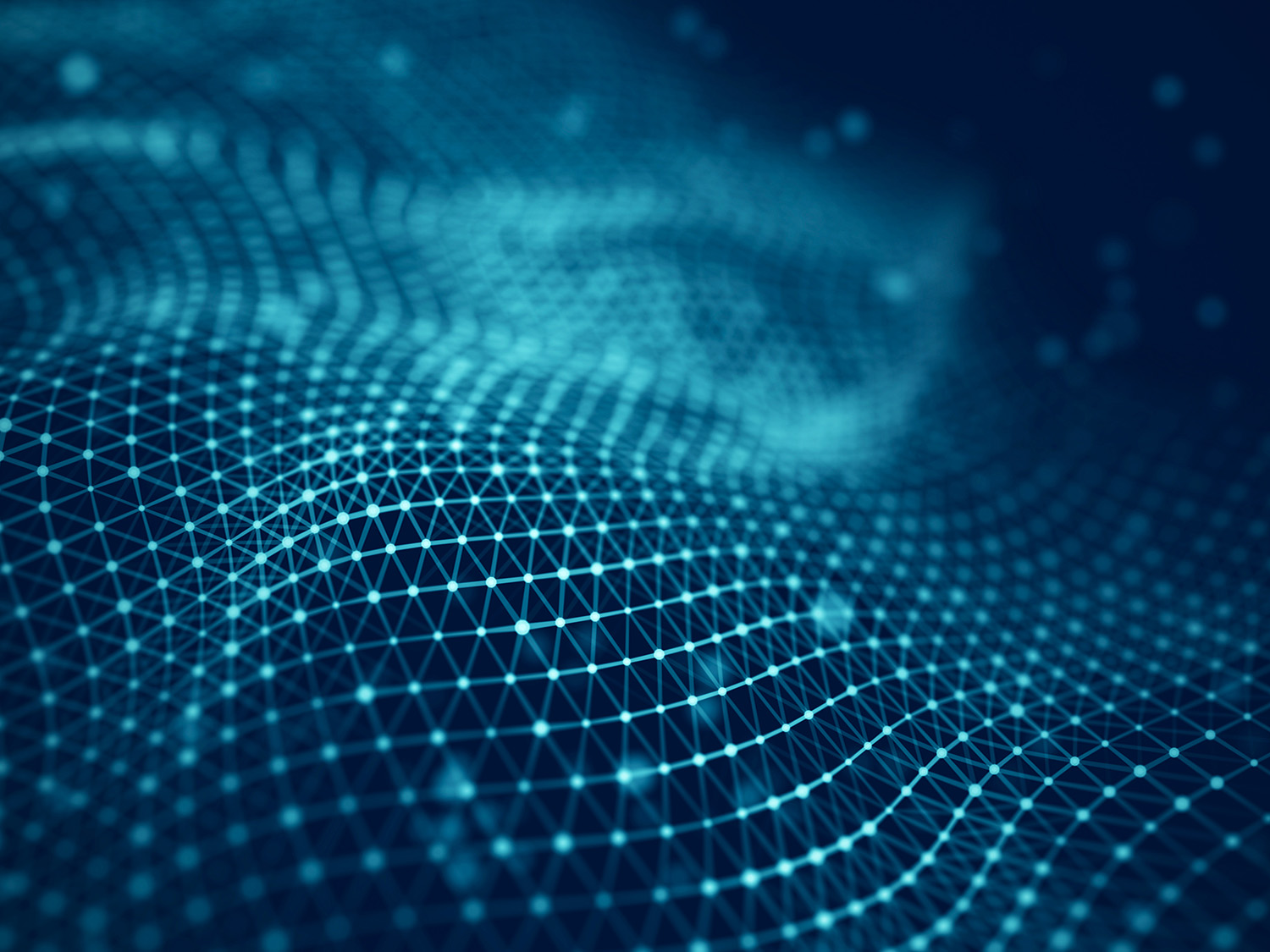
This month, the Textile Innovation podcast speaks with Ishan Chathuranga – an e-textiles engineer based in Ontario, Canada, about standardisations, and issues and solutions within e-textiles.
E-textiles are a rapidly expanding part of the textile industry. Also known as electronic textiles or smart textiles, e-textiles are fabrics or garments that incorporate electronic components and technologies. They can include features like sensors, actuators, conductive fibers, and microcontrollers, allowing them to sense and respond to their environment.
For episode 92 of Textile Innovation, we speak to Ishan Chathuranga – an e-textiles engineer based in Ontario, Canada. Chathuranga has more than eight years’ experience in electronic textile product development, failure analysis, and manufacturing.
Chathuranga goes into the challenges the market currently faces that prevents smart textile products from being scaled and commercialised, how a smart textile can be commercialised at scale and how plug-and-play technology can really propel the industry forward.
If you’d like to get in touch with Chathuranga, you can find him on LinkedIn or head to etextilewearables.com.
You can listen to the episode above, or via Spotify and Apple Podcasts. To discuss any of our topics, get in touch by following @wtincomment and @rubyatwtin on Twitter or email rpenson@wtin.com directly. To explore sponsorship opportunities, please email sales@wtin.com.
