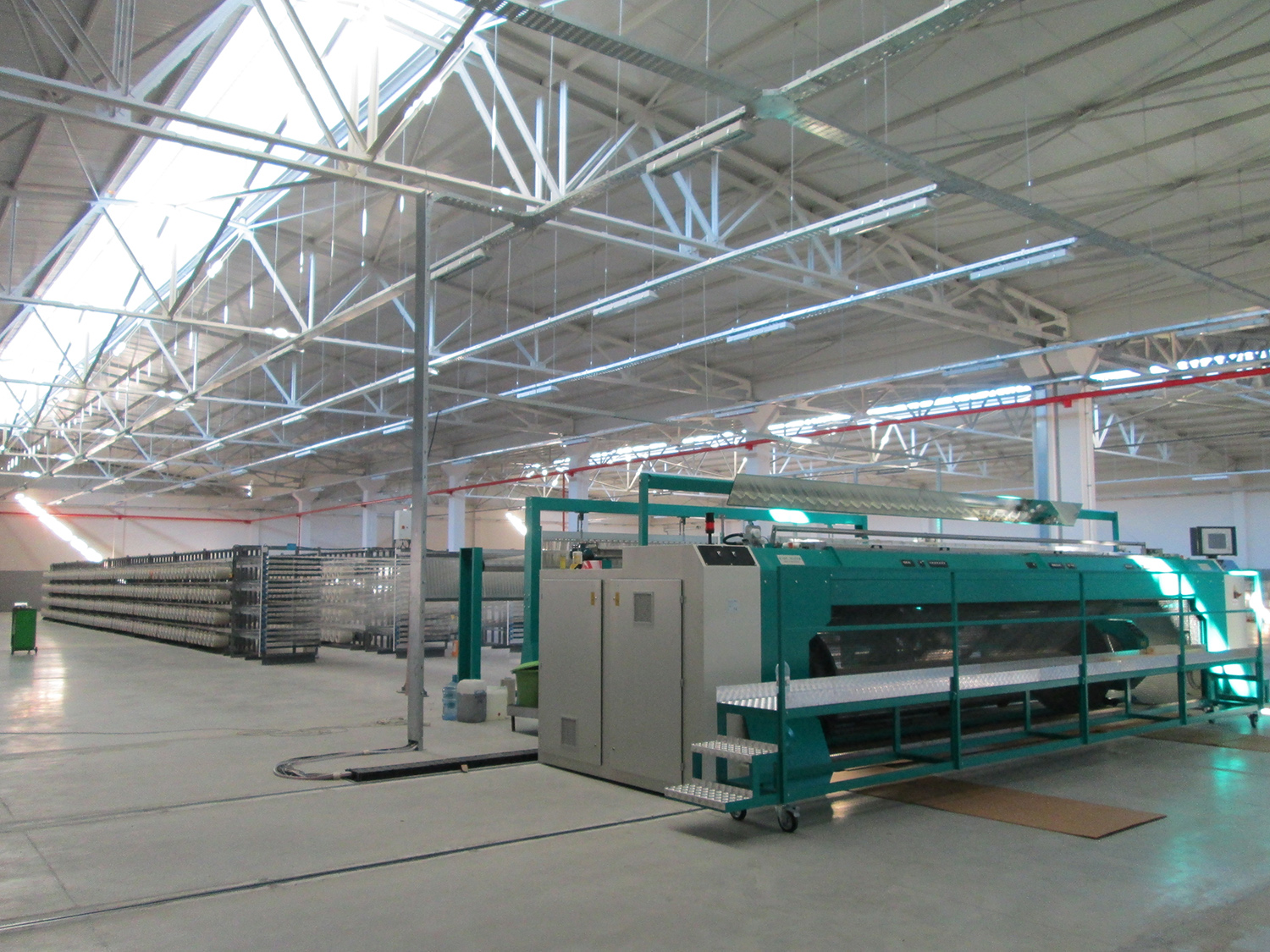
ITMA Daily News speaks with Cygnet Texkimp, an independent creel manufacturer and fibre handling expert, about manufacturing efficiency and the launch of a new robotic system at ITMA. Otis Robinson reports.
