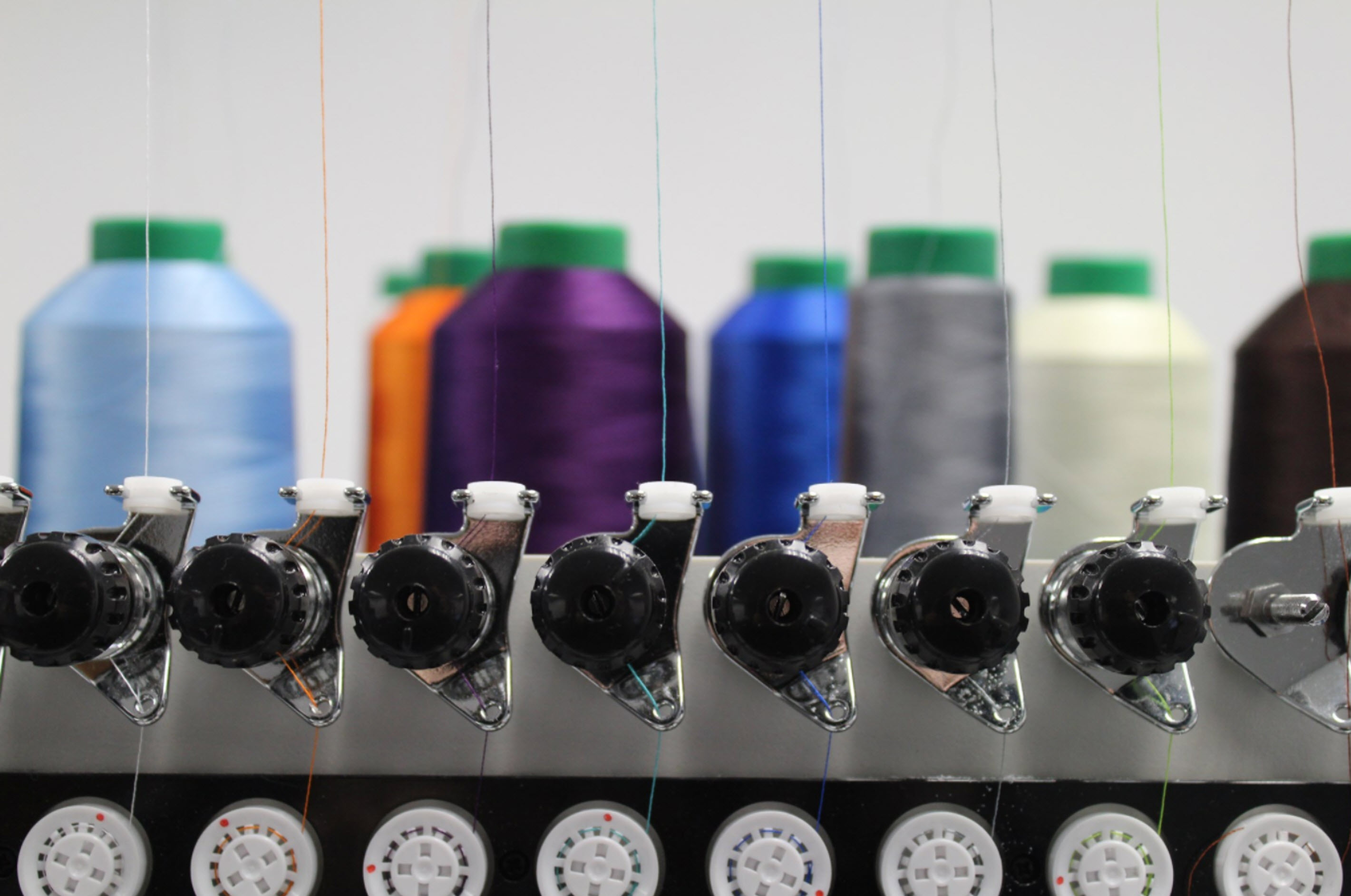
Ep. 73: Technical embroidery is a ‘massive field of opportunity’
By Jessica Owen
This week’s guest on The WTiN Podcast is Topher Anderson, manager, technical embroidery application at ZSK Research and Training Center.
Founded just a few years ago, the ZSK Training and Research Center is a subsidiary company to ZSK Embroidery Machines. Based on the West Coast of the US, the Center has been set up to help anyone from students to established companies to find solutions concerned with technical embroidery.
In this episode, Anderson explains the basics of embroidery and how it has transitioned from traditional applications such as baseball caps and T-shirts to technical embroidery including smart textiles and composites. He talks through the capabilities and opportunities that lie within technical embroidery, and he outlines the different machines and how they can be modified for emerging products. Elsewhere, he talks about how embroidery helps to reduce waste, bolstering sustainability, and how the team is improving the data and connection between the machines to improve efficiency and workflow.
