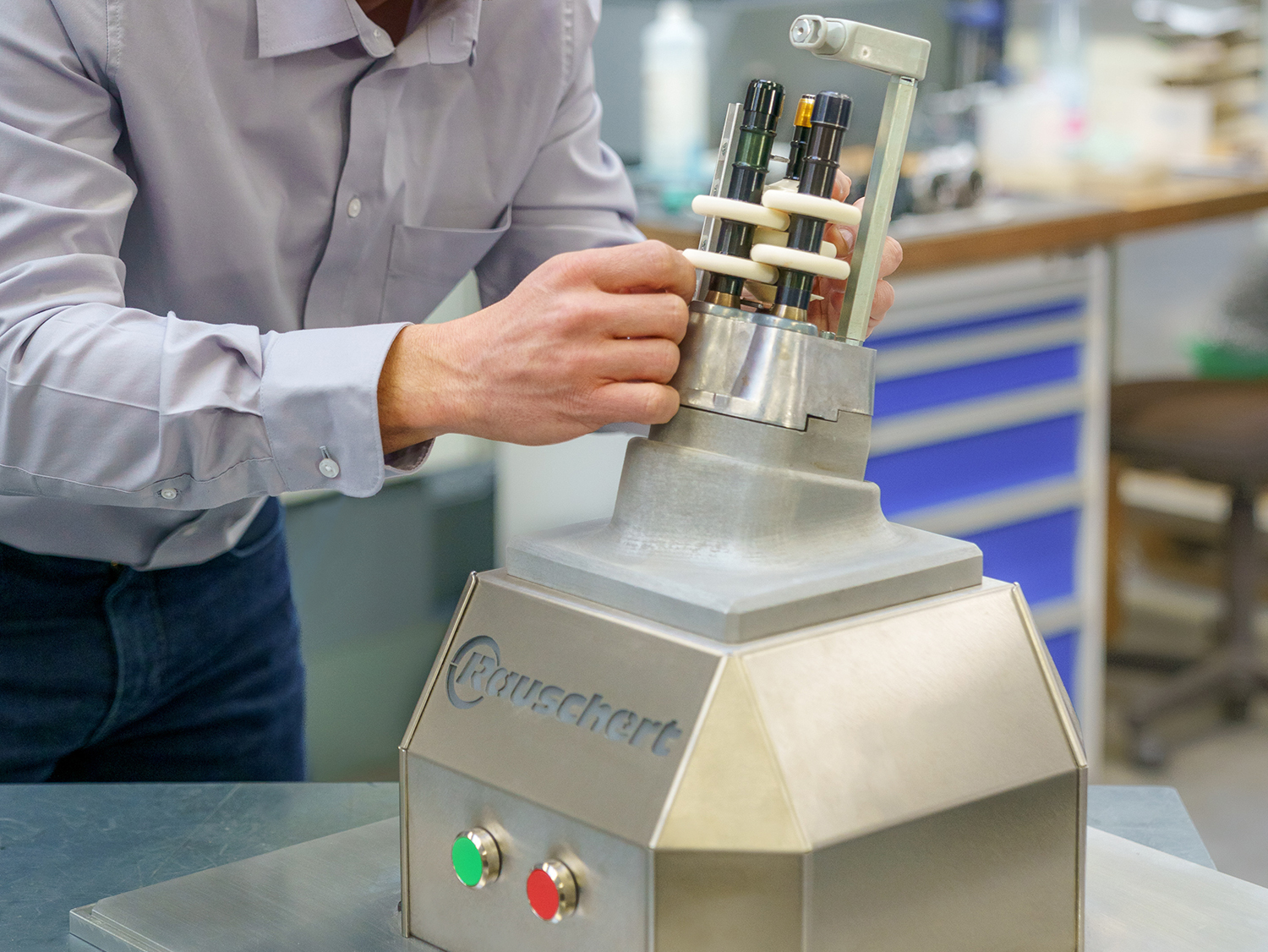
Rauschert at ITMA 2023: Extensive ceramic solutions, sustainable and efficient
By Madelaine Thomas
Sponsored by Rauschert
As a solution provider for high-tech ceramic components, Rauschert, headquartered in Scheßlitz, Franconia, Germany has been established in the textile industry for decades. Manuel Gebhardt (MG), head of production and deputy head of the Textile Product Division, discusses Rauschert’s presence at ITMA 2023 in Milan and how the company is dealing with the call for more sustainability in the textile industry.
