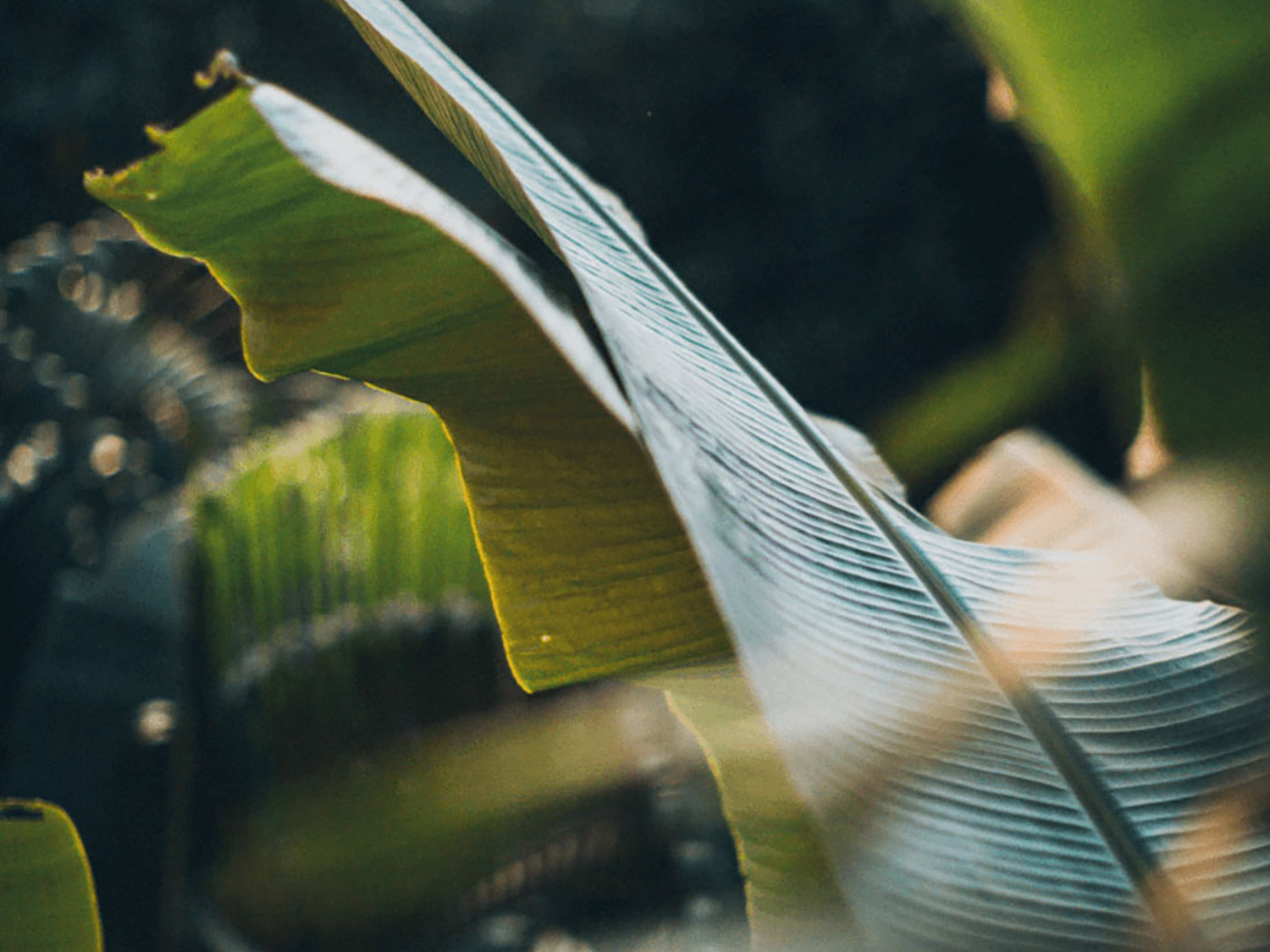
-
Understanding the commercial readiness scale
WTiN’s Commercial Readiness Scale gives an indication of what stage of commercialisation a product is at. It ranges from Emerging: a research stage development; Scaling: the product is being produced on a small but growing scale, and Commercialised: the product is well-established and ready to purchase.