To find out more about ZSK Research and Training Center, visit ZSK Research & Training Center (zskusa.com).
-
Transcript
This transcription has been AI generated and therefore may have some inaccuracies.
Ep. 73: Technical embroidery is a ‘massive field of opportunity’
This week’s guest on The WTiN Podcast is Topher Anderson, manager, technical embroidery application at ZSK Research and Training Center.
Speaker 1: WTiN
Speaker 2: Topher AndersonSpeaker 1
Hello, my name is Jessica Owen, and I'm part of the team here at WTiN. And this is the WTiN, and podcast. Join me and my guests every other week as we talk about new and interesting innovations from across the textile and apparel industry. Whether it's talking to sustainable startups quizzing experts on the latest research and development, or chatting to companies about their most recent products, you can rest assured that the WTiN and podcast will connect you with everything you need to know. This week, I am joined by Topher Anderson, who is the manager of technical embroidery application at the ZSK Training and Research Centre. Topher talks about the capabilities and opportunities within technical embroidery such as smart textiles and composites, how the sector can bolster sustainability and upcoming developments to look out for such as improving machinery in line with industry 4.0.Hello, Topher, it's lovely to finally speak with you. How are you doing? Good morning.
Speaker 2
Good morning. I'm doing well. How about you?Speaker 1
Yes, not too bad. So I understand that you're based in Seattle. How's everything over there?Speaker 2
It's going wonderfully today. We have a nicer overcast day out here. It's a it's a beautiful Seattle morning. Yeah.Speaker 1
And what about COVID-19? I asked everyone I speak to situations like so is it improved at all? Or?Speaker 2
Yeah, that's a good one. So things up here starting to open up a little bit more. I've noticed a lot more different sampling work and different things coming through the lab. But I mean, even just getting back out to normal things in the city are starting to open up again, which feels good. So restaurants are starting to come back and everything else. So it's, it's getting back to normal. I'm thinking the next couple of months will kind of get to a normal pace of life for sure.Speaker 1
Yeah, yeah. That would be great, wouldn't it? Okay, well, I mean, you're here today then to talk about the Zendesk Kate Research and Training Centre, which is I think it's the embroidery machine manufacturer sort of side company. Is that right?Speaker 2
Yes. So ZSK Is that us CA is a German embroidery machine manufacturer over in Krefeld, Germany. And what they decided a couple years back was, you know, everyone's starting to ask questions about technical textiles and technical embroidery in specific that they wanted to set up a spot out here in the US specifically on the west coast that there's somebody that can answer different technical textile problems or different technical embroidery problems. And so we went back and forth and we decided to set up a lab here in Seattle, the ZSK Research and Training Centre where we do that kind of work.Speaker 1
Right. Okay. So just to provide some background then tell me a bit more about Zetas K machines. I mean, they quite they've been around for quite a while then unlike the training centre.Speaker 2
Right. So they've been around for quite a long time. I don't know exactly the year offhand. But it's significantly a long time. They started. I remember actually, I think they started way whack back as a weaving company, and they transitioned an embroidery machines, and they've made some wonderful equipment. And they're very open to trying new things, which is I think the the key piece to me, they're willing to modify some equipment or make new parts or be able to optimise things for higher efficiencies and have high accuracies, which is what you really need if you're going to stitch smart textiles, or you're gonna put circuit boards down into pieces. So they're very accommodating in that.Speaker 1
And so before we talk any more about embroidery actually, I mean, tell me a bit more about yourself, then I think, when we were off air, you said that you went to ITA Akon, university, it'd be great to know how you sort of fell into this industry.Speaker 2
So my, my background is windy back and forth. But I liked it very much that way. So I started actually as an art major that transitioned into an architecture major that transitioned into an architectural engineering major for undergrad. I enjoyed, I enjoyed visual, but I also enjoy a lot of the technical behind it. And I think that's been the common search for me is how do you combine something that has an aesthetic property was something that has a functional or engineered property, and so I knew that part was something I was looking for early on, but it was kind of hard to, to mould that into a single career piece. So I did a couple other things inside of there. I went over to Germany, like I said, for them to do my Masters over there and I was in the ITAR, which is the textile engineering school over there doing textiles for MRIs and PET scanners for molecular imaging. And then I had a blast over there came back to work on my PhD in textile engineering. Took a break to do some circuit board and satellite spacecraft work at Lockheed Martin for a while. And then after that went out to Microsoft for a bit to do some work up there in the Apply I'd science group, I had a professorship back in Philadelphia full time for a while. And then after that, all of that I decided, You know what, I'm gonna start to do some more, some more teaching, but also in kind of a corporate setting. So that's where ZSK kind of came in. And as soon as I found, you know, you found the right thing when you're doing it every day, and it's not work. It's play. So it's perfect.Speaker 1
