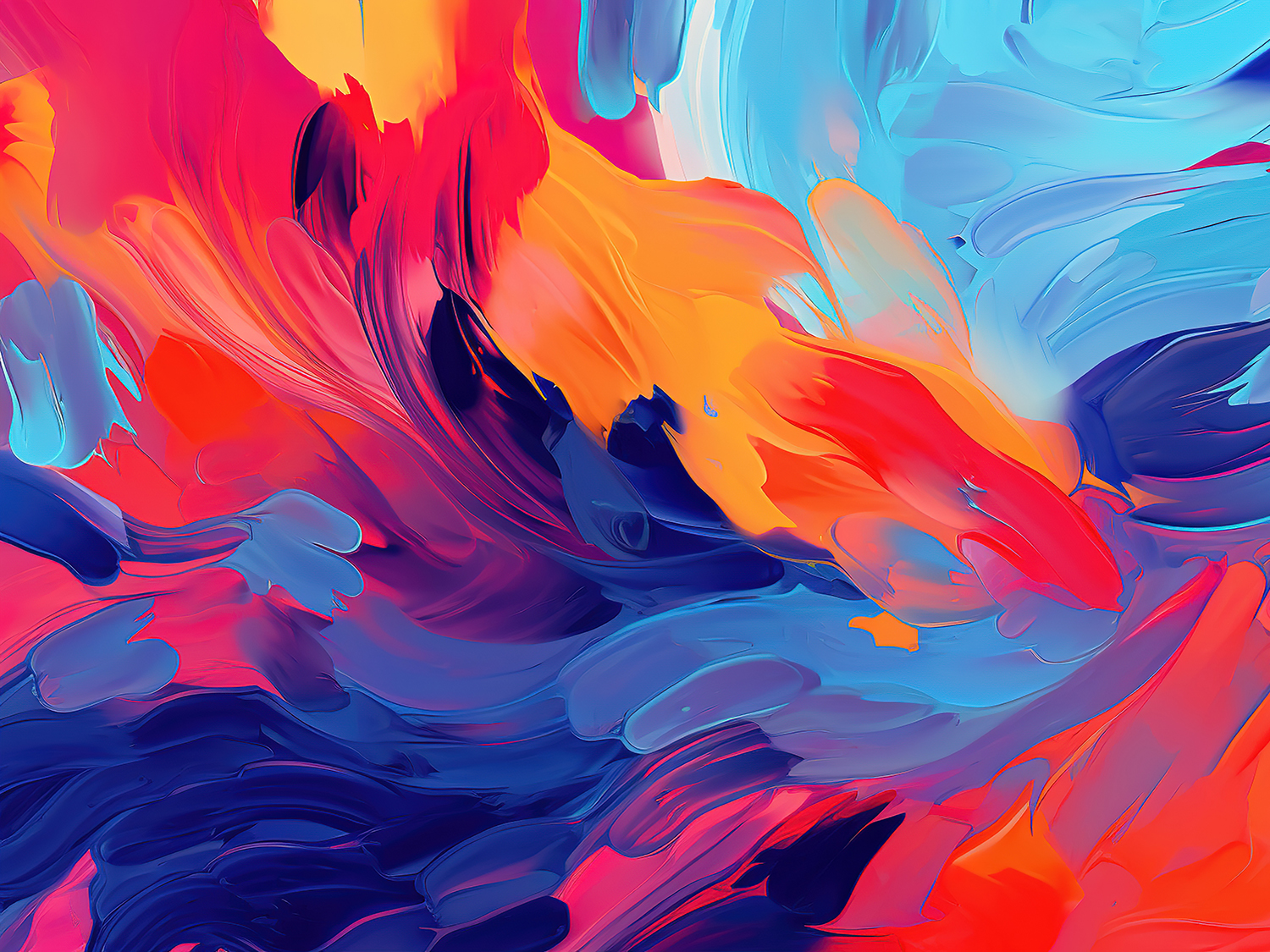
Garment printing expert Dmitry Sarbaev examines the strengths and weaknesses of hybrid printers and why they are enjoying high growth in manufacturing hubs around the world.