The Textile Innovation Podcast speaks with Graham Stewart – the man behind the patent-pending holistic Fibre52 process – about certification and evolution within the textile industry and the balance between sustainability and profitability.
As conversations turn to sustainability more and more frequently, many brands, mills and companies worry about how they can remain profitable while minimising the impact their business has on the environment as much as possible.
In episode 93 of The Textile Innovation Podcast, we speak with Graham Stewart: the man behind the patent-pending technology called Fibre52. The Fibre52 process is holistic from prep to dye, and mill tests around the globe show it’s consistently repeatable. Cotton prepared for dye and dyed with Fibre52 is naturally hydrophobic and repels water, while it is versatile enough to be hydrophilic if desired.
There is no need for additional machinery or upfront investment and users will benefit from a 25% reduction in processing time, up to 40% less energy usage and up to 70% reduction in water, according to Stewart. He talks to WTiN about certification, sustainability, how the Fibre52 technology came into being and how it can help manufacturing processes.
If you’d like to get in touch with Graham Stewart, visit fibre52.com.
You can listen to the episode above, or via Spotify and Apple Podcasts. To discuss any of our topics, get in touch by following @wtincomment and @ruby_wtin on Twitter or email rpenson@wtin.com directly. To explore sponsorship opportunities, please email sales@wtin.com.
-
Transcript
This transcription has been AI generated and therefore may have some inaccuracies.
Ep. 93: Working with nature for better cotton
The Textile Innovation Podcast speaks with Graham Stewart – the man behind the patent-pending holistic Fibre52 process – about certification and evolution within the textile industry and the balance between sustainability and profitability.
WTiN
Hello and welcome to textile innovation hosted by WTiN. My name is Ruby and I'm the news editor and your podcast host. Each month we're going to be joined by a brand new special guest. So join me and my colleagues as we deep dive into what's new, what's interesting and what unmissable innovations have hit the market recently, we cover everything on the podcast from sustainability to startups and the latest research developments. And we also quiz the experts in the fields about their new products and ideas across a huge spectrum that is the textiles industry. So no matter what your interest is WTI and have you covered and we can connect you to everything you need to know right here from our central hub in the UK. In this episode, we speak to Graham Stewart about his innovation fibre 52 That could change the way that the industry dies garments. Stuart's expertise within the textiles industry has taken him around the world from Hong Kong to Australia, the US and weigh more, we pick his brain on sustainability, fibre, 52 and scalability among other things. So first of all, Hello, and welcome to the episode. Very happy to have you here. Thanks,Graham Stewart
Ruby. Thanks for inviting me on the pod.WTiN
No problem. So do you want to start off with some of the basics you can tell us about yourself and your history within textiles?Graham Stewart
Yeah, Ruby, I'll try and keep this as short as possible. So I'm into my fourth working decade. I began life as a de commissioned dying in Huddersfield, Yorkshire. We had a number of dye houses. We're one of the largest players in Europe. I was fortunate in those days studying for my society of days and colorist degree above University, I was able to relate that study back into into practice, I found that to be a great way to learn. So after 10 years, 12 years is a day with tender houses and some weaving and spinning and move to dosta to national a large cashmere knitwear brand house, we own Pringle Braemar, Valentine with George Berry and so on. A lot of knitwear companies we were vertical, one of the largest cashmere companies in the world, we had big agreement with China and importing cashmere. I initially had the sales and marketing for the fabric divisions and we were the world's leading Slipknot or for for manufacture. We had about 60% of the world market in those days. And then that took me to the states where we acquired large knitting and garment operations with sport and utility brands in the USA, Pennsylvania, New York. I ended up developing those brands in Europe and Asia community across the Atlantic for three years. I had 10 years with Dawson International. Then I became General Manager Europe for the world's largest oil processor and tried to move to Italy for a few years and then on to headquarters in Adelaide, Australia. General Manager marketing with a big focus on China and Hong Kong joined our largest customer actually, novel Industries, a large textile conglomerate. Three years later, I was appointed General Manager of Australian wool innovation, the administrator of the Walmart company in Sydney, Australia. I then joined Nino Cerruti a successful Italian textile industrialist and designer. I then joined Shanghai challenge textiles as marketing director. Finally, I moved to Bozeman, Montana from Shanghai to co found tacos tacos. We call it and trademark shoot to shelf because it was the first of its kind, highly visible supply chain from shooting my partner's 12,000 sheep through all the production stages to garment production and branded apparel. Which brings me to Charleston today where I live in South Carolina and fibre 52.WTiN