Yeah, yeah, well, that really is a long and winding road. But it sounds like it's paid off. And it was what you were meant to do, by the sounds of it. Absolutely. So let's talk a bit about embroidery then. I mean, I've already admitted to you off air that I'm not an expert. And I'm sure some of the listeners aren't either. So do you mind giving a bit of background lesson in what embroidery is what it's used for, and the machinery that's used to do it these days?Speaker 2
Absolutely. So this is exciting. I love this one. So what we start with us, so for traditional embroidery, you can think of like shirts and caps, that type of thing. And in traditional embroidery, the the basic mechanics of it are that you have a a stitching needle that holds a colour or some kind of thread, and then you have a rotary hook underneath it that makes a knot from that. And it's very similar in that regard to sewing in the way that the stitches are manufactured for traditional embroidery. Now the difference with embroidery machines now is you start to have a frame that can be controlled CNC control frame, which is a robotically controlled frame that lets you start to do things or place things repeatedly. So that's a step up from hand sewing that you don't have to manually move your fabric in the machine, the machine moves for it. So that's where embroidery stayed for for quite a while, um, isn't that visual shirts, caps, tapestries, that type of thing. There was an interesting project that was worked on about, I would say 1015 years ago, where suddenly an automotive customer came to us and said, you know, we really want to embroider a wire down. And it turns out, this would be the wire that would be in carseat heaters. And they were looking at a way to do that. Because what they do now is up at that point in time, they hand glued these down into into the fabrics, which is a very laborious process. So So yes, Kay had looked at that. And we went back and forth as a internally as a company. And we made a machine that allows you to automatically embroider a wire down into into a piece of fabric. And that's what opened up the doors because suddenly, the fabrics became functional. And that opened this real big door of technical embroidery. So technical embroidery now is a, a much bigger picture than the traditional embroidery or traditional textiles that were worked on. So for technical embroidery, we do parts in smart textiles, which is a big one. And smart Textiles is things like stitching circuit boards down, creating different circuits that are very large or interactive textiles. This could be things like this could be like wall hangings, this could be carpet, this could be wearables on the body. These could be things that are used in VR, these could be things that are used in sportswear, just different ways of interacting with cloth or materials or flexible materials to get data out of them and to be able to provide some response. So that's one whole set. Then we have another set, which is in the composites world. This is a really fun one. This is the one I'm seeing the most interest right now, where we can make parts out of carbon fibres and carbon fibres extremely lightweight and extremely strong. And what you can do with that is you can start to make parts for spacecraft or for aeroplanes, or right now a lot of it is looking at cars because as cars become electric and more autonomous, they have to get lighter weight. And one way I can make a lighter part is take a steel part out or aluminium part out and put a fibre part in which is stronger and much lighter. And that way you save on fuel costs per ride. And so that's one that we're seeing right now. And then like I said before, too, we have a whole niche of other ones which I call like wire embroidery or assembly embroidery. I did a I did a company actually with a co worker of mine creating masks for for COVID. And that was a new way of assembling a transparent mask because we can use stitching to put different materials together in different combinations. So technical embroidery is is this massive field of opportunity of different problems that companies want to solve. And sometimes you need a flexible material or something a little outside of the box to fit that. But once you kind of get in that spot it's it's a really a really interesting and worth while field to explore.Speaker 1
Yeah, sounds it I mean, just going back to the whole smart textile embroidery sector. Where do you start with this then? I mean, do you have to embroider differently at all to you know, account for these new materials. I mean, it must be quite hard for you.Speaker 2
So there's there's a lot of differences that come up. And, um, a lot of that has been made by changes in electronics to be more closed loop systems. Mechanically, the equipment has always been very high, high accuracy, which is one of the things they've prided themselves on for many years. And that's you need that accuracy, if you're gonna start stitching something like a circuit board or something very fine or a highly controlled design down. Because if, if I send a needle through the middle of a circuit board, something's gonna break there. But if I know where those holes are on that board, I can start to be able to control that in a nice way, it becomes a much more reliable and scalable process there. There's a lot of different things that plug into the machines too. So one of the interesting ones I love is like cameras. So there's different camera alignment systems, that can detect holes in different things to be able to modify the embroidery code on the fly, to be able to hit certain tolerances. And that's, that's one interesting way of you getting accuracy. There's devices that put sequence down. So if you think of a sequence like like, you know, like a ballerinas dress and the little kids dress, you have those little plastic spangles or sequins. Well, a sequence can be a single sided circuit board. And now we can start to put little electronics as electronics get smaller and smaller onto each individual sequence. And if we can already stitch them down extremely quickly, and we have high accuracy will now we can start putting electronics into these very large textiles for temperature sensors or light sensors or