-
Transcript
This transcription has been AI generated and therefore may have some inaccuracies.
Ep. 92: Standardisation can propel e-textiles
This month, the Textile Innovation podcast speaks with Ishan Chathuranga – an e-textiles engineer based in Ontario, Canada, about standardisations, and issues and solutions within e-textiles.
WTiN
Hello and welcome to textile innovation hosted by WTiN. My name is Ruby and I'm the news editor and your podcast host. Each month we're going to be joined by a brand new special guest. So join me and my colleagues as we deep dive into what's new, what's interesting and what unmissable innovations have hit the market recently, we cover everything on the podcast from sustainability to startups and the latest research developments. And we also quiz the experts in the fields about their new products and ideas across a huge spectrum that is the textiles industry. So no matter what your interest is WTiN and have you covered. And we can connect you to everything you need to know right here from our central hub in the UK. Today, we are talking to a Ishan Chathuranga and E textile engineer based out of Ontario, Canada with over eight years of experience in electronic textile production, development, failure analysis and manufacturing. Ishaan talks to us today about the issues with scaling e textiles, the stages of development and the need for plug and play technology and standardisation within the industry. Hi, okay. Hi. Before we get into the technical side of things, do you want to give us a bit of background on yourself? Tell us about you and your history within textiles at this point.Ishan Chathuranga
So my educational background is in basically textiles engineering, I also have studied electronics engineering. In my career, I have worked as a tech lead in one of the largest electric electronic textiles manufacturing company as a tech lead for almost five years. And then I joined academia and I worked at UNICEF category for most three years working on wearable tech research projects currently also volunteering on working in IPC as an 18 member thing on a textile standards. At the same time, I'm working on one in one of my own companies called the textiles and wearables, where we consult a textile startups and work with them on product development and manufacturing.WTiN
Amazing. Thank you for that. We'll get into the technical side of things. Now, why don't you start by giving us an overview of some of the challenges in general that the market faces that prevents smart textile products from being scaled and commercialised?Ishan Chathuranga
Sure, I would say there, there are a number of challenges out there. And some of those challenges are unique to each product category and use cases. So the first one how complex the manufacturing and integration process you need excels when it comes to manufacturing of the textiles. The biggest hurdle is that the team members who are manufacturing, the product needs to have a good knowledge in electronics and textiles, which is not common, because if you take a normal textile manufacturing assembly line, so those people are really specialised in in garment construction, and like textile manufacturing techniques, but they don't have knowledge in electronics. At the same time, if you take an electronic assembly line, they don't have any knowledge about how textiles work, what happens is that unlike when prototyping of a textiles it when we try to manufacture those, we would have to use those assembly lines, we don't have the comfort of doing a manufacturing process. At the laboratory level where people who are working on textiles can talk with people in electronics, and they can work together to solve the challenges in manufacturing, we have to make our electronics in a separate assembly line and made textiles in a separate assembly line, then what happens is that if something happens in the electronic manufacturing line, which will affect the textile part of the product, it's going to make a failure. The same thing gonna happen. If something happens in the tech Sherman fishing line, which can affect the electronics, then again, they are going to it's going to be fair, if I take an example to describe this, just imagine if we are making a heated jacket. So one of the ways to manufacture such product is we're going to make the textile part of it in a textile assembly line or a garment assembly line. And we're going to make the the old electronics that we need for those heating elements in an electronic assembly line somewhere in the manufacturing process, we're going to bring those two together and compete the product, we have to have a pocket or something to place our power cells and there should be a place to place our heating elements. So just imagine, for some reason when they're making the electronic part they made the electronic part with shoulder length of conductive pathway then it's required. So when we bring that element and attach it to the jacket, it will have a huge impact on the stability of the jacket and and the overall feet. So like controlling those stuff is really hard. And when you try to scale it up, we comes so complex, there can be some other challenges as well, such as, when you're making a textile product to sell Worldwide, there can be safety challenges, because different regions has different state safety standards. And sometimes the technology using the textiles can be challenging itself, because some technologies like inherently not capable of scaling up. Yeah, I think those are the biggest challenges out there. When we try to scale up any textile products.WTiN
One of the challenges that you've mentioned is designing a smart textile product that meets a consumer need. If a brand manages to create a durable and functional product that meets the requirements, does this then imply that it is scalable?Ishan Chathuranga
Not necessarily most of the times, it's not because to understand this, I think we first should understand what the the product development process of any textile, again this can have many variants, but what usually happens is when we have an idea, we break it into three main stages. So at the beginning, we try to we call that the engineering stage. So at this stage, we try to make a prototype actually all the functionalities that we need, and then we go into more designs stage and at the stage, we try to design our final prototype to into the final product with all the durability requirements, and then only clumps comes the production stage. So at the production stage, we have to think of things like how to reduce the cost how to how to maintain the quality and how to do continuous improvements and stuff. Just making a product in a way that it achieves all the functionality requirements and durability does not imply that it's scalable most of the times it's not some for some specific product it's can be but most of the times in a textiles it's not.WTiN
How do we develop a smart textile product that can be produced at scale then?Ishan Chathuranga
