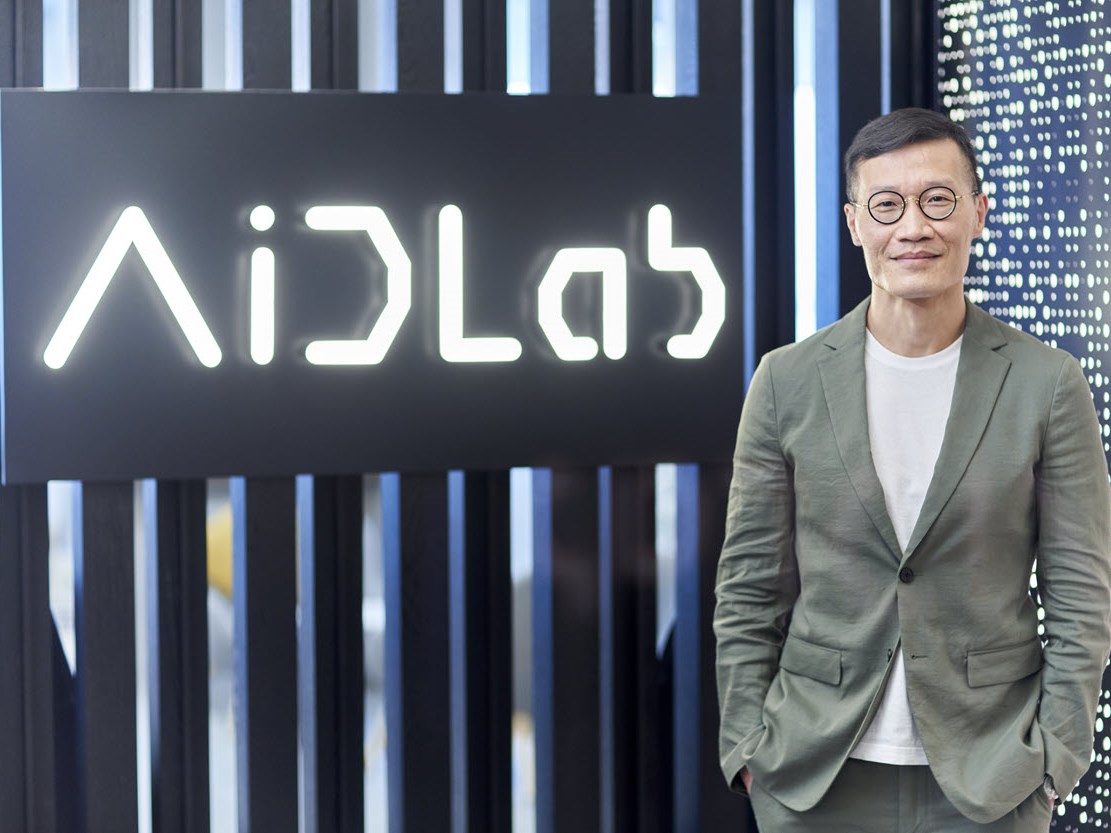
An AI-powered, intelligent quality control technology for weaving has been developed by the CEO of the Laboratory for Artificial Intelligence in Design (AiDLab). Otis Robinson reports.
Textile & apparel manufacturers are eager to automate the fabric inspection process, notes professor Calvin Wong, professor in fashion at the Hong Kong Polytechnic University and CEO of the Laboratory for Artificial Intelligence in Design (AiDLab).
Wong highlights that the textile & apparel value chain is complex and requires multiple inspection checkpoints. Many of these quality control checks are performed manually, which requires the hiring and training of highly skilled quality inspectors. Skills needed include the precise identification of defects in textiles and how to grade or classify such defects. But Wong suggests even this is not nearly thorough or reliable enough.
The process is overwhelmed by its labour-intensive nature and human inefficiencies. In fact, Wong claims this leads to a meagre 70% accuracy rate and many undetected defected textiles will end up downstream, ready for the garment creation process.
Consequently, the AiDLab CEO has seen manufacturer demand for smart, digital alternatives rise. He says this bottleneck has also created a “high propensity to attract artificial intelligence (AI) companies [who wish] to create solutions for many industry challenges.” Standing alongside a handful of automated quality control systems already available on the market, AiDLab has developed its own solution, the WiseEye.
Powerful tools
The WiseEye is an AI-based intelligent fabric defect detection system that utilises AI, big data and deep learning technologies.