measuring how close somebody is or touch. All of these things now become playable materials in that textile structure. And that opens up so many creative doors for all kinds of opportunity there and technical embroidery. Personally, I've always liked embroidery from the perspective, I used to do a little bit of Jacquard weaving and undergrad. And there's a couple other techniques. But embroidery lets you have complete control over that x y. So there's no warp and weft as there is in a in a traditional loom. And for knitting to you have to look at your course. And we'll structure for embroidery, we're free to move x, y, and actually even Z a little bit too, which is kind of fun. So you really can start to make circuits, as you would design them in a normal circuit board process. And to be able to use that process and that knowledge that you already have, allows you to move faster with them. So there's a lot of fun inside of technical embroidery and smart textiles.Speaker 1
So being Research and Training Centre, then do you have quite a lot of people coming through your doors looking how to take advantage of embroidery for smart textiles? I mean, what are the sort of things that these students are looking to learn in this area?Speaker 2
That's great. So we have Yeah, we have a whole gamut. We have big tech companies coming through, we have small startups, we have a lot of students, we have composite companies automotive, it's interesting, because it's always different every day is a totally different set of people coming through in different technical problems, which I enjoy a lot. But um, from that perspective, usually like the process will be somebody comes with a problem that they've they've seen that they want to know, is it possible to solve with embroidery? And some of these are pretty abstract problems? How do I hold two metal parts together in reliably? Or how do I add more reinforcement between two layers of plastic? Or how do I put two weird materials like aluminium and mylar together into a single material? A lot of these come through and we'll start to look at out of the lab? Are there processes that we can do to do this in a fully and high reliability way? And then the second one is because embroidery scales so well, because people have been scaling embroidery for 50 years now. We can start to use those efficiencies that are gained in that scaling manufacturing, to be able to take one of these prototype samples and then scale it out very quickly. And that can be a very cost effective way to solve interesting problems.Speaker 1
Well, that was actually going to be one of my questions is that a lot of people in the smart textile industry say that their biggest challenge is being able to scale up all of these things. So you're saying that actually maybe turn to embroidery like it might be the solution for you.Speaker 2
So embroidery, I think from again, from my my, my experience, my opinion of working with it is, is a scaling first technology because anything that you make on a small machine is immediately transferable to a large machine. They're designed modularly. And so if I can make, I don't know, one part every 20 minutes on a small single head machine on a 50 head machine, you just multiply that out by 50. And that's how many parts you get. And so because it starts with a manufacturing first, that's where you can start to craft your solution around the technology instead of coming up with a prototype. So one of the things that we did at Microsoft a lot is you'd come up with a new prototype, and that would be really exciting and interesting and it would be pushing the balance and a lot of different things but then you would try to have a prototype that maybe has 50 wires that have to be saw, soft hand soldered, and you would try to find a company somewhere on Earth that would hand solder 50 wires into a small A textile everyone passes on, it doesn't matter what the company is everyone says no, we're not doing that it's too tedious, too much risk, blah, blah. And so if you look at embroidery first and you design around the manufacturing technology, then you can say, well, you know, I can't really solder but I can do a conductive thread into a circuit board automatically. And I can have that circuit board placed onto the machine automatically. So actually, you know, I don't even need to solder, I can just do conductive stitching into the board and conductive stitching out to my parts. And now suddenly, instead of having that solder step, it's a fully automated step. And that drops priced immediately. And then suddenly you you show manufacture this and they say, Yeah, I'll do that. That's a piece of cake. It's just like normal applique technique, and you get a much better a turn there. So I think in that regard, being able to use some of the perks of the technology from the scaling site first, help with the design iterations help with growing the concept and help also integrating things together different technologies and different parts.Speaker 1
Well, I mean, like you say, it sounds like there's so many possibilities. Are there any limitations at all? Is there anything you can't do?Speaker 2
So, I mean, I've done embroidery on different materials, Fleck, I don't even say fabric anymore because actually only about half of it is fabric but fabrics, plastics aluminium, I had a customer come through when embroider cheese for his projects, we put cheese down and butter that gelatin for fibre. For biomedical. We've done fibre optic embroidery. So it's not, it's not even what you think from a textile perspective anymore, you can start to embroider things into thin balsa wood or even some projects embroidering into metal that has some holes already set that we can start to stitch through all kinds of opportunities there. So it's, it's so open that it's hard to kind of constrained what is possible, what isn't different threads, different wires, carbon fibre, like I said fibreglass basalt fibres. I would say in general, you want to keep the embroidery pretty, pretty flat. So you're going to go with a maximum of one centimetre really above the embroider table, but as long as you stick within that embroidered one centimetre height, and I don't know how big your part is, maybe it's a metre, maybe it's two metres by two metres, whatever that size is, then you're totally in that range of maybe it works in them, we can try it and and see what happens.Speaker 1