- Contents
-
Understanding the commercial readiness scale
WTiN’s Commercial Readiness Scale gives an indication of what stage of commercialisation a product is at. It ranges from Emerging: a research stage development; Scaling: the product is being produced on a small but growing scale, and Commercialised: the product is well-established and ready to purchase.
Summary
- Hybrid printing systems are helping print service providers (PSPs) meet the demands of the fast-paced world of garment decoration.
- The printers offer affordability and high productivity and are therefore becoming popular in manufacturing countries.
- There are multiple hybrid solutions on offer that suit the needs of a wide variety of PSPs.
Introduction
ITMA 2023 in Milan and ITMA Asia + CITME in Shanghai were significant trade shows for the digital textile printing market this year. Both events showcased a host of new innovative textile printing solutions, and many of these targeted the rapidly evolving garment decoration sector.
Printer manufacturers are focused on catering to the emerging global trend that is personalisation. It is exciting to observe how mid-to-large scale businesses in countries with mass production markets are undergoing a digital transformation and adopting new technologies to stay relevant.
One of the challenges that engineers, businessmen and decorators face is raising the efficiency and competitiveness of existing print production facilities while embracing new business models, reducing costs, and shortening production runs. Deploying hybrid printing systems can help print service providers (PSPs) face new realities in the fast-paced world of garment decoration.
What is a hybrid system?
A hybrid printing system combines screen printing and digital direct-to-garment (DTG) printing in different sequences and combinations. The setup usually includes a screen-printing unit and a digital printer that operate synchronously to apply artwork onto garments or cut panels. The hybrid system can be an all-in-one standalone machine or an add-on where a digital printer is integrated with a screen printer. These systems offer high-speed, full-colour printing, and excellent quality and cost per print.
Accelerating growth
Hybrid systems have been in development since the mid-2010s to meet the demand from global brands for durable, full-colour prints at affordable price points. These systems aim to combine the advantages of screen printing with the creative potential of digital printing, allowing designers to unleash their creativity. The goal is to provide high-quality prints that are cost-effective and meet the requirements of global brands.
It is well-known that the cost of white ink has been a challenge in the DTG industry. The volume of white ink jetted down in digital printing is typically three to four times higher on average than that of colour inks, leading to higher costs than other decoration methods. As a result, DTG has found its main niche in on-demand printing, where the ability to print “one-off" garments allows for custom retail-level sales and effortlessly covers all the costs for the premium type of print application.
However, when it comes to mass production printing, DTG has struggled to compete on cost per print. Despite increasing the speed of DTG printers over the years and the ability to work with the wide colour gamut using CMYK + spot colours, screen printing has remained the preferred choice, even though this preference limits the number of colours that can be used in artwork development.
The logical response to address the cost challenges was the development of a “hybrid” system that eliminates the need for “digital” white ink and utilises screen printing technology to apply white paste through the screen. By skillfully combining the coverage and density of screen-printing inks, this approach can significantly reduce costs associated with the white underbase by up to 70-80%. Additionally, the cost of the colour layer doesn’t contribute significantly to the overall cost per print due to the very low consumption when printing a full-colour layer. Therefore, this hybrid approach enables significant cost savings while maintaining high-quality full-colour prints.
In addition, pre-treatment spray is an inevitable step in classic DTG technology, and the pre-treated area is often larger than the actual print area. This can cause various production issues, such as colour staining over heat application, dull prints due to insufficient spraying and poor washability because of over or under application of pre-treatment. However, hybrid systems rely on the screen-printed base, which allows decorators to avoid the use of a pre-treatment layer in the most common scenario of their operation. This approach enables consistent output of the same image in large volumes, without the variability and potential issues associated with pre-treatment spray.
