOS chemistries.
“We were advised to start with clean and then build the performance from there. And that’s what we’ve done,” says the company’s founder, Mark Walker.
“It’s more difficult to approach the world from that standpoint, but it’s paid off now that there is heightened awareness around cleanliness and the environment. And we’re in a nice position as a result of that.”
To that end, the company has announced a number of new product developments for 2021, with the emphasis currently being placed on V-Shield and Zero.
V-Shield is described as a ‘breakthrough’ antimicrobial technology – and OSM Shield’s ‘response to the Covid-19 pandemic’ – that utilises the natural ingredient hydrogen peroxide to combat bacteria safely and effectively. So far, it has proven effective against numerous bacteria, fungi, and viruses, including the 229E and OC43 human coronaviruses.
It is currently undergoing further testing in India against SARS-CoV-2, the virus that causes Covid-19, with the team confident about the results. “There’s nothing in the data that would indicate that it wouldn’t have the exact same functionality,” says Lena McCord, technology and innovations manager, OSM Shield.
V-Shield can be applied to many types of surfaces – from apparel, medical gowns and upholstery to footwear, yoga mats and luggage, for instance.
“It was initially intended to be used on medical devices; we needed a solution that was going to be biocompatible and safe to be used on the body,” says McCord. “It also needed to be a solution that prioritised antimicrobial stewardship, and we didn’t want anything that was going to form resistant mutations of any type of bacteria or viruses etc.”
The company landed on a hydrogen peroxide-based solution. “Nobody is a stranger to hydrogen peroxide – it is a common household product and an incredible antimicrobial agent that you can use to clean all kinds of surfaces,” McCord says. “Leave it sitting there and it’ll provide antimicrobial effect for significant periods of time. We wanted to adapt that into a textile application.”
How it works
When the hydrogen peroxide comes into contact with any type of microbe, it functions by destroying the cell membrane as well as internal cell structures, thereby killing the microbe and inhibiting the growth of microbial colonies. It replicates the same active chemical the human body uses to defend itself from bacterial invaders, explains OSM Shield.
More importantly, hydrogen peroxide is considered safe for people and the planet as it forms naturally in the environment from moisture and oxygen, and quickly breaks down to these components when disposed.
“Unlike metal ions like silver, which there is quite a lot of regulation on, especially when it comes to disposing of silver when you’re running that in a mill, hydrogen peroxide is going to decompose so quickly in the environment; it doesn’t leave any lasting effects on aquatic life or anything like that,” says McCord. “So, we found it to be a unique, robust and safe solution to provide antimicrobial function.”
What’s more, the treatment offers long-lasting protection thanks to its ability to naturally recharge itself. “Hydrogen peroxide typically doesn’t start to leave the fabric until 50-plus launderings,” she says. “You can even dilute it down into a spray, apply it to something and the peroxide will continually scavenge and replenish itself. You could theoretically infinitely extend the life of the finish, which is another unique factor compared with metal-based solutions.”
The company has developed two iterations of V-Shield, one of which is geared towards traditional apparel, says McCord. “That’s going to be more of a pad application. We supply the chemical product and then the mill or whoever is supplying the chemistry would add the hydrogen peroxide right before finishing [apparel production]. It has to be sequestered and applied immediately.”
The second iteration targets spray applications. “It doesn’t take into consideration colourfastness, hand-feel or comfort; it’s much more designed for a spray application onto a finished good. You could apply it to footwear in its finished form,” says McCord, who adds that the company can ‘100% recycle the chemical application’ bringing further environmental benefits.
While the need for PPE drove the speed of getting V-Shield commercialised and viable, McCord says that ‘one of the big players’ emerging right now is the upholstery market.
“[These types of products] are more permanent, so to speak, and are getting a lot more traffic than personal apparel – especially commercial upholstery in hotels and hospitals etc,” she says. “Right now, there’s a lot of functionality required out of those fabrics already, and with adding an aftermarket cleaning treatment for antimicrobial purposes, you end up destroying a lot of the properties of those fabrics – they already typically will have a DWR finish on them and that can be totally outstripped by the aftermarket cleaning solutions. So, there has been a big interest in getting a durable solution in the fibre.”
Walker says that the Covid-19 pandemic has played a significant role in this activity. “We’ve seen a change in terminology in the last nine months. Pre-Covid, people were looking for oil repellency, water repellency and stain repellency, and now the terminology – even in the textile or apparel world – is shifting to barrier protection in combination with antimicrobial efficacy,” he says.
“The awareness started in the medical world just from a protection standpoint, but now we’re in a world that’s changed. It’s a viro-phobe world and I think it’s here to stay for the medium-term and maybe the long-term, where people want their surfaces, their apparel and their upholstery to be able to have protection.”
He provides the example of a large upholstery group that OSM Shield works with in the US: “They shifted quickly to a barrier protection, still repelling stains because the consumer still wants that. But they also want a permanent – or as close to permanent – antiviral, antimicrobial and antifungal efficacy in the fabric.
“We’re looking to move to a system with this one particular large upholstery group where we can sell them a permanent finish that’s integrated into the fibre of the upholstery, give them that barrier protection and then give them a spray solution where they can spray it down and get that peace of mind, but what they’re actually doing is allowing the V-Shield to recharge. So, you may have a finish that lasts longer as the consumer is providing long-term benefits to the fabric.”
The efficacy of V-Shield can be enhanced further by combining it with OSM Shield’s repellent finishes. Walker references Norr – its fluorinated line of chemistries that provides resistance against oil, stains, moisture, odour, and mold and mildew.