Okay, right. Good advice, then. So being in this area, you guys must stay on top of all of the latest developments in technical embroidery. So have there been any innovations, as wacky as they may be that have caught your eye recently?Speaker 2
Hmm, that's a great one. I think the two that are really interesting to me are bead embroidery, which is a whole new way of putting beads down. So if you think of a tiny little glass bead, they've been woven into different fabrics. For a while they've been hand placed, they've been glued, there's a lot of techniques that have done it, but I'm putting them down with an Embroidery Machine seems particularly interesting to me, because you can also look at a bead as a carrier for electronics as well. So suddenly, maybe there there is there's RFID beads I could be making there are LED or light up beads. Beads allow for a different form factor. And they also allow for a different visualisation that I think might be an extremely exciting way of integrating new properties into different textiles, specifically smart textile. So I'm extremely excited to see how that one goes. Because that's really just come out. There is another piece that just came out looking at putting, putting different circuit boards down with the machine automatically, which is an extremely exciting one. And that's a way that we can start to integrate fully, fully closed loop manufacturing to be able to integrate soft textiles and hard textiles into one. And so hard textiles have the benefit that you can mount components to them. So M's processors you can put down, you can put your resistors, your caps, all of your sensors and supporting electronics, they all have been designed to mount nicely to hard pieces or fr for rigid boards. But rigid boards, if I'm going to make a big thing are quite expensive. So you can imagine if I'm going to cover a wall in rigid circuit boards, that's going to be 10s of 1000s of dollars, especially if you want one single piece. But if I'm going to cover a wall with a fabric that has sensors in that, well that's a very, very affordable proposition then, because all of the electronics can be mounted to those little tiny hard boards. And then the fabric itself can be that carrier with all the conductive thread and wiring in it to be able to pull those circuit boards apart so that you have a bigger distance and suddenly your cost is much much better there and you have more capability because the fabric can move. So think of like think of like window curtains. You could have window curtains now that can detect how much sun is being hit on them and can automatically adjust them to open pores inside of them to let more light through if it's cold, or to close up so that more like it's blocked. And I think in that regard, there's architectural applications. So I think being able to place circuit boards down automatically fuses a few of these different technologies. So we can start to look at the connection between soft and rigid.Speaker 1
So at the sort of innovations that you've mentioned today, then any of these commercial or is this all still in the r&d phase at the moment?Speaker 2
That's interesting. I think actually, all of those that I mentioned, are either commercial or quickly becoming commercial, I'll put it that way. There's some there's some really interesting movement here. And especially in smart textiles, right now, it's, it's an emerging field, a lot of the technical textiles are really emerging the past five to 10 years, you're starting to see interest worldwide in all different industries, from automotive, to manufacturing, to electronics, production, to wearables. And so there's a huge surge here of different technologies that are coming in ideas that are coming in, and a lot of energy around that emerging markets, kind of where 3d printing was, I would say, about eight years ago. And you can kind of feel how that's starting to go. And people trying to figure out how to integrate these, these technologies in so I think there's a lot happening in that commercial space very, very quickly to try to get some of these technologies out so people can start trying around with them and exploring how they fit their own their own ecosystem.Speaker 1
Yeah, well, sort of leading on from that, then, I mean, what are the main business opportunities and areas for growth in the embroidery sector? I mean, is there any capability that is sort of less known by companies and brands that they, you know, could take advantage of, and actually, it will give them some sort of competitive advantage?Speaker 2
Yes. So I would say the big one, right at this exact moment is in the composite space. There is a lot going on, and a lot of interest in very big industrial equipment to make these composite parts, because I can make extremely strong and extremely stiff and extremely lightweight parts very quickly. And I think that's really a game changer when you're looking at fuel efficiencies and a couple other pieces of green green defying or making the the economy more sustainable. And so one of the big ones I've had recently is commingled composites. So they there's companies out there that take carbon fibre, and they open the fibres up, and they put these really cool thermoplastic fibres inside of them. They could be like nylon fibres, they could be polycarbonate, there's a whole bunch of materials that they can insert inside of these carbon fibres. And they close the fibre autobackup. So when you feel in your hands, it feels like a cord, it feels like a fibre it's very it's, it's not a plastic at all, it's not rigid, it's very soft. It's easy to work with, it's easy to run in the machines. And then what we can do is we can put those down in patterns that are