Tell us a bit about Cygnet, its foundation, what it offers to industry, application areas and target markets – and what are some of the key concerns within your sector of the textile industry today?
Cygnet Texkimp is a fibre handling machinery expert specialising in the design and manufacture of creels and automation solutions for the traditional and advanced textile market including geo textiles, carpets and flooring, tyre cord and composites. We also manufacture custom machinery and downstream converting equipment including prepreg manufacturing, coating, slitting, filament winding and recycling for the high-value carbon fibre and composites industries.
The company was founded in the early 1970s to manufacture fibre unwinding creels, initially for the traditional textile industry and then for the emerging technical textiles market around the world.
We are an independent creel manufacturer with almost 50 years of expertise designing and developing fibre unwinding and tensioning machinery and a portfolio of traditional mechanical creels alongside cutting-edge technologies such as our precision pneumatic Flatline creel. Our creels are capable of processing packages weighing up to 500kg at speeds of up to 350 metres per minute.
Our move into the automation and handling market began around 15 years ago when we started to see a significant increase in the size of fibre bobbins for which we were being asked to design creels. With heavier packages to manipulate on and off larger creels – some of which span an entire football pitch – and an increased focus on operator wellbeing and product traceability, we realised that we could add great value and efficiency to our customers’ operations by developing our own tailored automation and handling solutions.
Larger bobbins are most often used in industrial applications, such as polytapes used in the manufacture of carpet backing and polyester and glass yarns used in a range of products from sporting equipment to ship and aircraft building. They contribute to a more efficient manufacturing operation because they require fewer changeovers, but they are of course harder for humans to lift and manipulate, especially at height. We were being asked to accommodate bobbins weighing up to 350kg and measuring up to one metre in diameter in the design of our creels, and that made the need for automated handling greater than ever before. But this wasn’t only about handling large packages. Our solutions are also designed to help businesses manage repetitive lifting and manoeuvring tasks too.
What fibre handling expertise does Cygnet have?
The fibre handling expertise we had accumulated in our work designing bespoke creel technologies was critical in the design of these automated solutions. We understand fibre and we know how it should be handled to eliminate the potential for damage and to protect its integrity.
Our key aim when designing all of our systems, whether it’s a mechanical creel or a package lifting and loading system, is to design them in a way that handles and processes the fibre or yarn with ultimate care and minimal contact. This means incorporating technologies such as bellows-type grippers to hold the bobbin securely, and using highly polished, low-friction ceramic guides and smooth surface-finishes.
How important is manufacturing efficiency to Cygnet?
Automation is hugely significant in today’s manufacturing environment and can revolutionise the way manufacturers operate by enabling them to reallocate labour and increase production. In the last two decades, we’ve seen a major shift in working practices around the world that means fewer people are prepared to do jobs that involve heavy and repetitive tasks such as lifting and loading. Manufacturers need a resource to do the jobs people don’t want to do, or to make manual jobs less arduous in order to discourage employees from leaving.
As well as automatic creel loading and unloading solutions, we offer systems to wrap, pack and palletise bobbins of fibre, radiofrequency identification (RFID), barcoding and vision systems and auto guided vehicle (AGV) systems. Each technology is designed to enhance the quality of the fibre or product and the efficiency with which it is processed, either by reducing physical handling or improving traceability and in-process checking.
At ITMA you launched your Robot-AGV system. Could you tell us about this technology, how it functions and how it is beneficial to its target market?
We’re demonstrating our Robot-AGV system live on our stand at ITMA. This technology is designed to load and unload packages of fibre or yarn weighing up to 100kg on and off a range of equipment including tyre cord creels, winders, cabling and twisting machines, and shelving and racking structures, allowing manufacturers to reduce manual handling and improve processing speeds.
