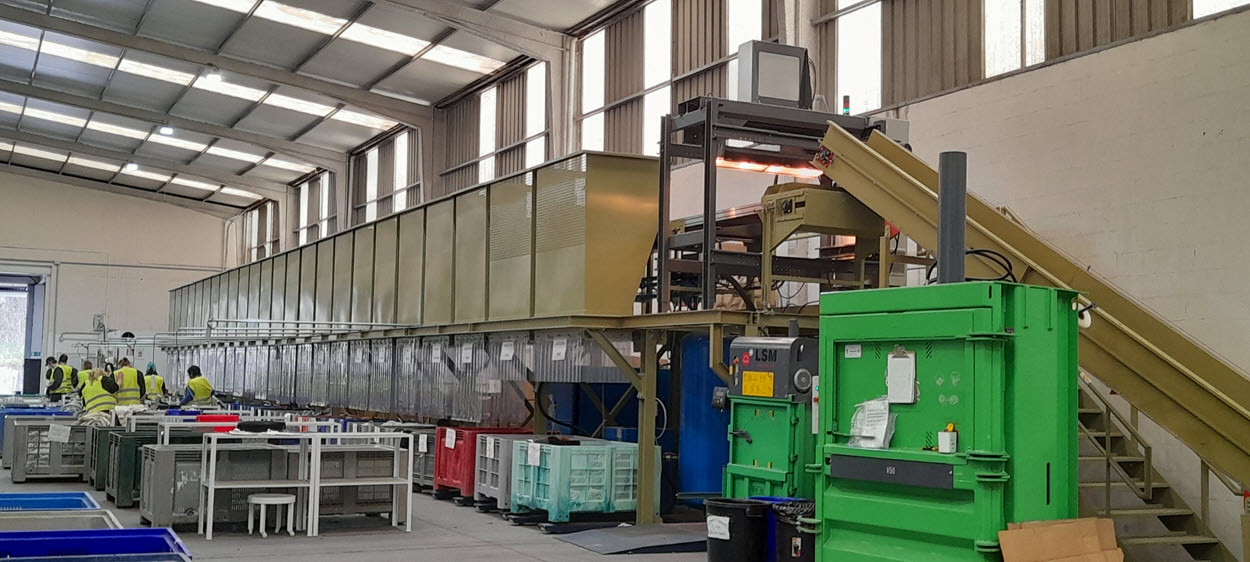
Silvia Gregorini, head of robotics at Picvisa, talks to Jessica Owen about the company’s automated optical textile sorting technology to enable a circular economy.
Accurately sorting textiles to promote widescale recycling still remains one of the biggest pain points in the textile & apparel industry. While there are a handful of companies now either piloting or operating sorting plants, the amount of textile waste that is coming through the system means significant additional support is required.
One company that has decided to throw its hat into the ring is Picvisa. Founded in 2000 and based in Barcelona (Spain), the company originally specialised in sorting technologies for glass and plastics but has now diversified into textiles.
Silvia Gregorini, head of robotics, Picvisa, says: “We allocated a budget to develop a textile sorting solution around seven years ago because of the large quantity of textiles ending up in waste management plants.”
She adds: “The market was not ready for that at the time, but we thought it was an important line to investigate. Now there is a clear demand from the market and so we are happy that things have changed.”
Unlike other textile sorters that usually focus on implementing one technology, Picvisa combines two types of optical technologies with artificial intelligence (AI). According to Gregorini, this combination makes for a more accurate and sophisticated sorting process.
The first step in the process is classification. To do this, Picvisa utilises near infrared (NIR) cameras to detect and determine material composition, as well as red-green-blue (RGB) cameras to determine colour, shape and texture information about the garment. This information is then combined with deep learning algorithms to decide which category the garment should be sorted into – information that the software continually learns from to improve accuracy as time goes on.
The second part of the system concerns physically moving the garment into a specific pile. To do this, Picvisa uses a conveyor belt to move the textiles along, and either high-pressure air valves or robots to sort the garments once they have a category assigned to them.
In order to visualise how this works in reality, Gregorini notes a plant that it has installed at Coleo Recycling – a recycling facility based in Galicia (Spain). She says: “First, the garments are placed onto a conveyor belt, where they pass under the NIR and RGB cameras. The cameras then detect the unclassified textile and send the information to the sorting system.”
She adds: “For this system, the company identified 24 different categories or materials and blends. The 24 boxes are lined up along one side and air valves sit on the opposite side. When the textile reaches the right spot on the conveyor belt, the valve detects this and blows air to push the garment into the right box.”
David Puyuelo, director of Coleo Recycling, says the facility can now process 5,000 tons of collected industrial and domestic material per year due to the installation of Picvisa’s technology. And in addition to solving the problem of the classification, Puyuelo says Picvisa's technology represents an important advance in implementing the traceability of textile waste – something that is going to be essential before the arrival of the new legislation.
While Coleo Recycling opted to sort textiles into 24 categories, Gregorini says that does not have to be the case for everyone. In fact, she says the company prides itself on providing customised solutions. She says customers need only sit with the Picvisa team to determine the categories they would like to include – most of which have sorting accuracy rates of above 95%.
Picvisa can also offer the entire system or just sections of it. And extras – such as a loop conveyor belt to recirculate garments that did not get classified and sorted the first time – can also be integrated.
Coleo Recycling, a recycler, is just one of three main target markets for Picvisa. The other two are waste management plants and retail brands. She says: “Waste management corporations are big companies that see the large quantities of textile waste entering their process, and this type of customer wants to start extracting the waste.”
As for the brands, she adds: “They are joining together to find a solution to their own pre- and post-consumer waste in order to give them a second change. Maybe they could reuse the garments or create new fabrics from them.”
The main reason for the lack of textile sorting companies that currently exist has been the lack of sophisticated technology. Although another reason is the cost of installing these facilities. That’s why Picvisa has built its systems to be relatively affordable. Indeed, Gregorini believes the business model that the company has devised is something that could be rolled out across Europe in the near future.
To help this plan come to fruition, Picvisa has been selected for this year’s Fashion for Good 2022 Asia Innovation Programme. Over the coming year, Gregorini says the company wants to use this opportunity to learn more about the textile & apparel value chain, talk to different stakeholders about their sorting and recycling requirements and build a prototype system.
Gregorini concludes: “We have deep knowledge of how to use our technology for automatic sorting and we aim to use that knowledge to make the textile industry circular.”
Have your say. Tweet and follow us @WTiNcomment