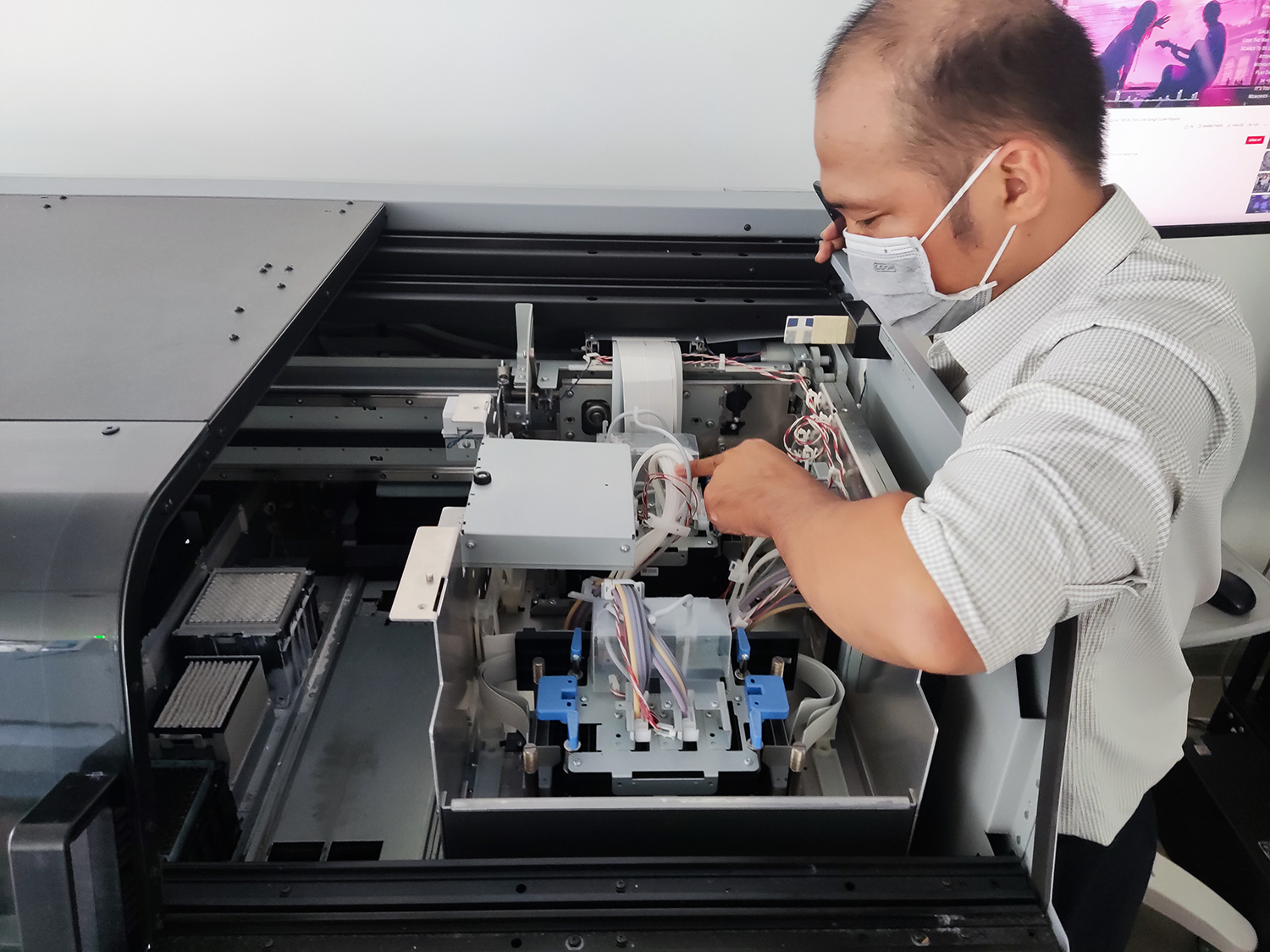
Summary
- Industrial DTG printing is one of the highest profile garment printing processes and has grown significantly over the last five years.
- It is a complex printing method that offers significant rewards.
- For optimum results, it is important that machine operatives are well trained so that they can mitigate issues and minimise downtime.
1. Introduction
Direct-to-garment (DTG) printing is a complex technology that requires support and maintenance. Ensuring machine longevity and maximum performance, while minimising downtime, is especially important on an industrial scale when the printers remain in operation across several shifts, if not 24/7.
