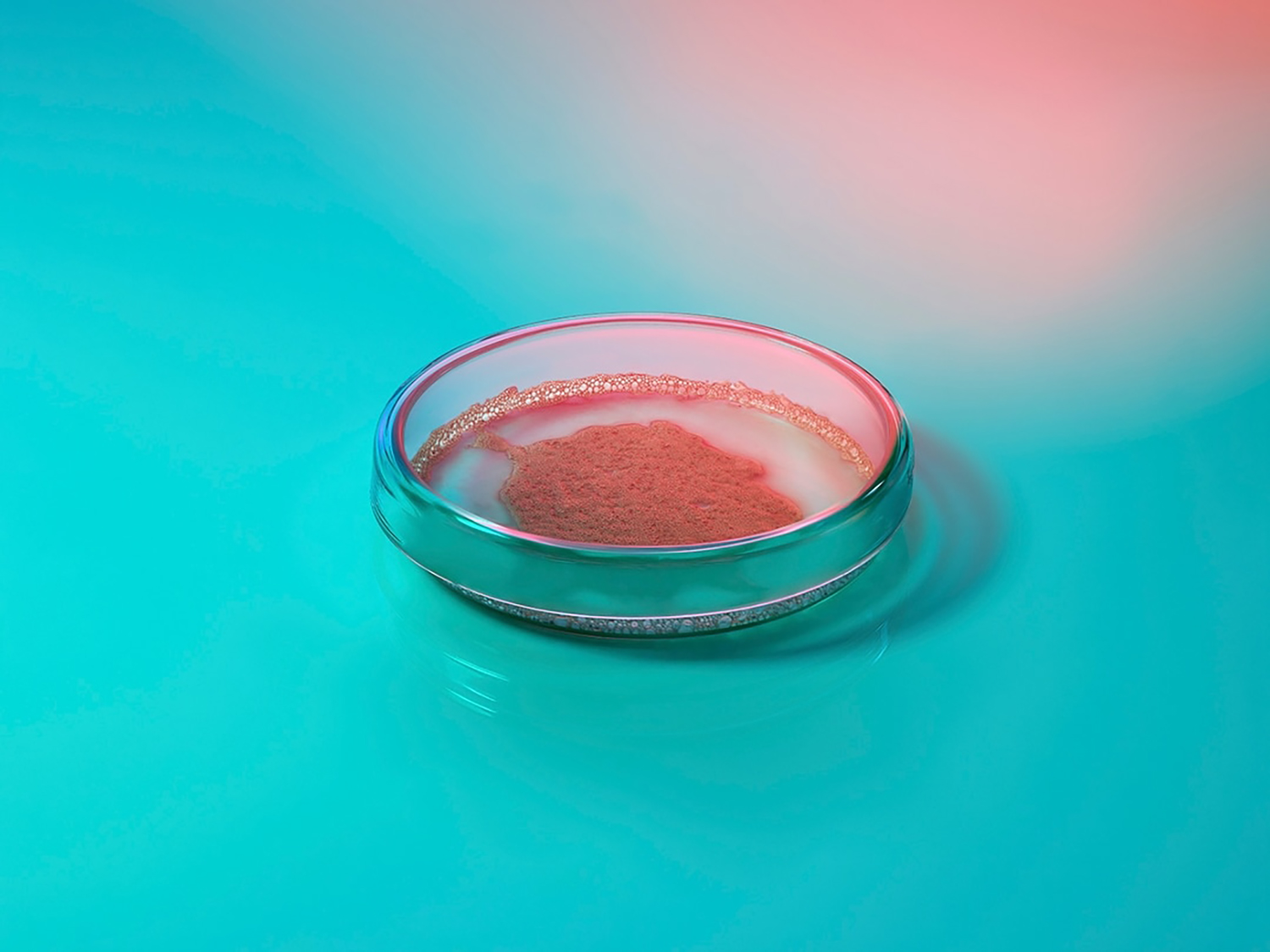
-
Understanding the commercial readiness scale
WTiN’s Commercial Readiness Scale gives an indication of what stage of commercialisation a product is at. It ranges from Emerging: a research stage development; Scaling: the product is being produced on a small but growing scale, and Commercialised: the product is well-established and ready to purchase.