“Because there are binders in the V-Shield that are similar [to Norr] from a crosslinking standpoint, the repellent finish binders actually add durability to the V-Shield, and the V-Shield binders add durability to the Norr repellent finish,” says Walker.
Zero
Zero is a new fluorinated chemistry from OSM Shield that ‘avoids all health and environmental scrutiny’ due to its non-PFAS classification.
The innovation lies in its unique chemical structure, as Walker explains: “There are two types of repellent finishes: fluorinated and non-fluorinated. And there’s a movement of people going from fluorinated to non-fluorinated. The primary reason is that there’s not necessarily anything wrong with the fluorine, but in a fluorinated system application you have per and polyfluoroalkyl compounds in the monomer base. And that PFC, if it’s handled properly, is 100% recycled or reactive, or at least to 20 parts per billion. But there is a fraction of people who aren’t interested in that story – they don’t want the PFC to be in the conversation.
“Because there is PFC in that monomer backbone – defined as PFAS classification – people have leapt to a non-fluorinated finish in certain instances because it gets them out of that classification,” he adds.
Explaining fluorinated repellent chemistry structures, OSM Shield says that a PFAS chain structure resembles a comb comprising a backbone with ‘teeth’ or ‘branches’ coming off of the base. The higher the number of fluorine-carbon bonds (indicated by C8, C6, C4), the taller the teeth or branches. As the teeth become longer, they become more unstable, increasing their chances of breaking off and entering the environment.
“If it’s a robust polymer, the theory is that it doesn’t break down and it’s not harmful to the environment, but the fact that it occurs has people paying attention to it. So, the Zero technology that we have is not a chain structure,” says Walker. “It also does not contain any per or polyfluoroalkyl compounds in the monomer structure, so it’s a non-PFAS classification … it does not require curing like all other fluorinated chemistries do; it provides an element of super hydrophobicity.
“It’s a better option than the best C6 in the environment today,” he continues. “And it replaces the need for anybody to move to the non-fluorinated platform because we’re going to give back to them all of the performances, including oil, without having the PFCs at the monomer base. Right now, it’s one of a kind.”
The company expects the Zero chemistry platform to be commercially viable before the end of 2021. Besides that, it is also developing a non-halogenated fire-retardant solution and is close to commercialising a dual-sided finish, called Wik + Repel, in partnership with a speciality textile equipment manufacturer. This would enable most woven and knit fabrics to wick on the interior and repel on the face.
“It revolves around some spray technology that we’re working on,” says Walker. “We’re excited about that; we think it has some really neat applications in either warm weather applications or high exertion applications for garments that are against the skin: where you need moisture management but you still want repellency on the outside.”
In addition, the team is currently carrying out some work with indigo denim to achieve improved durability through new types of proprietary crosslinkers and resins.
“Our goal is to be able to provide denim brands a solution that will take you to 20-30 washes and give you a nice robust performance,” he adds.
Innovation centre
OSM Shield is headquartered in Denver, Colorado, US, which is also the location of its innovation centre. It focuses on three application methods: pad, yarn and finished garment applications.
“[The innovation centre] spends time working on initiatives that are applicable to taking a specific customer to market for a commercial application,” Walker explains. “And they also spend typically 25-30% of their time on different innovations – things that don’t necessarily have a home yet but they try to get us ahead of the technology curve.”
These efforts are supported by the company’s partnership with North Carolina State University. “When I founded the business, I took some concepts to [NC State] and hired one of the doctorate professors under a private sector consulting agreement,” says Walker. “We then put our company into a development mode for a number of years to try and broaden the platform that we have, and also to make sure that the things we were trying to take to market were commercially viable.
“We have a services agreement with NC State, which gives us access to all of the equipment that they have at the university, and to also make sure that the intellectual property resides with us,” he continues. “Today we have three doctorate professors at NC State under private sector consulting arrangements and we work with them weekly, problem-solving and troubleshooting existing issues that we have and working on new innovations.”
The company also has offices in the mountain towns in Colorado – where Walker lives – besides representatives all over the world including the UK, Europe, Bangladesh and India. It is also bringing on a group in Indonesia ‘as we speak’, he reveals, adding that the company also has a wholly foreign-owned entity in China. “This allows us to function as a Chinese company when conducting business with Chinese mills,” says Walker. “We buy and sell goods and services in Chinese currency (RMB).”
Performance story
Positioned as a B2B company, OSM Shield works with brands to develop the ‘performance story’ that they’re looking for, always beginning with the clean chemistry approach.
“We’ll sit down with a customer and let them understand the different technologies that we have and then listen to them as to what performance story they’re looking for, and we build a storyboard for them around the different chemistry applications that we have specific to the different garments that they’re looking at,” he explains.
“That brand will then take us to their mill, and we support their mill to be able to apply the applications that we provide to them. So, we have a distribution component to our business; we bring in all of our own auxiliaries, we create custom formulations, and then we handle the supply of chemistry to the mills we work with.
“We’re really looking to resonate with brands and with mills as the best provider of chemistries, and most of them in turn will take our chemistry applications to market [under private label brands],” he says.
OSM Shield doesn’t see itself as solely a chemical company, but rather ‘an expert in applications knowledge and formulations’ – taking different chemical auxiliaries and formulating them to meet the requirements of different substrates, says Walker.
“We don’t always have something that no one else has but I would say that we’re more precise and studied about the applications that we’re making and how they pair best with the fabrics that we’re trying to derive the performance attributes from.”
To learn more about OSM Shield and its performance fabric finish portfolio, visit www.osmshield.com
Have your say. Tweet and follow us @WTiNcomment