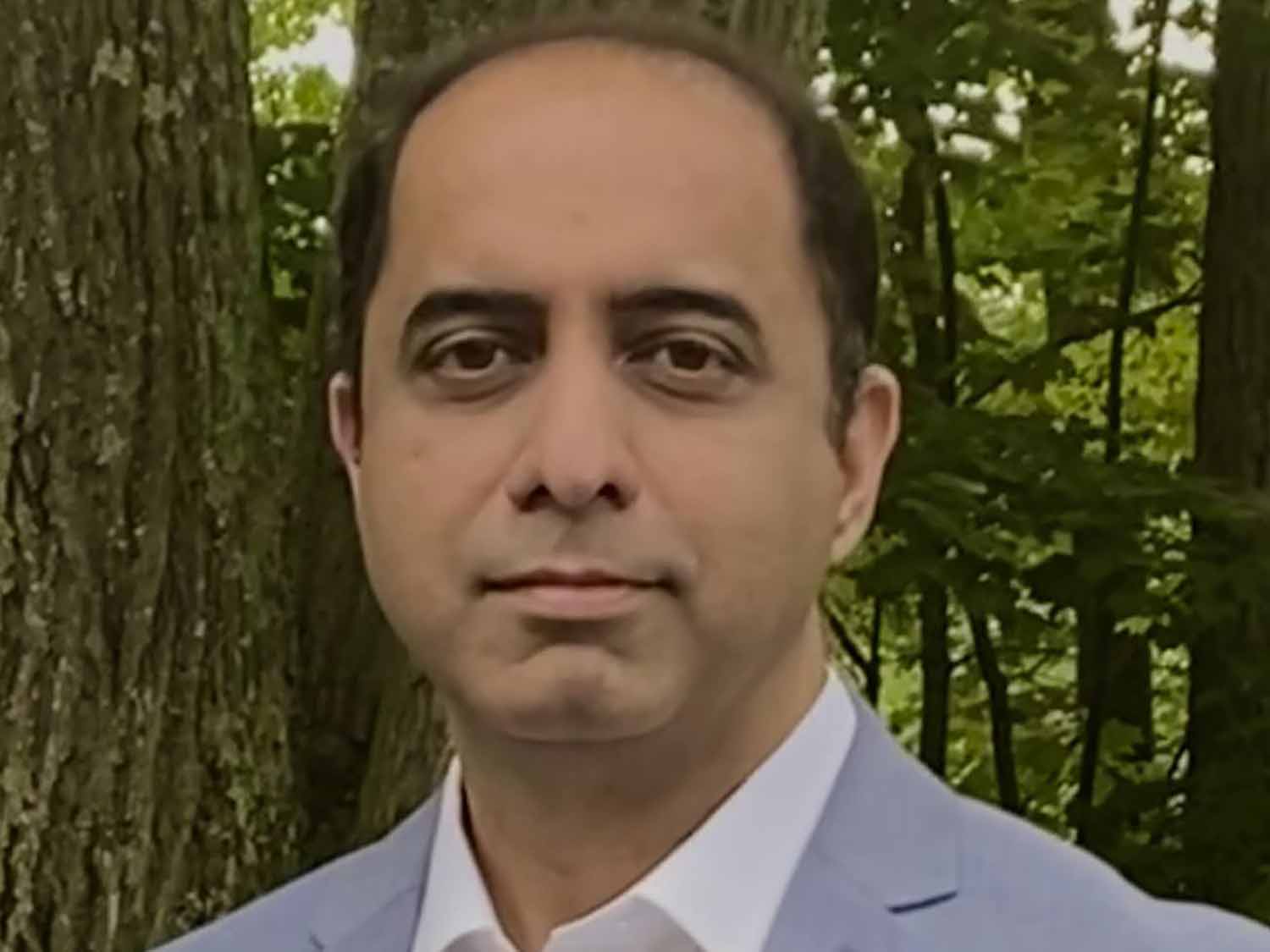
The Textile Innovation Podcast speaks with Sadavarte Samit, director of business development (new markets) at The Haartz Corporation.