Wow, that's impressive if you've worked in every area, so on to fibre 52 Why don't you tell us about what it does the history as inspirations and goals and anything like that.Graham Stewart
fibre 52 is a process a process to bleach and prepare for dye and dye cotton. In a in a departure from traditional methods. Instead of using the heavy alkali, that's been the norm for decades, we use bio products. So I've developed bio products to process cotton that leaves cotton stronger, and it's my natural state. And the bio products are designed in the process to work at lower temperatures with much quicker process times using less water in comparison to traditional methods, less energy and in most cases, a considerably lower carbon footprint, the history let's say in the USA, I've done a great deal of my own dying so you know whatever I've done in my career, I've pretty much always had something to do with dying and I did I did on my own wall down for the course and I noticed that cotton was being processed with such long processing times. And I was invited actually to look at recipes and just see if I could do something with them. And I noticed just how much time they would use in how much heavy alkali was being used with hydrogen peroxide. Without getting into the weeds, that does a lot of damage to cotton. This history was probably the inspiration to do something better and more sustainable in cotton, the goals to be the go to process for bleach and PFD and dang cotton around the world and to invest further in fibre 52, were committed to doing that, as we're all fibre 52 out around the world, we may you know, down the line look at processing other fibres in a more sustainable world and is presently done para de btrn.WTiN
We use a commercial readiness scale consisting of emerging scaling and then commercially ready Where does fibre 52 stand on that ladder? And what phase of production are you at currently? And what are your production capabilities?Graham Stewart
That's a good question after our initial launch in December 22, we've been making great progress. If I can put it this way. We're currently in the emerging fears that says we're thus as we relate to it our first because we do think a lot about this with our growing team, fibre 52 The great thing about our novel patent pending process chemistry is that we're using commercially available bio materials which are already in the supply chain. And they're used every day for food and in the pharmaceutical industries as well as textiles. We think of them as bio inputs for our process chemist, which means we can realistically scale to the commercial volumes that are expected in the textile, and apparel industries around the globe. From day one, we've been focusing on that scalability. And and this has helped us get into a lot of pilot trials, I can say with some of the world's largest fashion brands and textile mills, you know that that's my daily life, we estimated the person we're going to graduate from the emerging fears to what we call the scaling first by sometime this year, I guess, to summarise that we're in the emerging first today using scalable materials in the global supply chains this year fairly soon. I believe we'll be moving into the scaling phase. If we continue at this pace, which I'm sure we will.WTiN
That's an exciting stuff. Yeah, for sure. When it comes to the actual process to bleach, and Daikon, can you tell me more about that?Graham Stewart
I started to question present process practices, and embarked upon a great deal of trial and error, you have plenty of error to making incremental process progress, you know, to develop that better process. But importantly, I was doing that in existing equipment, I could see that, you know, there have been some sustainable moves. But sometimes you have to pay a lot for brand new equipment that doesn't exist inside I am on fibre 52 to work around the world, in the equipment that already that already exists, I made a big breakthrough to answer your question about 15 months ago, I mean using widely available and inexpensive buy a product it was one product that I added to the process, there are only three to four in depending how I do it, there are only three to four in in in the process, but found this particular buyer product worked efficiently to catalyse the whole process. And this was a really big time saving element that the process was really reduced in time. And so having got to that point, you know, we could see that the process was using up to now use the words up to because of the huge variation of equipment around the world, but it uses up to 50% less energy, and in many cases up to 50% less water. And again, that comes down to the existing die machinery around the world whether the liquor shows attend to 1521421, whatever they may be, we are well into a lifecycle analysis was a prominent university in Europe. In that a lot of the processing that we do around the world, we particularly in Europe, we feed into that your university, because we're under NDA, I'm not allowed to say which university is but meanwhile we've we've developed a calculator which we share with mills around the world. So there can quite accurately estimate the savings that they can make by adopting 552 Which that calculator is proven to be extremely important as we roll fibre 52 out around the world.WTiN
