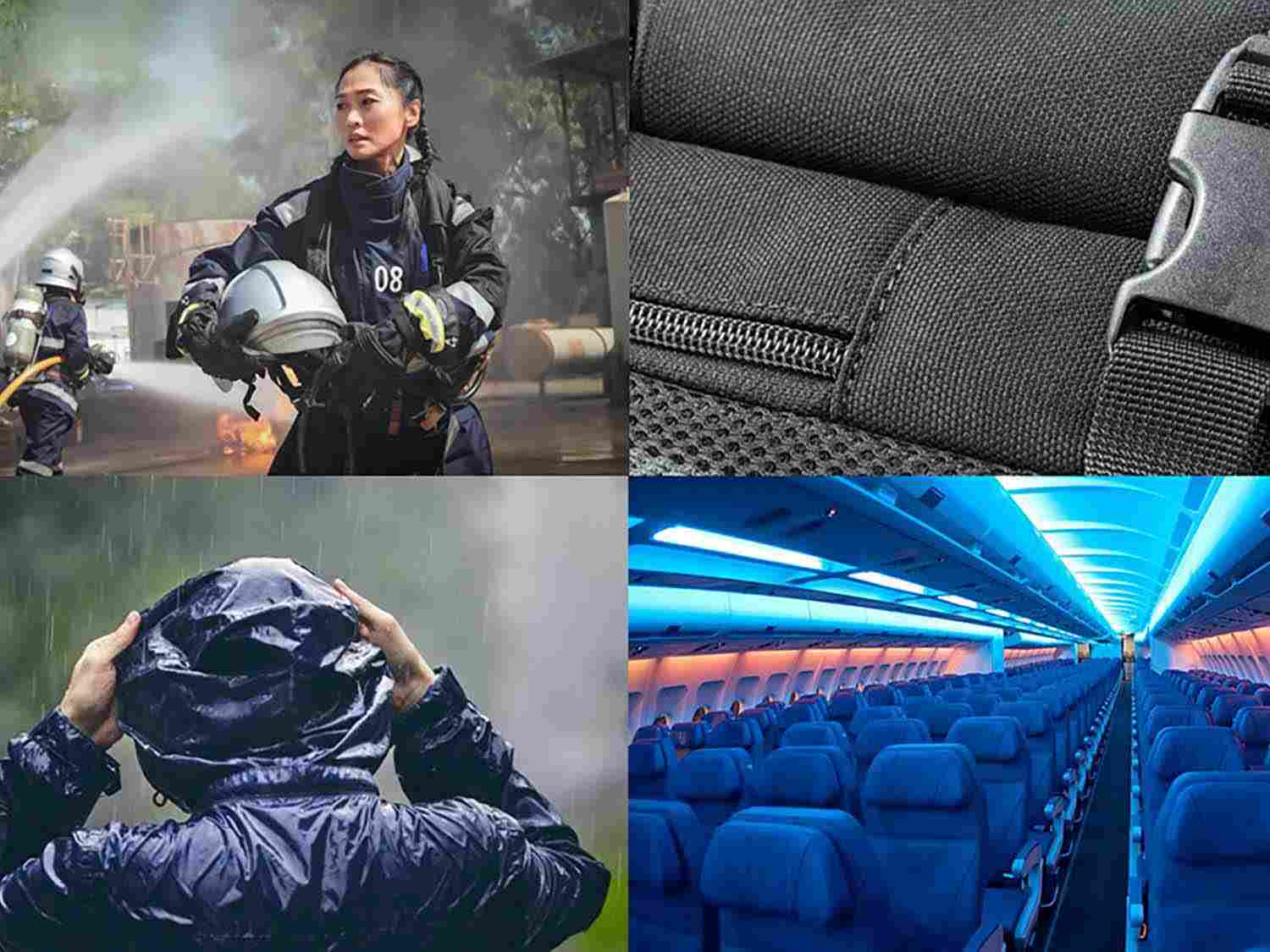
-
Understanding the commercial readiness scale
WTiN’s Commercial Readiness Scale gives an indication of what stage of commercialisation a product is at. It ranges from Emerging: a research stage development; Scaling: the product is being produced on a small but growing scale, and Commercialised: the product is well-established and ready to purchase.
Sponsored by British Textile Machinery Association (BTMA)
Members of the British Textile Machinery Association (BTMA) are increasingly involved in projects aimed at the further development of advanced technical textiles and reinforcements for composites.
As the association continues to expand its membership, newly-developed high performance fibres, technical textiles and composite materials are finding success through meeting the demand for them in high value industries such as aerospace, renewable energy, automotive and the medical sector.