exactly the correct mechanical alignment, so that the fibres create their strongest, their strongest properties in the direction that they need to be strong. And what happens after that is we take these things off the machine, they're still soft at this point, they feel like they feel kind of like patches, almost they can be as as big as a smallest cell phone all the way up to surfboard size. And what you do then is you can put them in an aluminium hot press mould, and you hot press them and suddenly all those plastic fibres fuse inside. And when they fuse, they create this really rigid piece because that's the matrix material for the composite. And the fun part of this is the fusing happens in 2030 seconds, so you can hot press 123 and a new part comes out. And that allows high sustainable high throughput for those pieces. So there's a huge amount of interest in how do we use this for everything from sports equipment, to automotive to spacecraft, and, and even beyond that, because you have some the ability to fix damage in there. If you crack them, well, you can compress them again. And they kind of fused back as well. So lots of fun inside of that. That space. That's the one I see right at this exact moment is exploding and growth.Speaker 1
Yeah, that's so interesting. I mean, you said at the very beginning, how far embroideries come from just your shirts and caps. But I mean, you're coming up with things I would never have considered. It just sounds so interesting.Speaker 2
It's a joy. I mean, I think a lot of people kind of, they'll see something maybe at a trade show or some pictures online and they'll come to the lab here in Seattle to visit and then I have different samples and other stuff. And then like can really show like what the equipment is capable of. And people. I mean, there's there's, it's, it's not even embroidery anymore. It's it's additive textile manufacturing. It's a totally different field almost because you're working with weird materials, you're working with strange concepts. You're working with interesting technical challenges, from mechanics to electrical, to fusing different materials. And I think that opens the doors to all the different possibilities that we can do, both commercially and then also for just fun hobbyist projects.Speaker 1
Yeah, definitely. I mean, let's talk about the equipment then actually because we've talked a lot of about the different application areas and how they're expanding. But what about the machines themselves? Are they they quite traditional still? Or are they following this industry? 4.0 trend and becoming more digital?Speaker 2
Great, great question. So the machines, I mean, they're still ZSK still make some of the high end, traditional embroidery machines for high end linens, bed wear that kind of thing. And they have a very good selection of those. But um, they also make these technical machines which allow a whole bunch of different materials to be used. So we have embroidery, we have three different types of embroidery, we have F head embroidery, which is what we think of when we think of traditional embroidery machines that is, in general, like caps, shirts, fine linens, f hat is what we've modified to do circuit board stitching, we've modified to do electronic sequins, we've modified to do a lot of these different electronics. So that's kind of the most versatile one that people know when they see embroidery. The next head over, we have this called K head embroidery, which is Chanel embroidery, or moss stitching. This was very popular, you know, that's 6070 style varsity jackets, where you get the fluffy loops on the back and you get chained stitching around it, it's a very, it's a visual style that we don't see quite as much anymore, it's starting to come back a little because it's in rotation. But it allows for very loopy structures. And the loops are interesting from electrical properties, because suddenly I can make things like textile electrodes to read heart rate, or to read muscle signals, or even to read or even to like stimulate different muscles, there's a lot of different plays in that shinier embroidery piece, especially since it's one thread, there's no, there's no Bob, and there's no rotary hook, it's a single thread that loops through the fabric. And so that opens some doors. And then there's another final one, which is the newest embroidery had called W had embroidery, which you can think of as wire embroidery. But that's where we can run a thick material or a stiff material, we can run a 3d printer filament through it, we can run carbon fibre or glass fibre, or we can run fine wire 63 micron stainless steel wire all the way up to Ethernet cord. And that one allows us to put strange materials down into the fabric regardless of how thin they are, how thick they are, what your tension is on them. And that lets us fuse different things together. And it's kind of I think of that kind of as the really the additive machine had, you put materials in interesting patterns together to do technical things. So the equipment now is shifted from just that F head style from the very beginning that was like shirts and caps to these combination machines that let you take one technique and go over it with another so I can run a wire and run it down through the entire piece. Maybe it's a heating wire to be able to warm up a jacket or something. And then I can stitch that over that wire with some conductive thread and then automatically connect that to a circuit board. And now I have no soldering in there, I have all the connections done. And that way that piece comes off the embroidery machine has a single finished piece, ready for whatever the next process is. And sometimes it's ready to go right there. So the equipment has kind of shifted to these to these technical machines, we call them that allow more capability, they allow different things to be plugged into them. They allow a high amount of adaptive adaptability, for whatever your technical processes are your technical challenge.Speaker 1