Catherine Roggero-Lovisi chief executive officer at Modern Meadow, a bio-design technology company, talks about the company’s Bio-Farm technology, traceability and research.
Modern Meadow, based in New Jersey, US, is a bio-design company that wants to “redefine what’s possible” in terms of green technology, by moving away from petrochemicals and animal-derived substances. It uses nature-inspired proteins in combination with other molecules to bring sustainable chemicals and materials to market. Its technology enables companies to create products that are free of animal or toxic chemical inputs, with substantial reductions in other environmental impacts such as greenhouse gas emissions (GHG), water, energy and waste. Modern Meadow focuses its efforts within three business units: biomaterials, beauty and wellness, and biomed.
Back in 2011 father-and-son team Gabor and Andras Forgacs developed a form of biofabrication called bioprinting, which resulted in the formation of the duo’s first company, named Organovo . While living in China, Andras saw first-hand the rapid growth in consumption – notably of animal products for leather and meat – and saw the toll this was taking on the environment. The creation of Modern Meadow as we know it now came after the Forgacs found a way of using the principles of biofabrication to replicate animal products using plant-based proteins.
Now, Catherine Roggero-Lovisi is spearheading the company as chief executive officer (CEO). According to Roggero-Lovisi, Modern Meadow believes the commercialisation of its innovative bio-based technology will drive increased consumer access and adoption, in turn, shifting manufacturers and consumers away from dependence on unsustainable petrochemical and animal supply chains.
Bio-F@RM technology
Modern Meadow’s proprietary four-step application platform, Bio-F@RM stands for Fermentation-based Active Recombinant Macromolecule protein. Roggero-Lovisi says: “The platform combines our proprietary know-how regarding strain engineering, protein design, analytics, precision fermentation and downstream processing to produce tailored proteins with desired properties and functionality for various applications.”
The first is design proteins. Through evaluating the different proteins from various species based on their amino acid sequence, structure and function, Modern Meadow can identify and select the specific proportions that deliver the desired functionality. Roggero-Lovisi says: “In many cases, we also modify protein amino acid sequences or combine different portions in creative ways to design unique proteins that are not found in nature. By doing this, we’re creating a library of protein ‘blueprints’ to target the desired functionalities and properties.” Those ‘blueprints’ are translated into DNA sequences that trigger the production of a specific protein. The process then engineers yeast cells by chemically synthesising the DNA and introducing it into the yeast cells, along with “regulatory” fragments that enable the translation from DNA to protein.
The engineered yeast cells are grown in a fermentation tank with optimised feed, such as fertiliser, and internal conditions, such as temperature, pH and oxygen levels, to produce the desired protein via the fermentation. Once the protein has been grown, the yeast cells are removed, and the protein is purified using separation equipment such as centrifuges and filters. The final purified protein is ultimately dried and ready for final formulation.
Green chemistry
Modern Meadow’s Bio-Alloy green chemistry solution combines plant-based proteins and biopolymers to bring performance and sustainability to materials at scale. Roggero-Lovisi says: “It’s the underlying technology application platform that serves as the foundation for all our biomaterial solutions. Our select plant proteins, combined with biopolymers, create a molecularly mixed miscible blend with performance, design and durability features.”
The initial Bio-Alloy for biomaterials is created by combining US-sourced soy protein isolate (SPI) – a plant-based protein – with bio-polyurethane (bio-PU), which is a bio-based polymer. Roggero-Lovisi continues: “This patented miscible blend delivers unique performance features to the materials it is applied to, including – but not only – strength, durability, wear resistance, enhanced dyeability and breathability. These mechanical properties are tuned based on application requirements.”