WTiN: What will Rauschert showcase at ITMA?
MG: At this year's ITMA we will be showing components that are particularly well suited to the DTY [Drawn Texturised Yarn] process such as thread guides, twist stoppers and spindle components. In particular, we will present our Rapaltex® working disc for the texturing process. It is much more resistant than a standard PU (polyurethane) disc and gives at least as good, if not better results, for example, in terms of speed and yarn properties.
We will also show applicator guides for the POY [polyester] and FDY [Fully Drawn Yarn] process. And, who knows what areas of application will arise for our new ceramic composite materials.
Another big topic for us will be filtration technology. We offer ceramic membranes for micro-, ultra- and nano-filtration of textile waste and process water as well as customised plants. Our motto for this year's ITMA is: "We make textile production better". This also portrays our overall innovation focus.
WTiN: How does the slogan "We make textile production better" match with the technical properties of your components?
MG: We offer technical solutions that are both economically efficient and sustainable. Of course, we cannot list the technical properties of all our textile-technical products because we have an enormous range of very different components but let us focus on key components.
Our Rapaltex® working disc stands out in its complexity. It has a particularly finely machined surface, which provides numerous advantages in yarn texturing. There is less snow abrasion, and the yarn has a much better grip. In the case of a Rapaltex® working disc used on different machine types, it is possible to increase the speed by 50m/min compared to machines using a conventional PU disc. This in turn means more productivity and free production capacities.
These advantages can be accomplished through good surface engineering that effectively utilises the natural properties of ceramics.
The material properties of ceramics are also a benefit in filtration technology. Here we can offer ceramic micro-, ultra- and nano-filtration membranes with pore sizes ranging between 0.9nm and 400nm depending on the filtration process. Furthermore, our membranes have outstanding chemical and thermal resistance. They can be operated at temperatures up to 90°C. This is particularly advantageous in the treatment of scouring wastewater.
With a specially developed pilot filtration plant and the corresponding ultrafiltration membranes, we were able to filter the scouring water of a customer in Taiwan. The cleaned permeate can be reused in further scouring processes without any problems, allowing major savings in use of fresh water, energy and chemicals. This is possible because the chemicals used to clean the textile fibres pass through the membrane into the permeate. With the current operation of the plant, we have an average flow rate of approx. 300l/h through each membrane. In addition, our technology reduces energy consumption because the constant heating of fresh water for the scouring process is eliminated by using our filtration system.
In summary, we can help to make the processes cleaner and reduce environmentally harmful wastewater by using the natural filtration properties of ceramics in combination with our engineering expertise.
WTiN: To what extent does sustainability already play a major role in production at Rauschert?
MG: Firstly, it must be mentioned that we mainly produce components from and with ceramics. Ceramics are inorganic minerals and, compared to other materials such as plastic or metal, have the advantage of being much more environmentally friendly, more wear-resistant and durable. This means that ceramic machine parts have to be replaced much less often than, for example, plastic components.
Nevertheless, the ceramics industry is of course an energy-intensive industry, which we try to compensate for, for example, with our own energy management system and a large number of photovoltaic installations. This currently provides us with a capacity of approximately 10 MWP. However, our aim for the future is to have an autonomous energy supply with green electricity, achieving CO₂ neutrality. Watch this space.
For more information see: www.rauschert.com or visit Rauschert at ITMA 2023 in Hall 3, Booth D103.
Please contact Anna Schardt to arrange a meeting: marketing@prg.rauschert.de
Have your say. Tweet and follow us @WTiNcomment