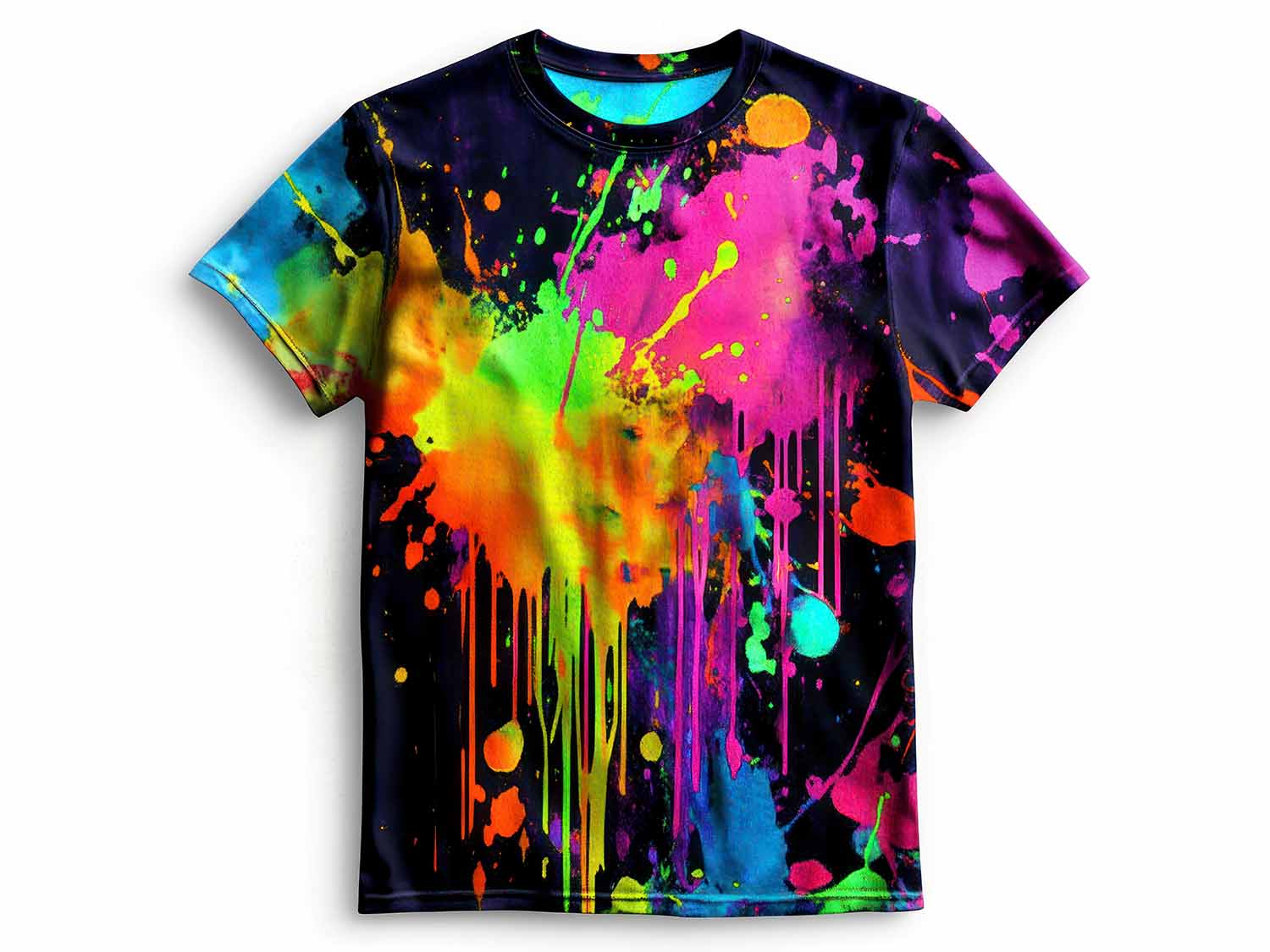
-
Understanding the commercial readiness scale
WTiN’s Commercial Readiness Scale gives an indication of what stage of commercialisation a product is at. It ranges from Emerging: a research stage development; Scaling: the product is being produced on a small but growing scale, and Commercialised: the product is well-established and ready to purchase.