Technical specialists and engineers need to consider certain key factors at the early stage of a DTG-related project feasibility study, but more importantly when supporting and maintaining industrial DTG printers. The following were derived from the experience of operating large volume DTG productions in Ho Chi Minh City, Vietnam:
- environmental conditions
- ink management
- equipment calibration
- software updates
- operator training
- regular preventative maintenance
- spare parts management
- regular testing and quality control
Let’s have a closer look at each one of them:
2. Environmental conditions
Industrial DTG printers must be operated in a controlled environment where the temperature and humidity are maintained within specified ranges to prevent ink from drying and to ensure consistent ink flow. The environment must also be free from dust, debris and other particles that can affect the quality of the final product, or even clog the printer’s components. Proper ventilation is important to ensure a healthy working environment for operators. Therefore, accurate layout planning plays an essential role at the early stages of any industrial DTG setup deployment.
Here are some qualitative and quantitate environmental parameters to be maintained:
Temperature
The ideal operating temperature for industrial DTG printers is between 20 and 25°C. Operating outside of this range can accelerate the drying speed of the ink in the print head, which could potentially damage multiple components within the ink system. This is because a high volume of ink residue forms in the ink lines and filters.
Other operational problems can include a shortened lifetime of the machinery due to overheating of the components. This parameter is especially critical in tropical climates when steps should be taken to intentionally lower temperatures overnight, as well as during the day. It is also essential to maintain a stable temperature within the printers’ environment to ensure that the equipment operates correctly (ie some print head models will require a technician to reload the waveforms to recover the accurate jettability when temperature fluctuates).
Humidity
Ideal humidity levels for industrial DTG printers are typically in the range of 60%-75% relative humidity. Humidity levels that are too low will cause ink to dry out faster on the nozzle plates, which ultimately leads to excessive manual or autocleaning cycles. This increases ink wastage, which is costly for the user. High humidity can also result in excess moisture that can harm the printer’s components – electronics in particular – in cases when the moisture is condensing on the surface of the components. Like temperature, it is equally important to maintain a stable humidity level around the print heads for a smooth ink flow.
Ventilation
Proper ventilation is crucial to ensure the printer environment is free from dust and debris. In mass production facilities, operatives have to deal with large quantities of garments/raw panels, each of them having surface debris and fibres from the fabrics. These potential contaminants can clog the printer’s components, thus negatively affecting print quality and potentially damaging the equipment. A well-ventilated environment can also help regulate temperature and humidity levels to ensure optimal printer performance.
Cleanliness
Keeping the printer’s environment clean is equally important to maintain optimal print quality. Dust and debris can accumulate on printer parts (especially those more exposed to the environment, such as optical and laser sensors). Poor cleanliness can result in print head clogging, misalignments and malfunctions. Dry or contaminated inks that were not cleaned in a timely manner can result in a loss of nozzles, ink starvation, banding and other issues. Regular cleaning of the printer’s environment, including the printer itself and any surrounding surfaces, can help prevent these issues and extend the lifespan of the equipment and its spare parts.
3. Ink management
Proper ink management includes the considerations below.
Ink viscosity
While the OEMs typically provide inks for their machinery (some even make closed systems with ink chips), inks are selected based on the viscosity that a certain print head is designed to handle. A variety of print heads are used across an expansive range of DTG printers, so careful consideration of viscosity based on the print head’s technical specifications is critical.
Waveforms
The ink jetting process of each print head is defined by the waveform. The important timings and the voltage levels will determine what is happening at the nozzle where the ink chambers release the liquid ink and are re-filled. Building a waveform is a complex process that is commonly a result of mutual work of both the equipment OEMs and ink manufacturers. Selecting the ink set along with its own waveforms is crucial to achieve the print head’s optimum performance in the DTG print production process.
Agitation and storage
It is essential to use only compatible inks, but also agitate them well. The titanium dioxide (TiO2) – the main component of white DTG inks – tends to be heavier than other white ink components and therefore agglomerates at the bottom of any ink container. In order to extend the ink’s shelf-life and avoid ink building up in storage while remaining idle, it is necessary to store them correctly so that they remain fresh and reliable. A simple ink agitation machine that is able to continuously rotate the ink containers – bags, bottles or cartridges – can significantly help in any storage operation procedure.
Quality
DTG remains the premium type of garment printing, and high quality DTG inks remain critical to the operation of any DTG printer. Using low-quality inks can cause clogging, banding and other issues that can harm print quality and significantly increase machine downtime, which costs the print service provider money.
4. Equipment calibration
Proper equipment calibration is essential to achieve consistent high quality across thousands of daily prints. Industrial DTG printers require regular calibration to ensure their nozzles are aligned correctly, their head heights are set accurately, and the ink droplets are jetted precisely. Failure to calibrate correctly can result in poor print quality, clogged nozzles and other issues that negatively impact production efficiency. Do not forget to regularly check the items below.