One problem we are having in EDF sauce industry right now is different companies try to approach some problems in different ways. Sometimes if we had some coordination and if we had some communication between those sectors, it might improve the quality of the products in overall. So if we have standards, what will happen is that most of the things different companies do would be will become standardised. So it will prevent like reinventing the wheel again and again. I mean, reinventing the wheel wheel is not a bad thing, if it's like giving you a huge benefit. But if you have standards, I think it will improve the quality of the the industry itself, because it has it has happened in many industries before such as textiles and electronics. So when when things become standard, obviously the quality becomes higher. So to understand how to develop a product that can be scalable, I think first we need to understand there are a few main differences in the prototyping stages and manufacturing stages. One is at the prototyping stage, we have a small team, where one person will be looking into common design and another will be looking into the garment construction. And there will be person to look into quality and there will be person to look into electronics. So those people can work together in a lab to overcome the challenges and make the prototypes and samples. The other thing is that cost is not a huge thing. At the prototyping stage time it takes to make a sample or prototype is also not a huge thing. But it's not the same when it comes to manufacturing. At a manufacturing stage, we had to break up products into really small parts, ask different team members to manufacture those specific parts and at the at some at the manufacturing, we have to bring those together to complete the product. So if something happens, if something goes wrong at one stage of of the manufacturing process, it's really hard to correct it unlike in a laboratory environment. The other thing is unlike in prototyping stages, cost is a big concern. And time to manufacture product is a big concern because when it takes lots of time, it can be one or two extra minutes it will improve the cost of manufacturing. So how to overcome those deaths. It's a complex problem to solve in textiles, how to convert a product into manufacturable product. But there are some some standards things that we have to do and not the same for all the products. But most of the times we have to thinking Think of ways how to break your product into separate pieces, how those pieces can be made separately in as in an assembly line, and how we can break those stuff together to complete the product. Sometimes, for some products, we even would have to redesign the construction of the whole product to achieve this, and, and one other thing most of the companies do is that they try to manufacture their electronics separately, and they manufacture their textiles separately, and bring those two together. This is also not that easy to do, because when we making our prototypes, we never focus on doing such a thing. Because in prototyping, we do have electronics and textile like garment construction at the same time. And we are just focused on achieving the functionalities of the product. But when it comes to manufacturing, we need, we get the challenge to preserve the functionality of the product at the same time, divide the manufacturing into two separate categories, and oh pathways where one team would be developing electronics and one team would be developing textiles and at the end, it will be brought together to make the completed product. And also we would have to come up with an in depth testing plan. So we need to plan how to test the product randomly while it's being manufactured. And we would have to manufacture testing weeks where the manufacturing team members can use without any technical knowledge. And there should be craned some special teams to take care of the most critical parts of the product. Overall, testing becomes a huge part. When we are we're trying to scale any textile product. In addition to that, we have to do things like finding extra suppliers for all the elements of the product because unlike in a lab laboratory environment, when we when you start a manufacturing process, you have to continue with you can't stop it in Midways, because it's going to cost a lot. So you have to find alternative suppliers and you have to train your manufacturing team members. So to bring the failures down, even sometimes you have, you'd have to look into more cost effective technologies to achieve the same functionalities of your product. Those are some key points that that's good to follow when converting any textile product into a scalable product. But again, in E textiles, most of those stuff are unique to the product and the specific use cases.WTiN
Okay, so in your experience, what would you say is the most difficult stage of development? Is it making a product durable and functional? Or is it making it scalable?Ishan Chathuranga
I would say both because if we don't do the early product development stages correctly, obviously there will be no product to convert into manufacturable stage. In my experience, I would say most of the times once you fix the problems you have at the product development stage, you will identify that making it scalable is a much harder challenge because you have to think of the cost aspects. And the other problems that that can come in manufacturing stages. But I would say both stages are really important. But most of the times scaling up is far more difficult than the prototyping stages.WTiN
Do you think that having interoperable plug and play components would help brands scale in that smart textile solutions?Ishan Chathuranga
Oh, it will most certainly. Because if you can have technologies that can just plug and play it will reduce the failure points you have in the development process. But the thing is it's it's not easy because unlike in electronics like like pure electronics in textiles, the the solution that we have come up for the problem matrices are really unique to each product and each use case but there are things that we can standardise such as some integration methods, some conductive pathway technologies, and some testings so for sure, like if we can standardise the stuff that we can use this plug and play to make the process far easier and improve the accuracy levels of manufacturing.WTiN
Wonderful. Thank you. That concludes all my questions. And that concludes the episode. Thank you so much for taking the time to speak to me. Cool, thank you. If you have any questions for WTiN then you can reach out over Twitter, find us at WTiN_comment or you can contact me there Write me at WTiN and if you fancy sponsoring an episode of the podcast please email sales@wtin.com. Thank you so much for listening and we'll see you next month.
Have your say. Tweet and follow us @WTiNcomment