Sponsored by Lubrizol
Innovation will be key in securing long-term growth in the direct-to-film (DTF) printing market. Lubrizol is responding with advanced pigment dispersion technologies that boost productivity, print quality and environmental performance.
The direct-to-film (DTF) printing industry has grown rapidly over the last five years, driven by its versatility and low entry costs. But as the market matures, competition is intensifying, and customer expectations are rising.
According to data from WTiN, global DTF print volumes achieved a compound annual growth rate (CAGR) of 21% between 2021 and 2025. However, growth will drop to 8% between 2026 and 2030, factoring in the anticipated rise in the average size of a DTF print.
Print service providers (PSPs), original equipment manufacturers (OEMs) and consumable suppliers must embrace innovation to differentiate themselves in today’s highly competitive market. In doing so, they can utilise new business models, improve output quality and target new applications to fulfil increasing consumer demands. Developments in productivity, reliability and improved environmental compliance will also unlock new opportunities for stakeholders.
Global speciality chemicals company Lubrizol can facilitate this progress with state-of-the-art pigment dispersions designed specifically for the DTF industry. Its solutions address prevalent and costly challenges in production, such as pigment particle agglomeration, which can lead to nozzle blockages and inconsistent ink application.
“Our portfolio includes conventional polymeric dispersions and advanced high-stability dispersions (HSD), which utilise polymer encapsulation to enhance pigment stability,” explains Nicholas Scheinkonig, global tech marketing manager at Lubrizol. “This results in improved jetting performance, longer print head life and higher overall throughput.”
In DTF printing, successful image transfer depends on the synergy between PET film, pigment ink and hot-melt adhesive powder. Treated films are coated to retain water-based inks on the surface, ensuring accurate drop placement, image sharpness and colour consistency. But without well-formulated inks, these coatings become less effective.
Lubrizol’s Diamond Dispersions are engineered to improve cohesion between ink, film and adhesive powder. The dispersions help control ink spread, prevent dot gain and ensure strong adhesion, resulting in vibrant, consistent prints that transfer reliably across a range of textiles.
Lubrizol offers water-based pigment dispersions designed to broaden ink formulation latitude, ensuring system compatibility and simplifying the work of the ink manufacturer. The company also offers a compatible line of inkjet binders under the Lubrijet™ tradename.
As competition increases, Lubrizol is open to working on bespoke dispersion solutions with the right partners, helping them gain a competitive edge. The company visited the recent FESPA Global Print Expo in Berlin, Germany, to learn more about new trends and the day-to-day challenges facing industry stakeholders.
“We’ve expanded our colour gamut to include red, green, orange, blue and violet, enabling broader colour profiling,” Scheinkonig tells WTiN. “We're also addressing industry demand for more reliable white dispersions through ongoing research and development (R&D).”
Lubrizol plans to launch a new white dispersion designed to reduce settling and improve re-dispersibility, further supporting consistent print performance. “Our R&D team is focused on delivering solutions that meet market needs,” Scheinkonig adds, “with more details to be announced soon.”
Meanwhile, the market is shifting towards larger, higher-quality prints produced with less ink, aligning with wider demands for supply chain transparency and environmental responsibility. DTF has come under fire for its environmental impact, especially the increasing amount of non-recyclable film it uses; total annual film consumption is forecast to surpass 645 million square meters by 2030.
Lubrizol’s high-stability dispersions can increase productivity and lower ink consumption through improved ink open time and start-up. The company is also setting the standard for sustainability by encouraging PSPs and ink manufacturers to collaborate with partners who share this value.
“All of our dispersion products are manufactured at our modern facility in Barnsley, UK,” Scheinkonig concludes. “Recent investments in solar panels and an upgraded chiller system have helped reduce our reliance on fossil fuel-based energy and lowered our overall consumption.”
Have your say. Tweet and follow us @WTiNcomment