The Haartz Corporation is leader in highly engineered and uniquely designed convertible toppings and interior surface materials. Headquartered in North America, with additional manufacturing in Germany and India, Haartz is working towards eliminating per- and polyfluoroalkyl substances (PFAS) from fabrics and finishes.
Haartz is the exclusive North American licensee of the Green Theme Technologies EMPEL™ process—a PFAS-free textile treatment. In this episode Sadavarte explains how PFAS-free alternatives like C0 chemistry have gained traction but can fall short when it comes to water repellency and durability, for example.
We discuss how Empel delivers water repellency, breathability, durability, and soft hand feel without introducing toxic chemicals into the supply chain. Sadavarte also touches upon advancing PFAS-free solutions into the textile supply chain.
He also speaks about challenges and opportunities sustainable and environmentally friendly alternatives to PFAS brings to the textile industry. To learn more please visit haartz.com.
You can listen to the episode above, or via Spotify and Apple Podcasts. To discuss any of our topics, get in touch by following and connecting with WTiN in LinkedIn, or email aturner@wtin.com directly. To explore sponsorship opportunities, please email sales@wtin.com.
Have your say. Tweet and follow us @WTiNcomment
-
Transcript
This transcription has been AI generated and therefore may have some inaccuracies.
Ep. 126: PFAS-free textile treatment
The Textile Innovation Podcast speaks with Sadavarte Samit, director of business development (new markets) at The Haartz Corporation.
WTiN: Hello and welcome to Textile Innovation, hosted by WTiN. My name is Abi and I'm the Features Editor and your podcast host. Each month we will be joined by a special guest. So join me and my colleagues as we deep dive into what's new, what's interesting, and what unmissable innovations have hit the market recently. We cover everything on the podcast, from sustainability to startups and the latest research and development. Plus, we quiz the experts in the field about their products and ideas across the huge spectrum that is the textile industry. So no matter what your interest is, WTiN has you covered and we can connect you to everything you need to know right here from our central hub in the UK.
Today I am joined on the podcast by Samit Sadavarte, Director of Business Development at The Haartz Corporation. Haartz is the exclusive North American licensee of Green Theme Technologies MPEL process. This is a PFAS-free textile treatment that is said to outperform traditional C0 finishes. As the textile industry works towards eliminating PFAS from fabrics and finishes, Samit discusses how performance can be maintained. He speaks about the industry moving toward sustainable and environmentally friendly alternatives and touches upon the challenges and opportunities that this brings.
Hi Savit, thank you so much for coming on WTiN's Textile Innovation Podcast. Please could you tell our listeners about The Haartz Corporation and its work within apparel textiles such as outerwear and footwear.
Sadavarte: Well, first of all, thank you for having me on the podcast. Glad to be part of this. Well, regarding Haartz, Haartz is a leading manufacturer of automotive trim, interior trim material, and also the convertible topping material. Well, founded in 1922, we have now been in business for 103 years now. We are now applying this century of textile experience in industries like outdoor apparels, protective wares, technical textiles. So we're trying to use all the technical know-how that we have learned from our automotive heritage into these new areas.
I can give you some examples. So, on the convertible topping, we would want the exterior convertible top to be a highly durable water repellent. So we are using our same learnings in that area to apply it on outdoor apparels as well, making sure that you know the outdoor apparel is comfortable, highly durable. Another example that I can think of is synthetic leathers. So the automotive interior trims are wrapped with synthetic These are the soft components that you would see on the instrument panels and door panels. So we're using that same technology to see if we can adapt on the footwear side. So we are working on projects where we can replace cattle hide and use more of a sustainable synthetic leather, a lightweight synthetic leather, without giving any abrasion or poor performance. So keeping that performance level high and using synthetics in these applications. So yeah, I mean, overall, we're certainly serving the automotive industry, but at the same time now using this in other industries as well.