The system currently exists in two models – the WiseEye 1 and WiseEye 2 – and is mainly for woven fabric inspection. WiseEye 1 can be integrated into weaving looms to detect “up to 40 common fabric defects,” says Wong, and is claimed to achieve over 90% accuracy for woven fabrics with solid colours and around 80% for striped patterns. The hardware includes a high-powered LED light bar that illuminates fabric and a high-resolution charge-coupled device camera that is mounted on a rail to capture images of the whole width of the fabric during the weaving process. Behind the scenes, these images are fed into an AI-based machine vision algorithm to detect defects.
WiseEye 2 extends this technology from the weaving machine to act as a standalone machine for inspecting both finished woven and knitted fabrics. This second version can detect defects in high-speed environments – a rate of over 60 metres of fabric per minute, Wong claims.
The WiseEye project entered development in 2015.
Wong says: “At that time, I had done a lot of fundamental research on image processing, pattern recognition and computer vision-related research – which perfectly match the core techniques for fabric defect detection. I decided to develop something that can really help the industry.”
Its technologies – AI, big data and deep learning – are the fundamental backbone of the solution and run parallel to one another.
Wong explains: “The WiseEye system mainly adopts two sets of algorithms. The first one is the AI-based computer vision algorithm, while another set of algorithms are a deep learning network.”
The deep learning network is trained with large scale image data sets. Over the past few years, the AiDLab team has collected images of fabrics with defects – captured by an industrial high-resolution camera during the manufacturing process – which were subjected to image pre-processing, feature extraction and defect detection. This was then fed into the AI-based computer vision algorithm to train itself.
From this information, the WiseEye solution can be integrated into the manufacturing line to detect faults and defect locations in real-time and generate analytical information and alerts as needed.
Wong adds that “deep learning networks are a very powerful tool and can really enhance the [efficacy] of detection accuracy.” Wong refers to how WiseEye has been trained to detect defects at exceptionally high accuracy – including a resolution of up to 0.1mm.pixel.
Recognition of the WiseEye’s technical feats were awarded to Wong in 2019. WiseEye won two Grand Awards at the 47th International Exhibition of Inventions in Geneva, Switzerland.
Absence in market
Ultimately, the textile & apparel industry is no stranger to automated quality control. In March 2021, WTiN Textile 4.0 spoke with Uster about its Quantum 4.0 sensor technologies and their ability to enable intelligent quality control for yarn production. But, although automated fabric inspection is a longstanding research topic and solutions exist in the market, the process remains riddled with challenges, says Wong.
He notes that most high-performance weaving machines cannot guarantee the production of defect-free fabrics all the time. As such, automatic fabric inspection technologies that can reach industrial requirements are still required – if not absent – in the market, he adds. Thus, WiseEye was developed to answer this specific gap.
Wong explains: “The reason WiseEye is a technological breakthrough is [related to] the fabric. We know it’s very complicated: the structure is very complicated, there are many fabric structures and variations in terms of texture and types. This makes defect detection very challenging, [especially for] algorithm design and development.”
He continues: “Currently, the detection capability of WiseEye covers quite a number of common types of fabrics. For example, for woven fabric we can [work] on plain structures, twill structures and some kinds of simple dobbie structures. For knitted fabrics, we can [work] on single jersey, double jersey and more. Our algorithms can also cover different types of colour and patterns, such as the solid colour checked pattern or striped patterns. That’s why we call this a technological breakthrough.”
Expansion
The first trial conducted – tested in a manufacturing environment for more than six months – achieved a 90% reduction in loss and wastage due to faulty textiles, Wong claims. Thus, allowing “considerable savings and enhancing production efficiency.”
It’s clear that the use of smart solutions such as WiseEye has an impact beyond an increase in production quality, accuracy and efficiency. In April 2021, global initiative Fashion for Good selected WiseEye as one of its 10 new innovators in its South Asia Innovation Programme, highlighting its supposed ability to reduce loss and wastage by 90% – thus helping to improve the sustainability of the industry.
Wong notes that this support is helping to drive commercialisation of the WiseEye: “At the moment, we are collaborating with six textile & apparel manufacturing companies to trial the WiseEye 2, which is now at the final stage of internal testing.”
Alongside on-the-ground trials of the technology, the AiDLab team will continue R&D on the technology.
Wong concludes: “We are exploring how to extend our existing WiseEye 2 algorithms from fabric [defect] detection to leather material inspection, like shoes and handbags etc.”
For more information, visit www.aidlab.hk/en.
Have your say. Join the conversation and follow us on LinkedIn