Hybrid printing in mass production countries
Consistency, quality, wash fastness and colour-fastness have always been key requirements in large-scale screen-printing facilities. The rise of direct-to-film (DTF) technology has put more pressure on the DTG market, driving further the need for cost-effective industrial printing solutions. Combining the benefits of DTG with screen printing in hybrid systems has become a natural choice to meet buyers’ high-quality expectations while keeping costs low.
Countries such as Vietnam, China, Bangladesh, India, Turkey, Uzbekistan and others are known for their significant numbers of screen-printing machine installations. By upgrading their existing setups with hybrid digital printers integrated with oval presses, businesses can seamlessly incorporate digital DTG printing into their print production processes. This integration provides decorators with the opportunity to expand their applications and compete by accepting artworks for printing with no limitations on colours.
Types of hybrid systems: pros and cons
When it comes to the combination of screen and digital DTG printing in a hybrid system, there are three major types available. Each of them has certain advantages that stand out, as well as weaknesses that limit their application.
1. All-in-one unit
The all-in-one unit is a standalone printer that integrates both a screen-printing station and a digital printing station, along with a flash curing system. It is typically controlled from a single user interface, which allows the operator to set screen-printing settings, such as the number of strokes, speed, drying after the underbase, and other parameters that subsequently determine the settings for digital printing.
The carriage of the printer is equipped with print heads that fire colour inks. Additionally, white ink print heads can be utilised, providing the operator with a selection of options to choose from: screen-printed white or DTG-printed white ink. This versatility allows for flexibility in achieving the desired print results based on the specific requirements of each job.
Pros
The all-in-one system offers several advantages over traditional oval press-based setups. One major benefit is the space-saving design. In many instances, factories have limited space, but the compact nature of the all-in-one system allows it to operate efficiently in small areas. This is particularly beneficial for businesses where space is a commodity.
The all-in-one system also has an easy registration mechanism, which is typically controlled from a digital display, which means quick adjustments can be easily made to ensure precise alignment between layers. This helps prevent misalignment issues that can occur in oval press-based setups and, therefore, offers fast seamless print production. Since both the screen printing and digital printing stations are integrated into a single sturdy frame, the installation process for these units is simplified.
Overall, the all-in-one system provides the benefits of space efficiency and easy installation, making it an attractive option for businesses with limited space and a need for reduced maintenance.
Cons
The major weakness of the all-in-one system is the single screen availability. For each pallet there is only one screen that can be used in conjunction with digital printing. This limits the operator to a combination of these options:
- screen printed white layer and digitally printed colour layer.
- digitally printed white-and-colour layers with screen-printed special effects (such as glitter, glow in the dark, etc.)
- screen-printed pre-treatment emulsion and digitally printed white-and-colour layers.
While these combinations offer flexibility for printing on various types of substrates – not just natural fibres which pure DTG systems are typically built for – the system is still limited in terms of delivering either the durability of the print or the cost benefits of the white underbase, which are primary advantages of combined screen and DTG printing.
Moreover, the single screen availability forces the operator to use an enhanced number of strokes when applying the ink via the screen. This affects the speed of output compared with oval setups, which can be a significant disadvantage for businesses with a high volume of orders.
2. Oval screen-printing press and digital DTG printer
A hybrid system of this type comprises an independent elliptical screen-printing machine with a variable number of pallets, depending on the requirements for the complexity of the print and the desired output speed. Typically, the number of pallets ranges from 24 to more than 50 to accommodate most requirements. A digital DTG printer is installed over one of the pallets of the oval press to print the full-colour image.
Pros
This hybrid system offers several benefits over the all-in-one unit. The independent screen-printing machine enables multiple screens to be used, so the operator can deliver more sophisticated prints with multiple layers.
Hybrid systems of this nature are capable of handling complex tasks. The inclusion of multiple printing stations before and after the digital DTG printer offers several advantages:
- Printing on a variety of fabrics. These hybrid systems can effectively print on various types of fabrics, including those of poor quality. This allows for greater versatility in catering to different customer demands.
- Avoiding dye migration on polyester. By incorporating antimigration blockers prior to screen-printing the white base, these systems can prevent dye migration on polyester fabrics. This ensures that the prints maintain their vibrant colours without any bleeding or smudging.