WTiN: That sounds really great. Thank you. And you touched upon it then about sustainability. A mission of Hearts is to eliminate PFAs for fabrics and finishes. Could you tell me a bit more about this as a challenge and the biggest barriers facing the textile industry?
Sadavarte: Yeah, certainly. You know, the challenge, PFAS has been used for years and it's certainly a challenge to replace PFAS containing finish with, you know, the non-PFAS. The biggest challenge is the durability and the performance that the PFAS chemistries were giving. There has been quite a bit of work now done on the non-PFAS finishes, which is slowly getting to the level where it would meet the standards of the PFAS-containing finishes. In terms of the barriers, I think the key barrier is understanding the requirements and the specifications more closely. What I have seen is some of the test methods that were developed were more designed using PFAS finishes in consideration, but instead of using those test methods, we would want to use more of test methods that can be more relatable to the real world. So those would be the barriers, I would say. I mean, we would have to look at the test methods and make sure that we're using the right test methods to quantify these non-PFAS finishes.
WTiN: Could you tell us a bit more about CO chemistry and why that has gained traction in the US? Apologies if I haven't pronounced that correctly.
Sadavarte: Yeah, yeah, C0 are, you know, people would also call it the non-PFAS. Non-PFAS, I would say, is a more appropriate term, but C0 term has been more popular. I would say, you know, this development has been going on for several years. This C0 technology has certainly evolved, and I feel it's continuing to mature. The key is that in the US, there are already state bans in effect, and that has expedited the transition of these finishes from C6 to C0. The textile finishers have slowly adopted the C0 finishes, but there's certainly a performance and durability gap there. And I think that's where the Empel makes a big difference, makes a big impact, where it can actually bridge the gap.
WTiN: Makes sense, and that leads me really nicely onto talking about your use of green theme technology’s Empel process. Can you tell us a bit more about why Haartz has opted for this over the non-PFAS C0 chemistry?
Sadavarte: Haartz has adopted both the standard C0 finish as well as the green theme. Standard C0 finishes is more for articles that require water repel properties, but Empel is delivering the highest performance and high durability. So that's where parts is putting a lot of effort. So let me get into a little bit more details between the standard finish and the impel finish just so that we can properly understand the differences between the two. So the C0 finish or the non PFAS finish, most of these finishes are applied using traditional dip pad process. This is essentially a water-based dispersion, which contains C0 chemistry. This chemistry is applied with the dip pad, where the fabric is saturated with this finish, and then it gets into a tenter frame and we drive off all the water. What the C0 finish does is it's actually forming a film onto the fibers, the yarns, and then providing the water repellency. The big difference between Empel and the C0 is, at Empel, we apply the finish using gravure coating. So with gravure coating, we are getting very uniform and consistent chemistry laid down onto the textile. And then we are taking this coated roll and putting it in a hyperbaric pod where we are introducing high pressure using nitrogen, and we are pushing out all the oxygen from the pod. The whole idea here is to cross-link or polymerize this chemistry directly onto the fiber level. So what we're trying to do over here is we are encapsulating these fibers with the with the impel chemistry and That is the key difference. So because of this we are seeing good durability because we have got more surface area covered as well as good breathability So rather than forming a film over the fibre and causing poor breathability, we are encapsulating these fibres and overall performance. So that's the big key difference between the C0 and Empel.
WTiN: Thank you so much for explaining that. And in your opinion, what are the benefits of using Empel in apparel, like you said, touching upon like technical textiles, outwear and footwear?