And these are ran by like software, then I mean, can you design everything on the computer that you can do with like knitting machines? And then it just does it for you?Speaker 2
Yes, yes. So we use ZSK makes its own software to be able to do this because that way you have complete control over every attachment and every single piece of the machines in a very controllable way. And that way, if there's new a new attachment or a new hot air cutter or something that comes out for the machine immediately that gets plugged into the software, and it's it's ready with the next patch update. So they have a software usually for what how we run different samples, it's usually somebody brings by a DX F drawing, like a line drawing or an Adobe Illustrator drawing or some kind of vector drawing. And that plugs in natively to the software. And we can either just trace over that or fill that in and use that as our guide to be able to create the machine code that runs outs. It's a very straightforward process in that regard. It's also a lot faster if if you've done knitting, I mean, knitting you know, like especially 3d Knitting you can you can make designs that take days, if not weeks to be able to make a good design and have it run and it's a very, very in depth process. It's a very beautiful process, but you really have to know what you're doing to be able to make 3d knitted knitwear. Whereas embroidery is a lot faster to get prototypes off. It's usually just a couple of hours from concept to trying it on the machine. And then on the machines, we don't really have to spend much time configuring that's maybe 10 minutes to run a wire part and then switch over to a carbon fibre part. So that allows a lot of reconfigurability and testing to be done or different scientific tests if you're trying to test which material you want to use? Or how stiff something is, it's, it's a very good way to cycle through many, many rapid iterations quickly so that you can arrive at a good solution for your project.Speaker 1
Right, interesting. And what about sustainability, then our embroidery machines quite sustainable? Or is there something else that needs to improve? Because obviously, this is such a hot topic at the moment, isn't it?Speaker 2
I love that question. That's, I think that's an extremely important one. It's probably my favourite question. Yes. So I think, in general, as any textile manufacturer, we have to be much more conscious of sustainability, especially as we start to green the economy and, and look at production, how things are shipped? I think sustainability is an extremely complex question, too. So part of the question is like, I mean, shipping adds a lot of different weight. And whenever you ship something that makes something less green, the longer you ship it, materials, where you're getting those materials from, and how much they're getting shipped, and how there's so many different considerations that go into that. But in general, I would say embroidery is a fairly sustainable process because it falls into the range of finishing processes, textile finishing processes, and because of that, you're really only putting thread and end material exactly where you need it. And that helps with with making sure that you're creating the design and not making too much extra sustainability is one of the bigger pieces that we're using right now in carbon fibre embroidery. So if you think of if you think of that think of blast fibreglass fibres are relatively cost effective fibre, it's, I don't know exactly offhand. But I would say around $2 to euros a pound a kilogramme, somewhere inside of there. If you go to carbon fibre, well, short and carbon fibres can be $150 more per per pound or kilogramme, and so you can't waste them at all. And so sustainability has an economic impetus there to be able to say, how do I put this carbon down exactly in the pattern that I need. So I don't have any waste, because the waste is expensive. And embroidery does that beautifully. Because if I'm doing a let's just say, a weaving process, well, I have to have a warp of carbon, I have to have a weft of carbon, if anything goes wrong in there, I have to reset the entire warp beam. There's a lot of different wastes that happens inside of that process. And it takes time to embroider that. And if anything goes wrong, that also allows sets a large amount of time to fix it and get the machine back up and running. With embroidery, we don't have a warp, we don't have a web so we can embroider on sustainable plastics we can embroider on. I've done a couple embroidery on PE T sheets, which are made from recycled soda bottles. But that way, we're only putting that fibre whatever the fibre is exactly in the patterns and direction that we need. So there is there is no waste in that part. And I think that's one way that we're looking at sustainability in the embroidery industry of how do I put colour down? How do I put material down so that I'm not wasting a lot of extra fabric? I'm not wasting a lot of extra precious material. And how do I put those together into a product that we can start getting out? Locally to so there's a lot of textile manufacturing, especially in these technical textiles, that is definitely happening in the US right now. People are seeing a need to be able to do it. They don't want long shipping times from overseas, they don't want to be able to worry about tariffs, they want to be able to have a product and somebody that they can go visit, see their manufacturing for their technical textile being made in person, and then have control over quick design changes, be able to understand that everyone in the factory can communicate with them, and they can point out different things, and then have it shipped down the street and it's ready to go for the next process. And then have it gets sold online immediately. Next, and it's a 123 process locally, which I think is a very nice, some nice piece from the sustainability of shipping of textiles.Speaker 1
Yeah, I mean, it's so interesting, isn't it, how every area in the textile industry has its own ways it can make an impact. And with embroidery, it just sounds like efficiency and cutting waste are the two main things that you guys could be known for.Speaker 2