Jason Kent, CEO of the BTMA, says: “These are certainly areas of high growth and opportunity. An important factor underpinning the success of our companies here is the strong collaboration between industry and the many universities and institutes in the UK. There has never before been such a high level of close collaboration between companies, academia and research institutes in the UK as at present.”
Advanced composites
Cygnet Texkimp, for example, is currently leading the design and build of the UK’s first carbon fibre research lines for a project led by the National Composites Centre (NCC) in Bristol to accelerate the development of more sustainable carbon fibres.
The company has also been part of the £39.6m Ascend advanced composites initiative which recently completed, involving 16 partners led by GKN Aerospace in collaboration with McLaren Automotive.
Prepregs
Cygnet is the world’s largest independent manufacturer of machines for the production of prepregs – integrated rolls of fabrics and resins which are widely employed in the composites industry – in addition to a portfolio of related handling and converting machines.
“Decarbonisation is a major priority for manufacturers globally,” says Cygnet CEO Luke Vardy. “We’re developing the capability to process technical fibres in ways that enable lightweighting, hydrogen power and electrification, reduce waste and revolutionise the end-of-life management of composite materials and parts. In collaboration with our industry partners, we’re bringing to market some of the most innovative new fibre processing technologies ever developed to deliver real-world benefits that support the sustainability agenda.”
In addition, Cygnet is licensed to design and build the DEECOM® composite recycling system developed by new BTMA member Longworth Sustainable Recycling Technologies, the first of which was recently commissioned by the Henry Royce Institute in Manchester. DEECOM is a zero emission, low carbon pressolysis solution using pressure and steam to reclaim pristine condition fibres and resin polymers from production waste and end of life composites.
National Materials Innovation Strategy
At the start of 2025, the Henry Royce Institute announced its National Materials Innovation Strategy in the House of Commons, aimed at further boosting an integrated approach to materials science that can address critical national challenges and boost economic growth.
“UK decision makers are now looking to support machinery innovation and development where it is intrinsic to realising the vision of the government-backed strategy,” observes Kent. “The BTMA is playing an active role in representing the textile machinery sector within its various expert working groups.”
Prepregging
Another new BTMA member, Emerson & Renwick (E+R), a specialist in print, forming, vacuum and coating technologies, also supplies technology for the production of carbon fibre prepregs.
Its most recent 1.7-metre-wide line supplied to a customer in Italy operates at speeds of 40+ metres/min for web coatings or prepreg fibre and resin consolidation, or a combination of both processes. It is distinguished by an ultra-precise three-roll reverse roll coater for the processing of high viscosity thermo-activated resins and enables the automatic changeover of sensitive woven fabric materials at zero tension, with three high precision calendaring nips with hot/cool plates. Multiple unwind and rewind systems for intermediate lamination steps include side loading and reliable lap splicing and zero speed splicing with a web accumulator for the main product rewind.
E+R has also been part of a consortium working on the development of lithium-sulphur (Li-S) batteries within the £540 million UK Faraday Battery Challenge. Once commercially viable, Li-S batteries promise to provide relatively high energy density at low cost for sustainable electric vehicles of the future – inevitably starting with F1.
Filament intermingling
Resource efficiency in the processing of extremely expensive carbon and aramid fibres is a key benefit of the latest splicing technologies of Airbond.
Pneumatic yarn splicing is a process established in the textile industry for joining yarns and works by intermingling individual filaments closely together, to make joint which are stronger and flatter than knots.
The patented splicers in Airbond’s latest range are 3D printed, making them both lighter and stronger than competing products. They now enable the splicing of yarns in sizes of up to 16,000 tex – compared to the 1,200 tex most splicing machines can handle.
Carwyn Webb, technical director, Airbond, says: “We are continuing to find new partners in the wind turbine, hydrogen and aerospace industries and are doing a lot of developmental work with research institutes and universities.
“This is leading to us expanding our portfolio and we are currently working on systems for carbon tape splicing, for example, as well as an automated system for full weaving beams.”
Medical devices
Fibre Extrusion Technologies (FET) works closely in collaboration with its customers on the development of specific multifilament, monofilament and nonwoven polymers and fibres for niche applications – over 70 to date – and designs the bespoke fibre extrusion and spunbond and meltblown nonwoven systems to successfully produce them.
Following the opening of its expanded Fibre Development Centre at the start of 2023, with considerably enhanced facilities more than doubling capacity and increasing efficiency, FET has also significantly accelerated the number of technical trials it has conducted for clients.
One particularly successful area for the company has been in melt spinning systems for the production of precursor absorbable yarns that go into all kinds of implantable medical devices.