Amazing. So I'm the complete opposite side to that. Can you tell me about some of the challenges that you've overcome already with fibre 52 and the technology,Graham Stewart
the fibre 52 process to me is a complete change of mindset in the treatment of cotton. Remember, you know this is a very traditional industry We've experienced an enormous amount of interest. But I gotta say that often comes with a healthy amount of scepticism. Let's say in the you know, this is each change is not a difficult change. As I say we're travelling across the globe currently providing fibre 50 tours efficiency and repeatability into those processes around the world. With a great deal of success is important. The the process is efficient and repeatable, but quite often a dire or a technologist will insist that prybar 52 cannot work. I mean, you know, I, I do a lot of trials myself, and quite often diners are very sceptical, you know that I often hear that all the day won't exhaust there's not enough alkali in there, or the temperatures are too low, the dwell times are too short and so on. You know, it's just great to see how pleasantly surprised these managers become once we've completed a few trials with them. And when I say trials now those are often three to 500 pounds, you know, so they're not small trials.WTiN
Are there any current or future development ambitions for the technology, such as overcoming a challenge or venturing into a new area or fine tuning the technology any further?Graham Stewart
Yesterday, we were venturing into new areas for present and future development as the word spreads. A good example is inquiry from the nonwoven industry, which I didn't expect this will probably be a medium term development. But the non woven industry is an enormous user of fibre, whatever it might be, but also a cotton. And also yesterday, for instance, we had an inquiry to quickly do trials in pad batch processing which up to now we've we've not done. I think we've always strived to fine tune and optimise fibre 52.WTiN
So on a more broad topic, how do you think with your experiences and what you've seen so far in the industry? How do you think the textile industry itself has evolved? And maybe more importantly, how do you think it hasn't evolved?Graham Stewart
I know we're in we are involved in what is a traditional industry, I have not personally seen a great deal of progress in the more traditional textile sectors over the last decade. However, I do feel the pressure to move and adopt these more sustainable processes as I feel pressure coming down the pipeline, particularly from governments, from ecological bodies from certification bodies who asked for higher standards to meet their certification requirements. And we're going through quite a lot of that right now. Cost there's a pressure on industry driven by ESG, you know, environmental, social and governance, investing and also socially responsible and impact investing, which, you know, we see, a lot of these days, these realities are driving textile manufacturers, there will be more legislation, there will be more pressure. AndWTiN
on the topic of sustainability. Actually, why is it do you think that textile manufacturers struggle to balance sustainability with profitability? Do you think these two things have to be separate?Graham Stewart
I definitely don't think that sustainability and profitability have to be separate, we do see there is a focus upon the cost of raw materials, for instance, in dyestuffs, and chemical costs, that's normal. However, we would have daily fibre 52 discussions about using you know, one or two or even three fewer wash offs in dying. Because you know that we're seeing a great deal of water. For instance, one wash off in the dyeing process will be like me think 10,000 litres of water per 1000 kilogrammes of fibre. So you do that three times you're into 30,000 litres of water. And you know, fibre 52 does cut down. We do save water, we look hard at the cost savings. And it's the same for saving time for saving temperature and for saving energy. And we encourage companies mills and brands to work with us in this as a day to day part of our trial and work. This is all about balancing sustainability with profitability.WTiN
Amazing and that is such a good place to end for questions and end the podcast. Thank you so much for coming on and chatting to me. This has been brilliant. Thank you. If anyone is listening who is interested in chatting with you further, what is the best way to get in touchGraham Stewart
I would suggest go to fibre 52.com. All our contact details are there and we very much encourage engagement with with your listeners in the industry. Thanks so much for having me on the pod Ruby.WTiN
It's no problem. It's been an absolute pleasure. If you have any questions for WTiN then you can reach out over Twitter Find us at WTiN_comment or you can contact me directly at WTiN and if you fancy sponsoring an episode of the podcast Please email sales@wtin.com. Thank you so much for listening and we'll see you next month.
Have your say. Tweet and follow us @WTiNcomment