So the there's another one that I'm I keep pulling up in my mind I'm trying to see I mean, just as a as a pitch. But we have this thing of smart textiles right now that is emerging. And we know that there's no standards on it yet. Unlike traditional circuit boards, those are all standardised there's different pieces. So smart textiles are still in this ambiguous state of how do we make them what is standard? What materials do we use? Interesting to me would be if we as a society could come together and say, you know, we're kind of fusing two of the more unsustainable pieces here we're fusing electronics manufacturing, which is relatively unsustainable, and textiles manufacturing, which is also pretty unsustainable, how if we're starting to fuse these at a new point, can we do better for this? And I keep trying to go through things like putting, I don't know putting either like an RFID sequin or a tag inside of the pieces that goes to a like a government database so that you can see all of the materials that were used in that mix. In that construction, whether it's a shirt or a towel or whatnot, and that way, we can start to do textile recycling. So you could send these into a textile recycling spot. And they can just scan it and say, Oh, this is 100%, pe T. But there is a circuit board on here that has silver. So we're going to take the circuit board out because it has x value, and we'll recycle the towel. And then the next one comes through. And there's another little RFID token or some kind of serial token inside of that. And it allows these these textiles, these technical textiles or smart textiles to be linked to this database so that you know, what's recyclable, what's reusable, and then also you can see value proposition so that somebody is more likely to see that, wow, this one has 35 cents of silver thread in it on that Silver's worth 35 cents for me to reclaim, I'm going to definitely reclaim this piece. Or maybe it comes down to saying like, you know, this textile is a mixed material textile has a lot of organic has a lot of synthetic material. This doesn't look reasonable for us to melt down. But we can shred this and turn this into insulation. So I think technical embroidery and a lot of the other technical processes right now would be a way of adding that information into the textile quietly and gently so that people don't know it. But when you get to that recycling step, now suddenly we take these two very unsustainable industries and create this new industry that people can recycle those goods people can reuse those people can start to see that there is value in reclaiming it because it's been pre sorted and pre serialised. So that's that's my my hope for the future is that embroidery can be part of that process, as well as other technical textile processes to be able to look at how do we create a better system for the next generation of textile users?Speaker 1
Now Topher? Unfortunately, we are running out of time. But before I let you go, What plans does satis K and the Research and Training Centre have for the rest of this year and perhaps next year.Speaker 2
So the rest of the show we're looking, we're looking pretty heavily at a couple of different techniques and developing some new techniques so that we can start to look at other additive manufacturing processes. We're looking at some new types of wire embroidery, being able to twist some wires on the machines, which is exciting, because that allows you to do custom wire production on the machine, we're looking at some interesting thermal shaping applications, a lot in the camera space to be able to do different camera, camera sensitivity. One of the big ones, too, is looking at data off the machines. So as we go to this industry 4.0 and everything becomes digitalized, we start to look at that in machines, too. So we start to be able to network all of the machines into a network. And that way you can watch your entire production floor and watch every single head on every single machine at once. And start to look that maybe this needle over here is slightly not sharp, we have to replace this needle or maybe this, this thread over here might not be the correct thread because we're getting more thread breaks, that's that's good, change that thread. And that allows you to digitally watch everything that's happening and have a higher work thread flow, also allowing you to be able to see different efficiencies on the machine, which further reduces cost and further helps with quality as well. So there's a lot of push towards that and having user interfaces. And I think that the last one I'm really, really looking at is how to be able to create online courses to be able to teach some of this because, as you mentioned, Utah out in Germany is a fantastic school to learn about textiles. But in the US there's there's pretty much two schools left that do it North Carolina and Jefferson. And so how do we start to teach some of these corporate partners who might not be able to go out to those schools, about technical textiles and what solutions they can provide and how they can help save cost in different different industry segments. So I'm looking at different teaching tools and methods to be able to do that, including online courses and whatnot. So I'd say those are my kind of focuses for the next year. And onward from that. It's always what kind of technical problems do people come up with that we can try to figure out new solutions for it and how can we make that fit in their in their workflow?Speaker 1
Well, it sounds like you're going to be very busy. Definitely. Yeah, well, I mean, as I said, Topher that's all we have time for today, unfortunately, but thank you so much for joining me on the podcast today. It's been great to learn more about embroidery and all the work that you're doing it said SK so thank you.Speaker 2
Thank you for having me. Jessica's absolutely wonderful to chat with you.
Have your say. Tweet and follow us @WTiNcomment