- Better control over the handfeel. The combination of multiple layers of screen-printed white paste and digital printing in a hybrid system allows for better control over the tactile properties of the final product. This means that operators can adjust the handfeel of the printed designs to meet specific requirements.
- Improved colour-fastness and washfastness. Hybrid systems can enhance the durability of prints by applying a topcoat. This improves colour fastness and washfastness, ensuring that the prints meet recognised standards and maintain their quality, even after repeated washing.
In addition, the increased number of pallets in these hybrid systems enables operators to reduce the number of strokes per pallet. This enables faster production speeds and therefore increases overall efficiency and output.
Cons
The installation process of this type of hybrid system, which consists of several independent pieces of equipment from different OEMs, can be more time-consuming and requires specific skills. The installation process involves tasks such as precise levelling of all machines’ surfaces to maintain product quality and prevent downtime. Alignment procedures need to be carefully executed to ensure perfect registration between layers and the sharpness of the printed image. Moreover, integrating the printer engine with the screen-printing program logic may require additional effort, especially if the machines are supplied by different manufacturers.
Another potential disadvantage of this hybrid system is the requirement for a large space when installing presses with dozens of pallets. The need for a significant amount of space can pose challenges for businesses with limited floor space.
Despite these hurdles, the benefits of the oval screen-printing press and digital DTG printer system, including its ability to handle complex tasks and deliver durable prints, often outweigh the installation complexities and space requirements.
Oval setup for mass customisation
The increased demand for personalisation and on-demand printing has driven the evolution of hybrid systems into almost automatic mass customisation printing solutions. They eliminate the need for screen making and allow decorators to print directly on ready-to-wear blank garments using customer-provided artworks. This enables the production of finished products with a short lead time, meeting the market’s demand for a quick turnaround.
In this set-up, the flexibility of the hybrid system allows for both white ink jetting via the print heads and for a white paste to be screen printed, depending on the immediate production needs. This versatility ensures that decorators can adapt to different requirements and achieve the desired results.
For a digital add-on over the oval screen-printing machine, there are multiple options to consider:
- Two sequentially located digital printers. This setup enables simultaneous printing of white ink and colour inks by different machines, enabling efficient and synchronised production.
- Single digital printer jetting both white and colour ink. This option consolidates the printing process into a single machine, reducing equipment requirements.
Furthermore, the hybrid solution can integrate additional machinery to process the application of pre-treatment liquid, perform surface cure, and apply heat pressing to the garments. This streamlines the production process and creates an intelligent and flexible system.
Adopting such hybrid solutions not only enables on-demand printing but also contributes to reducing the environmental footprint. By eliminating screen making and optimising production processes, these systems minimise waste and energy consumption, making them more sustainable options for garment decorators.
What’s next?
The evolution of hybrid screen-printing and digital DTG printing systems will continue to progress, with a focus on software solutions that integrate these in-line systems into the ecommerce space. Efforts will be made to enhance the speed and automation of these systems, making them highly efficient and streamlined. By implementing advanced robotics and machine learning algorithms, these systems will become almost fully automated, thus minimising manual intervention and maximising production speed.
Key takeaways
- The all-in-one standalone hybrid printer is typically controlled from a single user interface, allowing the operator to set screen-printing settings, and other parameters that subsequently determine the settings for digital printing.
- The all-in-one system provides the benefits of space efficiency and easy installation, making it an attractive option for businesses with limited space and a need for reduced maintenance.
- An oval screen-printing press and digital DTG printer means that multiple screens can be used, enabling the operator to deliver more sophisticated prints with multiple layers. The system also allows for faster productivity.
- The increased demand for personalisation and on-demand printing has driven the evolution of hybrid systems into almost automatic mass customisation printing solutions.
- The oval setup for mass customisation can integrate additional machinery to process the application of pre-treatment liquid, perform surface cure, and apply heat pressing to the garments.
- Adopting an oval setup not only enables on-demand printing, but it also promotes sustainability.