Sadavarte: Well, the big difference is the high performance. So for the outdoor apparel, you're looking for extreme high water repellency. You would not want to have that rain jacket and, you know, get it soaked. So that water repellency is extremely important. What we have found out using aggressive test methods is that the overall water absorption after a simulated rain shower using Wendell's Spring test method, we see that the fabrics finished with Impel as a much lower water pickup. So essentially we are not soaking this fabric with water. So it stays dry after the Bundesmann test. The other big advantage that we have seen is we have then taken these fabrics and washed it using home laundry cycles, anywhere from 30 to 50 cycles. And we are not seeing any degradation of this finish. So the performance of that textile or that garment or that article stays consistent even after wash. So great wash durability, great water repellency to start with. And the other big advantage that we have noticed is its water barrier properties. So with the Bundesmann, we also look at how much water passes through the product. And we're seeing that the textiles which are finished using Impel has very low water pass-through compared to the traditional standard C0 finishes. Well, these are the key, but a few other things that I have noticed is cleanability. As I mentioned with the Empel finish, we are encapsulating these fibers with this chemistry. And what it offers is that the stain that is applied onto the textile, it's easier for it to release and clean. These are very good properties when it comes to outdoor apparel. On the footwear side, this is an application which goes through high flex. What we have seen is textiles that are used in footwear require high, low wicking. So you don't want that capillary action of water from getting into your shoe. So we tested Empel treated fabrics in the footwear application and we have seen very good wicking performance under high flex applications as well. So yeah, I mean there are several advantages that I listed and these are very important properties when it comes to outdoor applications.
WTiN: Yeah, that's great. Thank you so much. And looking from a different lens, could you maybe give us an overview of why Empel’s process is so much better for the environment in comparison to traditional PFAS?
Sadavarte: Sustainability is, I would say, the big factor why Empel is so better as well. So, well, to begin with, Empel is PFAS-free, so there is no fluorocarbons used in this chemistry. But the key difference I would say is MPEL is a water-free process as well. So it's actually a dry finish. So we are not using any water, and water is also a resource that we are, from a sustainability perspective that we need to care for. There is only so much water in the well. So this process is completely dry. If I compare that with the standard finish, the standard finish is a water-based dispersion, which contains close to 90% of water. So all of that water is saved. But the other key factor is this water needs to be dried out. So this fabric actually gets into forced air hot ovens, which are fueled by natural gas.
For Empel, this is a dry finish so we are really not driving off any water. So there is a huge benefit over there. So we did a carbon footprint comparison between the two processes. One is the traditional dip pad dry process versus Impel, which is we start off with a dry finish and then we polymerize under high pressure and conditions. We saw that the carbon footprint for Impel process is almost one-tenth compared to a traditional finish. So these are the big factors to consider when we are comparing these finishes for environmental and sustainability aspects.
WTiN: And you've touched upon it, you touched on it previously about testing everything. Could you tell us more about the Bundesmann testing that you use? I apologise again if I have pronounced that wrong.
Sadavarte: No, I think you said it pretty well.
WTiN: Amazing.
Sadavarte: So, as I said, we've been in this textile industry for over 100 years and most of the initial developments were based on an AATCC test method. So this is a spray test, but the big difference between a standard spray test versus the Bundesmann spray test is that the Bundesmann is more closer to the real world exposure. So in an AATCC, what you're doing is you're taking 250 milliliter of water and you are spraying that water using a nozzle which has 12 holes from a distance of almost 15 centimeters. And it's a quick test of about 30 seconds versus Bundesmann. This is the simulated drain shower, which is where we are using a spray head which has 300 nozzles instead of 12 that is used in an ATCC spray. And that spray, that water is dropping from almost 150 centimeters compared to 15 centimeters, so 10 times more height. So that impact is very rigorous. And then the abundance bund also is a 10-minute test, so a lot longer test, and we are using a lot more water. I would say this is one of the harshest test standard when we compare for water propulsion. The other reason why I like Bundesmann is because we are not just doing qualitative analysis where we are comparing these samples based on visual ratings, but we are also doing a quantitative analysis. So the Bundesmann process, we are actually measuring the amount of water the fabric absorbs and also the amount of water that is passed through the fabric. We collect all the water that passes through the fabric and we measure that as well. That gives a clear information and you can use that to develop better products that way. So we are not just comparing something which is less rigorous, we're comparing something which is more rigorous and more closer to the real world.