The compact AGV has been built to fit down narrow shelving isles or between creels and other equipment, making it an ideal solution for companies that want to automate their process in a busy factory setting. The robot can reach down to lift from floor-level package holders or up to load and unload above operator height, saving them from repetitive and potentially dangerous lifting and loading actions and increasing factory efficiency.
The robot is mounted onto an omni-directional AGV fitted with drive wheels that can rotate 360 degrees and allow it to navigate in any direction. Unlike transfer cars, which run along rails, the AGV can run anywhere it is programmed to and is ideal for use in factories with restricted floor space. The system can be programmed to follow a pre-determined route, and easily reprogrammed to accommodate layout or task changes, or controlled manually via a joystick.
Laser scanners and encoders enable the AGV to plot its exact location and navigate the factory environment safely. If an obstruction is detected, the AGV will slow down or stop moving immediately, which means it can be used for loading and unloading processes alongside operators performing manual tasks.
The system also offers full packing and palletising capability, including weighing, labelling and RFID tagging for inventory control, data management and traceability, wrapping, packing and palletising.
Tell me about the role and benefits of your creel and their applications in the textile industry.
The creel is fundamental to the quality and efficiency of every textile manufacturing line. The way in which fibres or yarns are unwound from the bobbin and fed into downstream technologies is critical to the success of the whole process and the quality of the finished material.
When it comes to manufacturing the highest quality woven fabrics, particularly in high-volume production markets, tensioning and handling are key to achieving consistency in the finished product. Controlling the tension of the yarn as it is fed into a weaving process, for example, is essential to eliminate distortion in the fabric in the form of buckling or wrinkling. The same is true in a wide range of applications, from tyre cord used to manufacture tyres for the automotive industry to geo textiles used in swimming pools.
Our bespoke creels are designed to fulfil the needs of a variety of applications and developed to provide the best treatment for each material and process, but each one is engineered using the same guiding principles of fibre care. These include the need to minimise fibre deviation throughout the process; use the correct surface finish for the material; keep tension constant and as low as possible; avoid the build-up of foreign-object debris (FOD) and stray filaments; eliminate twist in the fibre (unless it is desirable); and prioritise ease of operation, maintenance and reliability.
Our tyre cord creels, for example, are used in the manufacture of tyres principally for the automotive market and are designed to unwind tyre cord at high speeds into weaving or cord treatment lines. These are robust, mechanical creels that use a mechanical brake system to maintain the yarn under constant and controlled tension throughout the unwinding process.
By contrast, our high-capacity weaving creels feature intelligent control systems to maintain a low and constant fibre speed and running tension of the fibre into the downstream weaving process and enable operators to adjust the tension of according to the weight or type of yarn being processed. A bespoke guide system accommodates varied fibre counts (k-counts) and tow widths, and a tension recuperation mechanism offsets the effects of the shedding motion of the loom.
With thousands of tows being unwound at once, the opportunities for damage caused by fibres crossing and touching are magnified. The guide system is central to reducing fibre damage by maintaining the separation of each tow from package to process and keeping contact points to a minimum. Where fibre contact is necessary, its impact is mitigated by, for instance, incorporating highly polished, low-friction ceramic guides and smooth surface- finishes.
Another example, which is ideally suited to the unwinding of high-end carbon fibres used in the manufacture of prepregs and other composite materials, is our Flatline creel. This creel uses low-pressure, low-friction pneumatic cylinder technology to apply a consistent load or tension to each yarn or fibre tow as it is fed into a downstream process. It has been designed to be extremely easy to operate with no mechanical calibration or high-level operational expertise required to set up, run or maintain the system. Each cylinder also forms part of an enclosed module, which eliminates the potential for fibre debris to enter the tension system.
At ITMA, we are showcasing our full range of creel types, alongside our electrical and pneumatic control systems and various package sizes using a large-scale demonstrator creel rig.
For more information, visit Cygnet Texkimp at Hall 3, Booth A107.
Have your say. Join the conversation and follow us on LinkedIn