Negative pressure
Negative pressure is an important variable to control in any inkjet system. In most industrial DTG engines, negative pressure is generated and controlled by the pressure regulators, while the compressed air is supplied to the engine from the external source. In some smaller systems, negative pressure is maintained mechanically by a set of dampers. The ultimate purpose is to create a vacuum in the ink lines, to regulate ink flow and prevent air bubbles from forming. The values of the negative pressure must be carefully checked, kept at a stable level and the air-free operation in the ink lines and print heads must be maintained for the proper engine’s operation.
Print head alignment
Print head alignment ensures accurate ink droplet placement on the fabric. Precise alignment minimises ink wastage and can prevent banding or blurring, which inevitably affects the quality of the final print. Inconsistent alignment will reduce the quality of the image and lead to an increase in cost for the print house that is producing the prints.
Print head height adjustment
The proper print head height is typically around 3mm over the fabric in most DTG print engines. The adjustment ensures that the print head is at the correct distance from the fabric. If the print head is too close it can cause crushing or smudging of the fibres, but if it’s too far away the ink droplets may not adhere properly to the fabric resulting in poor print quality. Proper height adjustment also helps to prevent damage to the print head and prolongs its lifespan.
5. Software updates
Industrial DTG printers rely on both the machinery firmware and RIP (raster image processing) software to control their operation and produce high-quality prints. Regular firmware and software updates are essential to fix bugs, improve performance and add new features to the DTG print production process. It is critical to stay up-to-date with the latest software releases to ensure optimal printer performance.
ICC profiles are an integral and important part of the RIP software. The ultimate purpose of a proper ICC profile is the accurate colour reproduction. An ICC profile is a data set that characterises the colour behavior of the printer, ink and substrate combination. By making a proper ICC profile, a DTG tech specialist adjusts the colour information so that once the artwork has been processed by the RIP software, the final output of the print accurately matches the desired colour. This is especially important for industrial DTG printers that need to produce consistent and high-quality prints across hundreds of multiple jobs and substrates.
6. Operator training
The human factor continues to play a vital role in the print production process, and it is necessary not to neglect the proper operator training, which is a combination of technical knowledge and the Standard Operational Procedures of the industrial printing facility. Therefore, the contribution of technical specialists to the content of the training is very important.
Operators should receive thorough training and hands-on experience on how to use the printer, including loading and unloading garments, preparing artwork files and maintaining the printer on a daily, weekly and monthly basis. A basic understanding of the QC (quality control) procedures is also necessary to reduce the rejection rate. Complete training will not only help prevent operator errors and improve print quality but will also extend the lifespan of the equipment.
7. Preventative maintenance
DTG printers have many moving parts: print heads, platens, pumps and motors. These all require regular preventative maintenance. Regular cleaning of these components is necessary to prevent clogs from dry ink, misregistration of the layers and other operational problems. Additionally, routine inspection and replacement of worn or damaged parts can help avoid costly downtime and repairs. Some items to consider for more effective scheduled maintenance are below.
CMMS
CMMS (Computerised Maintenance Management System) provides a centralised platform for scheduling and tracking equipment maintenance activities. With such a system in place, the maintenance team of any DTG print production facility can create and manage maintenance schedules based on the actual usage and condition of the printers, pretreatment machines and dryers, rather than relying on time-based schedules.
It is important to monitor the printer’s performance data to identify potential issues before they occur, which helps to reduce production downtime. Using CMMS at DTG facilities can also help the technicians track and analyse maintenance history to identify trends and develop better maintenance strategies. It helps extend the equipment’s life, avoid daily disruptions and lower maintenance costs.
Spare parts management
In order to perform preventative maintenance along with the ad-hoc repair jobs on the printers, the stock of spare parts should be kept at hand, to reduce downtime caused by equipment failure. It is important to have an inventory of commonly used spare parts (such as filters and sensors) and replace worn or damaged parts promptly. Even if the piece of equipment is under warranty, the spare parts from the available stock can serve the reduced downtime requirement, whereas parts under warranty can later be delivered to refill the stock.
8. Regular testing and quality control
Regular testing and quality control are essential to ensure consistent print quality and identify potential issues before they become major problems. Technicians should team up with the QC staff in production to regularly test prints for colour accuracy, image sharpness, wash fastness, crockfastness and other quality factors. Regular testing can also help detect machinery issues such as clogged ink lines, misalignments and other operational problems before they result in costly downtime.
Key takeaways
- Industrial DTG printing is a combination of highly sophisticated technology, complex production processes and verified standard operational procedures.
- The print process requires support, service and maintenance on all levels to ensure optimum environmental conditions. Ink selection, calibrating equipment, software updates, preventative maintenance, operator training and regular testing are crucial steps
- Service engineers with specialised knowledge in DTG printing and thorough training play a vital role in supporting and maintaining these complex systems.