WTiN: Yeah, that sounds great. Thank you. And looking at the real world, with mounting regulatory pressures with more states and countries moving to restrict PFAS in textiles, what opportunities do you see for Haartz, Empel and similar technologies?
Sadavarte: The mounting pressures, certainly, you know, that's important. I mean, there are, as I mentioned, standard C0 finishes available. But, you know, Empel is a solution which gives you that high performance and high durability. We're seeing that gap, and as I mentioned to you earlier, Impel is actually bridging that gap between the standard finishes and we're getting much better performance. The key areas would be the breathability, the durability, and sustainability. These, the consumers or the customers would consider those key areas important, they would certainly want to consider MPEL for those applications.
WTiN: With manufacturers needing scalable, compliant, and consumer-ready PFS alternatives, what needs to change in the industry for this to happen, in your opinion? Like, for example, does more testing, such as the Bundesmann need to be adopted? Does there need to be more investment in R&D for sustainable fabrics and finishes? Yeah, if you could give me your opinion, that'd be fantastic.
Sadavarte: Absolutely. Yes, we definitely need to shift from the traditional performance measuring methods like AATCC that I just mentioned. Another test method that I would point out is an oil holdout test method. So the non PFAS finish, which is fluorine free, they do not fare well for oil repellency. But I think we need to focus more on methods that is focused on oil resistance. So there are applications where repellency is not important, but oil resistance is more important. And I'm going to give you an example. It could be the outdoor apparel where you're looking for more of the stain release properties. Some of these stains are oil-based stains. So we're not looking for repellency there, but we're looking to see if these oil-based stains can be easily removed and cleaned. And then we can continue to keep that high water repellency. So I would say, yes, we got to do more of, you know, the real world testing, things like abundance, things like cleanability, which are more closer to the application. We need to design the product in the right fashion as well so that we can use these non PFAS finishes. And in general, I think we need to give more importance on wash durability as well. You would want this finish to last more. Some of the, for that matter, even the PFAS finishes that we have seen, these are applied on the textile in the forms of film, but when it gets washed, these finishes come off. After five washes or so, this article, the garment or bags or whatever, is no longer a water repellent surface. That's where I think outshines is because this finishes is more permanent on that product because we're encapsulating those fibers well. So yeah, I think overall we need to focus on the right test standards.
WTiN: Amazing, thank you, Samit. And then my final question for you is, moving forward, how will The Haartz Corporation scale its Impel offering and what is the vision moving forward for the company?
Sadavarte: We already have a strong backing from our leadership. Hearts is committed to sustainability. We have already invested in the pilot scale and the production scale set up for the Empel in the US. There are several developments already in progress with applications associated with outdoor apparel, technical textile, and we're seeing excellent results there. These are the areas where high performance is required. What Hearts has done is it's optimistic about this technology and we have built the infrastructure around it so that we can easily scale up. So as we scale up, we should see an increase in output and an improvement in efficiency. And so that's the catch-up game that we are trying to get into, where we have to make this new technology more accessible. So that's where we have started off with one production line and have made provisions for additional lines that can be installed quite quickly. So overall, I guess I would say, you know, Harts is well positioned to offer great alternatives and Empel is definitely one of them.
WTiN: Amazing. Thank you so much. That was really interesting. I'm excited to see what comes in the future.
Sadavarte: Great. Thank you.
WTiN: Thank you so much for listening. If you have any questions or want to learn more, you can follow us on LinkedIn at World Textile Information Network, or you can contact me directly at content at WTiN.com. Textile Information Network, or you can contact me directly at content at WTiN.com. If you are interested in sponsoring an episode of the podcast, please email sales at WTiN.com.