“We’ve built up a solid client base in this field, where regulations and validation are particularly important and establishing trusting and reliable partnerships is crucial,” says FET managing director Richard Slack. “We’re currently working on an exciting new parallel development we believe will be game changing for the medical devices industry, and we’ll be announcing full details prior to ITMA Asia in Singapore this October [2025].”
Simple, fast and intuitive
Sophisticated systems for the testing of fibres and advanced materials are also the speciality of key BTMA members such as James Heal, which has established strong ties with major producers of technical textiles over many years and with its latest Performance Testing collection of instruments has put the emphasis on making testing simple, fast and intuitive.
The latest James Heal AirPro air permeability tester is used to test the resistance of the flow of air through woven, knitted or nonwoven textiles. Its software offers flexibility with standards and comprehensive reporting options and different test head sizes are available, making it suitable for a range of applications and standards.
The HydroView hydrostatic head tester is meanwhile designed to measure the penetration of water in materials which have an end use that requires water resistance, such as those in the medical, geotextiles and nonwovens sectors. It is also proving essential in the testing of end-use applications for technical textiles ranging from protective gloves, diving suits and winter sports apparel to fishing waders, roofing, tenting, ground sheets and more.
Water repellency is another important function of technical fabrics from a safety and comfort perspective and with the TruRain, James Heal has reduced the volume of wastewater and energy consumed in water repellency tests to a fraction of that of competing products.
Visual accuracy
Colour is the prime focus of VeriVide and its systems are widely employed by manufacturers of technical textiles for end-use applications. These include automotive, aerospace and other transport interior materials, seat belts, airbags, helmets and gloves, and even medical implants and prosthetics where colour accuracy remains important.
For non-contact colour measurement and digital imaging, VeriVide’s established DigiEye system collects and processes data that can be communicated and shared instantly, enabling manufacturers, producers and processors to speed up quality control, sustain product integrity and reduce waste. DigiEye also enables the non-contact measurement of curved and textured parts and provides objective and accurate colour data.
Patterned fabric inspection
The precise detection of defects during the production of technical fabrics has recently been significantly advanced with the introduction of the latest WebSpector automated fabric inspection system by Shelton Vision.
Building on its market leading vision system for plain, single colour textiles, Shelton’s patent-pending image processing techniques now recognise and adapt to complex patterns such as camouflage and even on fabrics with significant distortion and deformation.
Fabrics are not rigid and can be sheared or stretched while also being subject to local distortion, but the WebSpector system now successfully deals with such anomalies in real time to provide a reliable inspection process at the same levels as plain fabric.
The unique and advanced software techniques ensure a totally clean image, allowing the full detection of faults on fabrics running at high speeds.
While the automotive interiors and one-piece woven airbag sectors remain major destinations for this advanced technology, further finished fabric WebSpector systems are now currently being supplied to manufacturers of performance wear and high-end fashion, denim, outdoor upholstery, sunscreen, mattress ticking, window dressings and even carbon fibre composites.
From lab to line
Meanwhile, what Shelton is doing for defects, C-Tex is also doing for inline colour variations, either from an approved standard or within a batch.
Rob Ricketts, C-Tex managing director, explains: “What mills would typically do in the past is take a colour swatch from a fabric production run every 200 metres or so, and hope that it represents the entire run. What we are doing is now taking a lab capability and putting it into production.”
Working with Shelton, C-Tex has now combined fabric fault detection and colour variation as key quality components of batches.
“How people have used our technology before has been within departments and they have kept that quality control knowledge very close to their chests,” Ricketts says. “What’s happening now is this data is being seen across a full supply chain. So, when a fabric leaves the textile mill and is delivered to the garment, car seat or sofa maker, they know exactly what’s coming to them and if they can produce what they need from that batch, given the recognised defects and colour variations.
“This visibility is a big breakthrough. It already happens a lot more freely in the automotive industry, for example, but now it’s coming to technical textiles supply chains too.”
Towards ITMA Singapore
“Many BTMA members are currently developing new technologies, either in-house or increasingly through joint projects, and there will be much to reveal by the time of ITMA Asia in Singapore this October,” says Kent in conclusion. “There’s a new spirit of openness and adventurous interaction in the UK right now – especially in the fields of technical textiles and composites – which I find very encouraging.”
Founded in 1940, the British Textile Machinery Association actively promotes British textile machinery manufacturers and their products to the world. The non-profit organisation acts as a bridge between its members and the increasingly diverse industries within the textile manufacturing sector.
Have your say. Tweet and follow us @WTiNcomment