Certification and traceability
Modern Meadow’s Bio-Tex is a material system comprised of a Bio-Alloy coating applied on a fabric backing, which creates flexibility for designers in colour and haptics, among other things. It’s a certified bio-based product under the United States Department of Agriculture (USDA) BioPreferred Program, meaning it carries the USDA-Certified Bio-based Product label. The label was designed to provide useful information to consumers about the bio-based content of the product.
The USDA has established minimum bio-based content standards for many product categories. A product must meet or exceed the minimum bio-based content percentage in its given category to qualify for certification. In the case of the Bio-Tex™, the minimum bio-based content requirement is 25%.
Modern Meadow says it considers the traceability of the materials and finishes that it produces. Roggero-Lovisi says that, together, the company works with manufacturing partners and ingredient suppliers to maintain a complete transparent supply chain system where inbound raw materials are qualified and complete a chain of custody documentation. The process is maintained with accompanying certification where applicable. She continues: “In production, our manufacturing partners employ the most up-to-date Enterprise Resource Planning (ERP) systems that capture detailed batch records on run condition and material inputs for each manufacturing run.
“Our manufacturing partners produce goods for major global brand partners and go through rigorous supply chain, customs security, social and environmental compliance audits. These audits are often performed by internationally recognised or sanctioned audit agencies such as SGS, Intertek and [are] sometimes re-audited on an annual basis.”
Alternative leathers
The competitive set of alternative materials to traditional leather has largely remained consistent over the last few years, according to Roggero-Lovisi. The group of materials can be divided into microbe-derived, plant-matter derived, mycelium-based and cell-culture-based. Modern Meadow offers two leather alternatives, called Bio-Tex and Bio-Vera.
The Bio-Tex material line competes with other microbe-derived products. Roggero-Lovisi says: “It offers the advantage of added protein functionality while giving the material a more natural feel, the ability to dye and abrasion resistance while still [offering] bio-content. Bio-Tex generally offers better performance than [other plant matter-derived] alternative leather.”
Some market leaders continue to struggle to address the fundamental barriers that mycelium materials wrestle with, such as scalability and material performance. Modern Meadow’s alternative, named Bio-VERA, is a novel, sustainable and animal-free biomaterial that looks, feels and naturally ages like traditional leather, suede or chamois. It’s powered by Modern Meadow’s Bio-Alloy and available in rolls, as well as requiring no special preservation or storage conditions. Roggero-Lovisi adds: “It’s a plug-and-play technology that can be seamlessly dropped into the current supply chain and infrastructure, making it easier to scale with favourable techno-economics.”
Resource-efficient dyeing
Bio-FREED is another of Modern Meadow’s innovations. The one-step, foam-based dyeing system uses 95% less water, 75% less energy and 80% fewer dyes and chemicals, than traditional dyeing, with no salts. Textiles of any fibre type can be dyed with reactive or acid dyes with no colour limitations or migration. Bio-FREED stands for Fast Resource Efficient Enhanced Dyeing, says Roggero-Lovisi. Powered by its Bio-Alloy technology, the application can replace the three-step dyeing process often used for blended fabrics.
She continues: “In addition, Bio-FREED offers process flexibility by enabling the pre-dyeing and post-dyeing of the textiles with both acid and reactive dyes. This is envisaged to give the textile industry new and unique design efficiencies, such as dyeing garments after they are made, thereby gaining additional environmental and supply chain benefits.
“Colour mitigation associated with disperse dyes in blended textiles is also greatly improved through the one-step Bio-FREED™ reactive dye process. Finally, the ability to precisely deliver protein functionality to fibre surfaces is expected to provide a path toward textile circularity. Applying the Bio-Alloy to a textile preserves the fibre properties without introducing covalent bonds between the Bio-Alloy and the underlying fibre substrate. This is expected to assist in preserving the fibre for future use.”
Have your say. Tweet and follow us @WTiNcomment